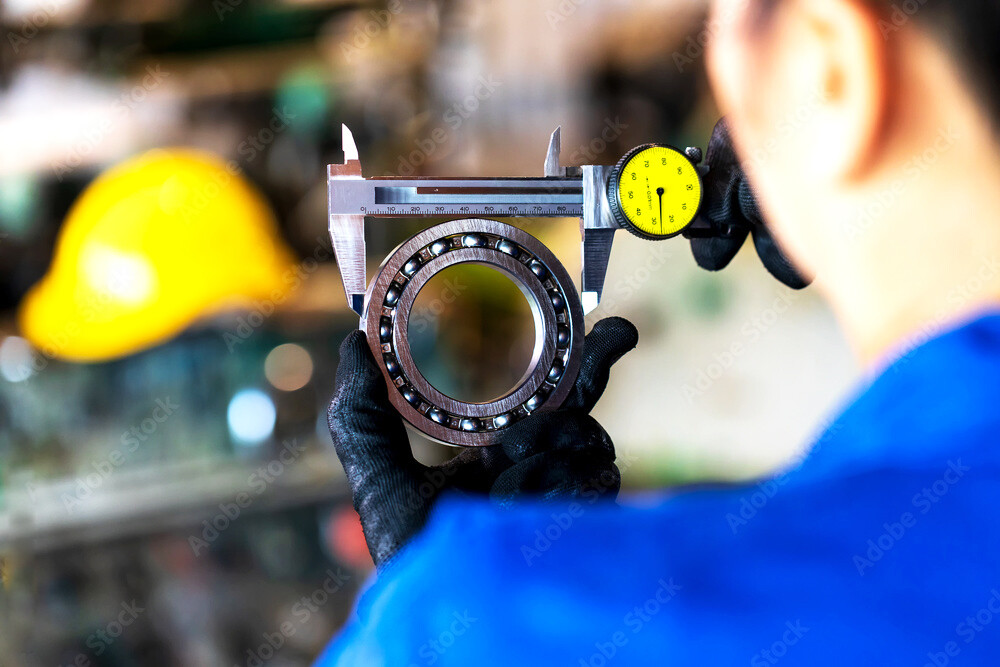
Bearing Manufacturer & Supplier
Specialize in ball bearings, roller bearings, thrust bearings, thin section bearings etc.
Everything You Should Know About Ball Bearings
Bearings are one of the most critical components in any industrial machinery. These high-precision components are critical to reducing friction and carrying loads during rotational motion. There are thousands of types of bearings on the market, including ball bearings, cylindrical roller bearings, tapered roller bearings, needle roller bearings and bearing units. While ball bearings are the most common type of bearing, each type has its own characteristics and benefits that make it suitable for certain uses and applications and not for others in operating environments.
Now, AUB Bearing Manufacturing Co., Ltd. summarizes all the information of ball bearings based on years of bearing manufacturing experience. Ball bearings are rolling bearings that use rolling balls held between inner and outer raceways to support radial and axial loads acting on rotating and reciprocating shafts. These ball bearings are used to provide smooth, low friction motion in rotating applications. They provide high performance and long life, transferring load from the balls to the inner ring. In this article, we will discuss the different types of ball bearings.

Table of Contents
ToggleBall Bearing Designing
Ball bearings consist of four main parts which are: 2 rings/races, balls (rolling elements) and retainers (ball separators).
The outer ring is fixed and mounted in the housing. The outer ring also assists in the transfer of radial loads from the bearing to the housing. The inner ring supports and guides the shaft during rotation and is mounted on the rotating shaft. The function of the rolling elements is to carry loads and distribute them throughout the raceways.
The rolling elements rotate at a different speed than the inner ring, but they rotate around the inner ring. The keeper acts as a barrier that prevents the balls from colliding with each other. Thrust bearings are subjected to loads parallel to the axis of rotation, called axial loads. Thrust ball bearings consist of two rings of equal size.

Types of Ball Bearings
According to the design and structure of the ball bearing, it can be divided into several types. Common designs of ball bearings are described below. Read on to learn about the different types of ball bearings and their uses.
Single row angular contact ball bearings
Double row angular contact ball bearings
Four-point angular contact ball bearings
Single row deep groove ball bearings
Double row deep groove ball bearings
Double direction thrust ball bearing
Double ball bearing

Angular contact ball bearings are designed so that the bearing forms a contact angle between the races and the balls when the bearing is in use. The main design feature of this type of ball bearing is that the shoulder of one or both rings is higher than the other. In order for these bearings to function properly, thrust loads must be applied during assembly. This load (or preload) creates a contact line (or contact angle) between the inner ring, balls and outer ring. Preload can be built into the bearing or it can be created when the bearing is inserted into the assembly. Contact angles vary from 15° to 40° and are measured relative to a line perpendicular to the bearing axis. Angular contact ball bearings have inner and outer ring raceways that are displaced relative to each other in the direction of the bearing axis. This means that these bearings are designed to accommodate combined loads, i.e. radial and axial loads acting simultaneously. These types of ball bearings are available in different design styles, with seals or shields. Not only do they prevent contamination, they also act as a retainer for lubricants. These bearings can be made of stainless steel, ceramic hybrid or plastic and can be chrome, cadmium or other plated. In addition, they can be pre-lubricated, re-lubricated or have solid lubrication capabilities. Angular contact ball bearings are further divided into the following subtypes:

Single Row Angular Contact Ball Bearings
These bearings use a large number of balls to provide relatively high load carrying capacity, can only accommodate axial loads in one direction, are usually adjusted for a second bearing, and have non-separable bearing rings.
The advantages of single row angular contact ball bearings include:
High carrying capacity
Good running performance
Easy to install universally matchable bearings
Double Row Angular Contact Ball Bearings
With a design corresponding to two single-row bearings arranged back-to-back, but where two single-row bearings take up too much axial space, they can accommodate radial and axial loads in either direction and tilting moments. The advantages of double row angular contact ball bearings include:
Less axial space
Accepts radial and axial loads in either direction
Accommodates tilting moments
Rigid bearing arrangement

Four point angular contact ball bearings
Four-point angular contact ball bearings are designed to support axial loads in two directions and have high load carrying capacity, can support limited radial loads for a given axial load, use less axial space than double row bearings, and is separable.
The advantages of four point angular contact ball bearings include:
Suitable for axial loads in both directions
Less axial space
High carrying capacity
Separate design
Improved oil flow
Limited inner ring deformation when subjected to high clamping forces

Deep groove ball bearings are the most common type of ball bearing and can be purchased in sealed, shielded and snap ring configurations. The dimensions of the races in these types of bearings closely match the dimensions of the balls contained. They are also great for supporting heavy loads. Deep groove bearings provide radial and axial support. However, there is no way to adjust the contact angle to change the relative level of such loading. Deep groove ball bearings are further divided into the following subtypes:
Single Row Deep Groove Ball Bearings
Single row deep groove ball bearings are the most common type of ball bearing. They are used very widely. The raceway grooves of the inner and outer rings are circular arcs with a radius slightly larger than that of the balls. In addition to radial loads, axial loads can also be applied in either direction. Due to their low torque, they are ideal for applications requiring high speed and low power loss. Also, for open bearings, these are usually fitted with steel shields or rubber seals on one or both sides and are pre-lubricated with grease.

Double Row Deep Groove Ball Bearings
Double row deep groove ball bearings correspond in design to single row deep groove ball bearings. Their deep and continuous raceway grooves are tightly integrated with the balls, enabling the bearings to withstand radial loads and axial loads in both directions. These types of ball bearings are well suited for bearing arrangements where the load carrying capacity of single row bearings is insufficient. For the same bore and outside diameter, double row bearings are slightly wider than single row bearings in the 62 and 63 series, but have a much higher load carrying capacity. Double row deep groove ball bearings can only be used as open bearings (no seals or shields).

Thrust ball bearings are designed for pure thrust loads. These bearings can accommodate little or no radial load. Rolling elements can be balls, needles or rollers. Slewing rings or turntable bearings can accommodate axial, radial and moment loads. They are not mounted on the housing or shaft, but directly on the surface of the base. Both the inner and outer rings have mounting holes. The inner ring, outer ring or both can have integral gears. These bearings are known as table bearings, turntable bearings and slewing rings. Thrust ball bearings offer low noise, smooth operation and capability for high speed applications. They can be used as one-way or two-way bearings, the choice depends on whether the load is one-way or two-way.
Single Direction Thrust Ball Bearings consist of a washer-like bearing ring with raceway grooves. The ring connected to the shaft is called the shaft ring (or inner ring), and the ring connected to the bearing housing is called the seat ring (or outer ring).
In a double direction thrust ball bearing, there are three rings and the middle ring (the center ring) is fixed to the shaft. There are also thrust ball bearings with an aligning seat washer below the housing washer to compensate for shaft misalignment or mounting errors. Stamped steel cages are typically used for smaller bearings, while machined cages are used for larger bearings.

Duplex Ball Bearing
A combination of two angular contact ball bearings forms a duplex bearing. Possible combinations include face-to-face, which have the outer ring faces together (type DF), back-to-back (type DB), or both front faces in the same direction (type DT). DF and DB duplex bearings are capable of taking radial and axial loads in either direction. Type DT is used when there is a strong axial load in one direction and it is necessary to impose the load equally on each bearing.
Now that you got familiar with the common designs of ball bearings, let’s get to know the construction types of ball bearings.
Conrad Ball Bearing
These types of ball bearings are assembled by placing the inner ring into an eccentric position relative to the outer ring, with the two rings in contact at one point, resulting in a large gap opposite the point of contact. The balls are inserted through the gap and then evenly distributed around the bearing assembly, causing the rings to become concentric. Assembly is completed by fitting a cage to the balls to maintain their positions relative to each other.
Conrad bearings can withstand both radial and axial loads but have the disadvantage of lower load capacity due to the limited number of balls that can be loaded into the bearing assembly. Probably the most familiar industrial ball bearing is the deep-groove Conrad style. The bearing is used in most mechanical industries.
Slot-fill Ball Bearing
In a slot-fill radial bearing, the inner and outer races are notched on one face so that when the notches are aligned, balls can be slipped in the resulting slot to assemble the bearing. A slot-fill bearing has the advantage that balls can be assembled, resulting in a higher radial load capacity than a Conrad bearing of the same dimensions and material type. However, a slot-fill bearing cannot carry a significant axial load, and the slots cause discontinuity in the races that can have a small but adverse effect on strength.
Self-aligning Ball Bearing
Self-aligning ball bearings have two rows of balls, a commonly sphered raceway in the outer ring and two deep uninterrupted raceway grooves in the inner ring. They are available open or sealed. These types of ball bearings are insensitive to angular misalignment of the shaft relative to the housing, which can be caused, for example, by shaft deflection.
The benefits of self-aligning ball bearings include:
Accommodate static and dynamic misalignment
Excellent high-speed performance
Minimum maintenance
Low friction
Excellent light load performance
Self-aligning ball bearings can reduce noise and vibration levels, for example, in fans.

Linear Ball Bearings
Linear ball bearings are designed to provide free motion in one direction. They are the most widely used variety of linear slides and ensure a smooth precision motion along a single axis linear design. Featuring self-lubrication technology, these ball bearings allow for optimum performance and reliability. They are comprised of two linear ball-bearing rows, integrated within four rods on alternate sides of the base.

Radial Ball Bearing
Suitable for a wide range of purposes, radial ball bearings offer exceptional levels of performance. These types of ball bearings have the capacity for either radial or axial loads as applied to the shaft. However, the combined application of such loads requires axial angular contact. Adjustment of the axial radial bearing angle allows for equal distribution of the axial and radial loads along with the angular contact ball bearings.
Relieved Race Ball Bearing
Relieved race ball bearings are ‘relieved’ as the name suggests by having either the OD of the inner ring reduced on one side of the ID of the outer ring increased on one side. This allows a greater number of balls to be assembled into either the inner or outer race, and then press-fit over the relief. Sometimes the outer ring will be heated to facilitate assembly. Like the slot-fill construction, relieved race construction allows a greater number of balls than Conrad construction, up to and including full complement, and the extra ball count gives extra load capacity. However, a relieved race bearing can only support significant axial loads in one direction.
Fractured Race Ball Bearing
Another way of fitting balls into a radial ball bearing is by radially ‘fracturing’ one of the rings all the way through, loading the balls in, re-assembling the fractured portion, and then using a pair of steel bands to hold the fractured ring sections together in alignment. Again, this allows balls, including full ball complement, however, unlike with either slot fill or relieved race constructions, it can support significant axial loading in either direction.
Bearings with a flange on the outer ring simplify axial location. The housing for such types of ball bearings can consist of a through-hole of uniform diameter, but the entry face of the housing must be machined truly normal to the hole axis. However such flanges are very expensive to manufacture. A cost-effective arrangement of the bearing outer ring, with similar benefits, is a snap ring groove at either or both ends of the outside diameter. The snap ring assumes the function of a flange.

Caged Ball Bearing
Cages are typically used to secure the balls in a Conrad-style ball bearing. In other construction types of ball bearings, they may decrease the number of balls depending on the specific cage shape and thus reduce the load capacity. Without cages, the tangential position is stabilized by the sliding of two convex surfaces on each other. With a cage, the tangential position is stabilized by a sliding of a convex surface in a matched concave surface, which avoids dents in the balls and has lower friction.
Hybrid Ball Bearing
Ceramic bearing balls can weigh up to 40% less than steel ones, depending on size and material. This reduces centrifugal loading and skidding, so hybrid ceramic bearings can operate 20% to 40% faster than conventional bearings. This means that the outer race groove exerts less force inward against the ball as the bearing spins. This reduction in force reduces the friction and rolling resistance. The lighter balls allow the bearing to spin faster and use less power to maintain its speed.
These bearings make use of both ceramic balls and race. These bearings are impervious to corrosion and rarely require lubrication if at all. Due to the stiffness and hardness of the balls and race, these bearings are noisy at high speeds. The stiffness of the ceramic makes these bearings brittle and liable to crack under load or impact. Because both ball and race are of similar hardness, wear can lead to chipping at high speeds of both the balls and the race, which can cause sparking.

Materials used in ball bearings
The materials used to make ball bearings vary widely, but there has always been a major focus on the material of the rings. This ensures a coordinated interaction of the cage, outer and inner rings. This is often important when the application involves heating or cooling of the bearing. The running performance of ball bearings is important; they must be good. Below is a list of the most common materials used to manufacture ball bearings, and how they relate to the ring materials:
Higher hardness so longer life ratings
Lower cost
Good for temperatures of 120°C constant up to 150°C intermittent
Poor corrosion resistance
This is the standard steel for most ball bearings. It is harder than stainless steel meaning greater life ratings. It also has superior low noise qualities to standard 440 grade stainless steel. Chrome steel actually has a low chromium content and is not corrosion resistant. Chrome steel can tolerate continuous temperatures of up to 120°C. Above this temperature, it undergoes greater dimensional change and the hardness is affected, reducing load capacity. It can withstand up to 150°C intermittently but above this temperature, bearing life is significantly reduced.
Grade 440 Martensitic Stainless Steel (prefix "S")
Good corrosion resistance to water and many weak chemicals
Suitable for -70°C to 250°C constant temperature or 300°C intermittent temperature
Slightly softer than chrome steel and therefore lower load ratings
Corrosion in salt water or salt spray, poor acid and alkali resistance
expensive than chrome steel
resistant to corrosion due to the higher chromium content and the addition of nickel, grade 440 stainless steel is most commonly used for corrosion resistant ball bearings. Chromium reacts with oxygen in the air to form a layer of chromium oxide on the surface of the steel, which is called a passivation film. It is hardened by heat treatment and has a good combination of strength and corrosion resistance. Unlike grade 300 austenitic steel, this steel is magnetic.
The load capacity of AISI440 grade is about 20% lower than that of chrome steel, so the rating life will be slightly reduced. This grade exhibits good corrosion resistance when exposed to fresh water and some weaker chemicals, but will corrode in seawater environments or when in contact with many aggressive chemicals.
KS440/ACD34/X65Cr13 grade stainless steel with lower carbon content, compared to standard AISI440C grade, it has higher corrosion resistance, greater load capacity (approximately 10% lower than chrome steel) and excellent low noise qualities. Grade 440 stainless steel can also withstand higher temperatures than chrome steel, up to 250°C constant and up to 300°C intermittent, but with reduced load capacity. Above 300°C, bearing life is greatly reduced.
Excellent corrosion resistance to water, salt water and many chemicals
Suitable for full load temperatures up to 500°C
Suitable for cryogenic applications down to -250°C
Negligible response to magnetic fields
Expensive than grade 440 due to lower yield.
Only suitable for very low loads and low speeds
Not suitable for low noise applications
Grade 316 stainless steel bearings are used for better corrosion resistance to seawater, salt spray and certain acids/alkalis. They are suitable for very high temperature applications as the steel can be used at temperatures up to 500°C. They can also be used in cryogenic applications, as the steel remains ductile down to -250°C. Unlike 440 grade bearings, 316 stainless steel bearings are classified as non-magnetic due to their negligible response to magnetic fields, although 316 stainless steel may become magnetic after cold working.
Grade 316 stainless steel cannot be hardened by heat treatment and can only support low loads and speeds. 316 stainless steel ball bearings have significantly lower load and speed ratings than equivalent 440 class bearings. Grade 316 stainless steel exhibits good corrosion resistance in marine environments when used above the waterline or temporarily submerged when flushed with clean water. Not suitable for permanent submersion unless there is regular high velocity water flow on the bearing. This is because the passivation film on the surface of stainless steel depends on the presence of oxygen to regenerate itself. In low oxygen underwater marine environments such as stagnant seawater or under mud/silt, steel may be susceptible to pitting or crevice corrosion. 316 stainless steel is less resistant to warm sea water. Pitting corrosion is a risk in seawater above 30°C, while crevice corrosion may occur at 10-15°C. Grade 316 is still corrosion resistant than 440. Bearings made of grade 316 stainless steel can be used at high temperatures, provided that suitable cage material is used or the bearing is filled full. Polyethylene, PEEK or PTFE are commonly used for cages in 316 stainless steel bearings.
Engineering Plastic
Acetal resin / POM-C (AC)
Excellent corrosion resistance to water, salt water and weak chemicals
Non magnetic
Only semi-precision grade is possible
Temperature range -40°C to +110°C
Suitable for very low load and low speed only
PEEK (PK)
Excellent corrosion resistance to water, salt water and most chemicals
Good high temperature performance
Non magnetic
Wide temperature range from -70°C to +250°C
Semi-precision only but greater strength so suitable for higher load and speed than other plastics
Polyethylene (PE)
Excellent corrosion resistance to water, salt water and many chemicals
Extremely low moisture absorption
Non magnetic
Temperature range from -40°C to +80°C
Suitable for low load and low speed and semi-precision only
PTFE (PT)
Excellent corrosion resistance to water, salt water and most chemicals
Extremely low moisture absorption
Good high temperature performance
Non magnetic
Very wide temperature range from -190°C to +200°C
Suitable for lower loads and speeds than other plastics and semi-precision only
PVDF (PV)
Excellent corrosion resistance to water, salt water and most chemicals
Extremely low moisture absorption
Can withstand higher temperatures than acetal and polypropylene
Non magnetic
Fairly wide temperature range from -50°C to +150°C
Suitable for low load and low speed and semi-precision only
AUB’s standard polymer corrosion resistant bearings have polyoxymethylene resin (POM-C) rings, nylon (PA66) cages and balls made of 316 stainless steel or glass. They are also suitable for food applications. However, they corrode in the presence of certain chemicals, and PA66 cages absorb water after prolonged exposure, resulting in a loss of tensile strength. There are many alternative materials for rings, cages and balls such as polypropylene, PTFE, PEEK or PVDF.
All plastic bearings are semi-precision bearings and, like 316 stainless steel bearings, should not be used in precision applications. Due to the softer material, although PEEK has better load carrying capacity, they are not suitable for anything other than low loads and low speeds. PTFE, PEEK and PVDF materials vary in corrosion resistance to provide the best overall chemical resistance.
When using plastic bearings at high temperatures, care should be taken to select the correct material. Acetal bearings should not be used at temperatures above 110°C, polypropylene only up to 80°C, but other materials have good high temperature resistance, especially PTFE and PEEK, which are suitable for Temperatures up to 250°C, despite the lower load rating of PTFE. In general, plastic bearings are not recommended for vacuum applications. The exception is PEEK, which has very good outgassing properties.
Ceramics
Zirconia / ZrO2 (prefix "CCZR")
High corrosion resistance to acids and alkalis but may degrade after prolonged exposure to hot water or steam. Studies have also been carried out on low temperature degradation of zirconia in the presence of moisture or water. There is evidence of some surface weakening but the effect on bearing performance is inconclusive and not thought to seriously affect zirconia bearings at low temperatures or room temperature.
Wide temperature range from -190°C to 400°C without cage
Non magnetic and electrically insulating
Lower speed and load than steel bearings
Not suitable for low noise applications
75% of the density of steel
Higher flexural strength and lower elastic modulus than other ceramics so better for small shock loads and interference fits
Expansion similar to chrome steel and same as 440 stainless so no problem to use with steel shaft at high temperature
Very good corrosion resistance to water, salt water, acids and alkalis
Very wide temperature range from -210°C to 800°C without cage
Non magnetic, electrically insulating and suitable for use in high vacuum applications
Lower speed and load than precision steel bearings but Si3N4 balls are used in high speed hybrid bearings
Not suitable for low noise applications
40% of the density of steel
Very low thermal expansion so consider shaft/housing fits for high temperature applications
Not recommended for shock loads or interference fits
Best corrosion resistance of the ceramics
Best high temperature performance up to 1600°C without cage
Non magnetic
Electrically conductive
40% of the density of steel
Very low thermal expansion so consider shaft/housing fits for high temperature applications
Most brittle so cannot tolerate shock loads
Not supplied from stock
Full ceramic bearings are much expensive than steel bearings and are therefore often used in environments that are too harsh for steel bearings. They have good to excellent corrosion resistance, depending on the material and chemicals encountered, and are usually supplied without lubrication. They are non-magnetic and, unlike silicon carbide, they are electrically insulating. Full ceramic bearings may have PTFE or PEEK cages or be supplied as full complement types, i.e. without cages. If supplied as a complete supplement, they can be used at very high temperatures.
Since ceramics are much harder than steel, they are brittle. Steel can withstand large impacts through plastic deformation, while ceramics are prone to cracking. Therefore, full ceramic bearings, especially silicon nitride and silicon carbide, are not recommended for use where heavy shock loads are likely. Due to greater brittleness, full ceramic bearings can carry approximately 65% to 75% of the load of steel bearings. The limiting speed of full ceramic bearings is only about 25% of the speed of the same steel bearing, because the rings are less round and there is a greater risk of sudden failure due to lower bending strength compared to steel.
Using silicon nitride or silicon carbide bearings with steel shafts or housings in high temperature applications can cause assembly problems due to large differences in coefficient of expansion. If the greater expansion of the steel shaft in the ceramic inner ring at high temperatures is not taken into account, bearing damage may occur. Zirconia is less problematic because the coefficient of expansion is similar to steel. See the shaft/housing fit section for details.
Hybrid bearings (prefix “CB” or “SCB”): Silicon nitride is the most popular for the balls in hybrid bearings as it has only 40% of the density of bearing steel but is much harder giving greater wear resistance. Hybrid bearings are also capable of higher speeds due to the lower centrifugal force generated by the ceramic balls. However, due to the lower elasticity of the balls, the contact area between the balls and the raceway is smaller which causes a higher contact pressure. This can cause the raceways to wear faster. The speed increase for hybrid bearings is approximately 30-40% with adequate lubrication. Hybrid bearings can also operate better with limited lubrication but running speed should be reduced. They are also less subject to ball skidding under high acceleration with a low load.
Bearing Retainers
Bearing retainers distribute the balls evenly around the raceways to prevent ball-to-ball contact and allow for higher speeds. They also help retain grease around the balls and raceways. For greater accuracy and to prevent additional friction, it is important not to allow too much radial movement of the retainer. For this, the cage is guided by balls or one of the rings.
Metal Crown / Ribbon

These standard retainers are manufactured from carbon steel for chrome bearings and AISI304 or AISI420 grade stainless steel for stainless bearings. These were often made from brass which also offered a high temperature capability but this is much less common due to higher cost of brass and advances in steel technology.

For higher temperatures, stainless steel is usually recommended. The crown cage and ribbon cage perform the same function but the crown cage is used primarily on smaller miniature bearings and thin-section bearings where space is limited. Steel cages are preferred for arduous operating conditions and where high levels of vibration are experienced. Cages in 316 stainless steel can be fitted to full ceramic bearings from 8mm bore upwards.
Suitable for medium and low speed
Can withstand higher temperatures depending on the type of steel
Crown Type – Inner Ring Guided
Ribbon type – mainly ball guide
Reinforced Nylon Crown (TW)

This molded fiberglass reinforced synthetic cage has better sliding characteristics than steel cages and produces lower running torque fluctuations. It can increase the maximum speed by up to 60%, so it is often used in high-speed applications and has good low noise characteristics. This retainer is not suitable for cryogenic applications as it loses its elasticity below approximately 30°C. In vacuum applications it may become brittle.
High speed and low noise
Temperature range approx –
30 to +120°C Ball guided
Polyethylene crown (PE)

This low speed retainer is made of high density polyethylene (HDPE) and is used in 316 stainless steel bearings. It has very good corrosion resistance, so it can be used in the presence of sea water and many chemicals.
Very corrosion resistant
Temperature range -40 to +80°C
Inner ring guided
PEEK Crown (PK)

PEEK cages are commonly used in ceramic bearings, 316 stainless steel bearings and PEEK bearings. They are highly corrosion resistant, have a wide temperature range and are suitable for use in vacuum environments.
Very corrosion resistant
Low outgassing so suitable for vacuum use
Temperature range –
70 to +250°C Inner ring guided
PTFE Crown (PT)

This cage is used for ceramic bearings, 316 stainless steel bearings and PTFE bearings. It is highly resistant to corrosion and has a very wide temperature range.
Very corrosion resistant
Temperature range –
190 to +200°C Inner ring guided
Nylon Crown (PA)

This is mainly used in our acetal plastic bearings. Unlike the TW cage, this is not a reinforced cage so not suitable for high speeds. It is corrosion resistant but may swell after a few months if constantly used in water or a continuously damp environment.
Corrosion resistant
Temperature range -30 to +100°C
Inner ring guided
Full Complement (F/B)

A full complement (or full ball) bearing contains extra balls and has no retainer. It is used for its greater radial load capacity although axial load capacity is very small. These bearings can only be used at low speeds and bearing torque is increased due to ball to ball friction. Improved steel and hardening techniques have increased the load capacities of bearings with cages and the full complement bearing is much less common now.
Higher radial load capacity
Much lower speeds than caged type
Low axial load
Increased bearing torque
Combating common retainer problems
From lubrication failure to misalignment bearing failure occurs for a range of reasons. Retainers, however, can succumb to two common problems:
Hooping
The phenomena when the retainer wobbles like a hula-hoop causing torque spikes in the rotating assembly. The retainer should track in a true circumferential plane concentric with the pitch diameter of the balls.
Hang-up (wind-up)
When an axial load is applied to static bearings that have the axis of their shaft in a horizontal mode, the balls fall downward to a position where they are unequally spaced prior to the load being applied. When the axial load is applied it squeezes the balls between the inner and outer raceways. Now that the balls are held securely in unequally spaced positions they cause the retainer to bind. This binding is called “retainer hang-up.” Once bearing rotation commences the retainer is stressed and some of the balls may skid causing damage that will initiate premature bearing failure.
Bearing Guards and Seals
Bearings have different types of shields and seals, often called closures. These closures are not always necessary; however, shielded and sealed bearings provide better protection from contamination and help retain bearing lubricants.
Shield (ZZ)

Most of our bearings have metal shields. The shield is designed to prevent larger particles from entering the bearing while keeping the grease inside the bearing. They can be pressed into the outer ring of the bearing (non-removable) or secured by circlips (removable). Since the guard does not contact the inner race, there is no increase in starting or running torque. Guards on stainless steel bearings are usually made of AISI 304 stainless steel.
Prevent contamination by larger particles
Reduce lubricant leakage
Do not increase torque
Wide temperature range, especially for stainless steel
Contact seal (2RS)

Standard bearing seals consist of Nitrile/BUNA-N rubber bonded to a metal washer. Washers are made of SPCC cold rolled steel for chrome steel bearings or 304 stainless steel for stainless steel bearings. Some sizes are available with high temperature PTFE seals (up to 250°C) or Viton seals (up to 230°C). The inner lip of the seal rubs against the inner ring of the bearing to provide an effective seal against smaller particles such as dust and moisture while preventing lubricant leakage. Contact seals generate much higher levels of frictional torque than seals and will reduce the maximum speed of the bearing. Below -40°C Nitrile and Viton harden and provide a poor seal, so PTFE seals or metal shields should be considered for very low temperatures.
Good protection against pollution
Significantly reduces lubricant leakage
Reduced max speed by approximately 40%
Significantly increased bearing torque
Temperature. Range –40°C/+110°C for NBR
Temperature. PE range –50°C/+110°C
Temperature. Viton range –40°C/+230°C
Temperature. PEEK range –70°C/+250°C
temperature. PTFE range –190°C/+250°C
Non-contact seal (2RU )

These seals are also made of nitrile rubber bonded to metal washers, but do not rub against the inner race of the bearing and therefore have less effect on bearing torque and maximum speed than contact seals and can therefore be used in low torque, high speed applications. They Provides better protection than metal shielding but does not seal as well as contact.
Good protection against pollution
Reduce lubricant leakage
No torque increase
Does not affect maximum speed
Temperature. Range –40°C/+110°C for NBR
Temperature. PE range –50°C/+110°C
Temperature. PEEK range –70°C/+250°C
Temperature. PTFE range –190°C/+250°C
Do you need high contamination protected bearings?
For applications in the food and beverage or pharmaceutical industries, equipment must comply with strict hygiene and safety standards. In these environments, protection from contamination is critical, so it is beneficial to choose a contact seal to ensure that dirt does not enter the bearing. For equipment that handles regular washdowns, a contact seal will also provide effective water resistance. This will prevent grease from flushing out of the bearing, roller or ball slippage or overheating. Many steel bearings in this industry require the supply of non-toxic lubricants that meet NSF’s H1 or H2 standards.
Will the bearing operate under extreme temperature conditions?
Shielded metal bearings can generally withstand higher temperatures than sealed bearings. For high temperature applications, 440 grade stainless steel bearings can be used at temperatures up to 300°C. If exposed to extreme conditions, the rubber or plastic can melt, and if debris melts and enters the raceways, it can cause the bearing to fail. In these cases, shielded bearings are recommended.
At what speed will the bearing run?
For high-speed applications such as cycling and skateboarding, non-contact seals are the preferred choice. Offers better contamination protection than guards, and non-contact seals do not affect maximum speed or bearing torque.
The load rating is a guideline for the load a bearing can withstand in an application and is used in life calculations. We always express the load rating of a bearing in Kgf (kilogram force). This is the force exerted by a kilogram of mass on the Earth’s surface. Elsewhere, you may see forces expressed in Newtons. A Newton is defined as the force that accelerates a mass of one kilogram at a rate of one meter per second (or 1 m/s²). Since gravity at the Earth’s surface is 9.80665 m/s², 1 Kgf = 9.80665 Newtons, but for simplicity let’s say 1 Kgf = 10 Newtons.
Dynamic Radial Load Rating
Dynamic radial load rating is officially defined as: “90% constant radial load in a set of identical chrome steel bearings, with only the inner ring rotating, for one million revolutions before showing signs of fatigue.”
One million rpm does sound like a lot, but let’s take a closer look. If you run at about 10,000 revolutions per minute (rpm) and apply maximum dynamic load, the bearing will only last a little over an hour and a half (100 minutes).
These numbers are used to calculate rating life, but in normal applications bearings should not be subjected to anywhere near such loads unless you don’t expect them to last very long.
If long life is required, it is best to limit the actual load to between 6% and 12% of the dynamic load rating of the bearing. Can withstand heavier loads, but life will be shortened.
AISI440C/KS440 stainless steel bearings will support approximately 80% – 85% of the load figures of chrome steel bearings. Thrust bearing load ratings are based on a constant axial load of one million revolutions. AUB Bearings’ team of experts can help provide rating life data for a wide range of different bearings.
Rated static radial load
Static radial load ratings are pure radial loads (or axial loads for thrust bearings) that cause complete permanent deformation of the balls or raceways.
Static loads close to this number may be acceptable for some applications, but not where any smoothness or accuracy is required. Static load ratings for stainless steel bearings are approximately 75% to 80% of those for chrome steel bearings.
The load capacity of a bearing may be limited by the lubricant. Certain lubricants are only suitable for light loads, while others are designed for high-load applications. Full complement bearings have higher load ratings . The axial load capacity of radial ball bearings can be increased by specifying loose radial clearance.
Rated axial load
Heavy duty bearing types such as the 6200 or 6300 series can accommodate axial loads up to 50% of the rated static radial load. Due to the shallow raceways, thin-walled deep groove ball bearings can only accommodate axial loads between 10% and 30% of the bearing’s static radial load rating.
Note that these figures are based on pure axial loads. Additional radial loads or moments (misalignment loads) will affect the axial load capacity. Exceeding the total recommended limits for combined loads will have an adverse effect on bearing life.
Full complement ball bearings have a filling groove machined in the inner and outer rings. Under axial loads, the groove interferes with ball rotation, so full complement bearings are not recommended for axial loads.
Bearing Life
The calculated life of a bearing is based on its load, operating speed and environmental factors. Industry standards typically require 90% of bearings to be serviceable after 1 million revolutions and 50% of bearings to be serviceable after 5 million revolutions. This is known as bearing fatigue life. Bearing life is often underestimated (for safety reasons) and the applicable variables used to calculate such life.
It can also be done with the following formula:


Ball bearing internal clearance
Internal clearance or radial clearance is the amount of looseness between the balls and raceways of a bearing.
Radial clearance is the clearance measured perpendicular to the bearing axis, or specifically: average outer ring raceway diameter minus average inner ring raceway diameter minus (2 x ball diameter).
Axial clearance is the clearance measured along the axis of the bearing, called axial clearance. The axial play is approximately 10 times the radial play value.
The radial play in a bearing before installation can be referred to as the “initial” radial play. The “residual” or “running” radial clearance is what remains after the bearing is installed. Ideally, the residual radial clearance in the bearing should be zero to minimize ball slippage and reduce axial play (end play), so it is very important to choose the initial radial clearance correctly.
During installation, there are many factors that can change the radial clearance. A tight shaft fit (commonly called an interference fit or press fit) in which the shaft is slightly larger than the inner ring of the bearing will stretch the inner ring, making it larger. This reduces the radial play of the interference fit by up to 80%. A similar situation can occur if the outer ring is a tight fit with the housing. The difference between shaft and case temperature can also be a problem. If the inner ring of the bearing is hotter than the outer ring, it will expand and reduce the radial clearance. This can be calculated as follows:
Chromium steel: 0.0000125 x (inner ring temperature – outer ring temperature °C) x outer ring raceway diameter* in mm.
440 stainless steel: 0.0000103 x (inner ring temperature – outer ring temperature °C) x outer ring raceway diameter * (mm).
* The outer ring raceway diameter can be roughly calculated as: 0.2 x (d + 4D) where d is the bore in mm and D is the outside diameter in mm.
There can also be problems, e.g. the shaft is made of a different material than the bearings and housing and expands due to a different coefficient of expansion. In this case, bearings with looser radial clearance may be required.
Standard radial clearance is usually suitable and these bearings are readily available, but sometimes, a non-standard clearance is recommended. If the load is purely radial, tight radial clearance is conducive to low noise, higher rigidity and running accuracy. A looser radial clearance is desirable for high axial loads because it increases the axial load capacity of the bearing. It will also accommodate misalignment between the shaft and housing better.
Tight Radial Clearance (MC1/MC2, PO2/P13, C2): Considered for purely radial loads and low noise, low vibration applications. Beware of axial loads, high speed applications, severe vibration and very low torque applications. An interference fit should not be used.
Medium radial clearance (MC3/MC4, P24/P35, CN): Most commonly used and available as standard, except for full ceramic bearings with C3 as standard.
Loose radial clearance (MC5/MC6, P58/P811, C3/C4): Due to greater thrust load capacity, consider higher axial loads. Greater interference fits and shaft misalignments can be tolerated. Also suitable for heavy loads or shock loads. Not recommended for low noise applications unless tighter radial clearances are not suitable.
Medium radial clearance (MC3/MC4, P24/P35, CN): Most commonly used and available as standard, except for full ceramic bearings with C3 as standard.
Loose radial clearance (MC5/MC6, P58/P811, C3/C4): Due to greater thrust load capacity, consider higher axial loads. Greater interference fits and shaft misalignments can be tolerated. Also suitable for heavy loads or shock loads. Not recommended for low noise applications unless tighter radial clearances are not suitable.
Radial clearance has nothing to do with accuracy class or tolerance. Loose bearing does not necessarily mean low bearing accuracy. You can use P4 (Abec7) class bearings with looser radial clearance, just as you can use P0 (Abec1) bearings with tighter radial clearance, too much clearance indicates the need for tighter radial clearance or Axial preload.
In low noise or high speed applications, zero residual radial play is desirable. This provides greater stiffness, reduces noise, provides greater running precision and eliminates ball slip under acceleration. This is achieved by applying a preload to the bearing. This is the axial load applied to the inner or outer ring to counteract the effect of the outer ring on the inner ring and eliminate radial play.

Preload is usually applied through the use of wave washers or spring washers and is usually applied to a stationary ring which is supposed to have a sliding fit with the shaft or housing to allow axial movement. If the bearing is glued to the shaft or housing, you can use a weight to keep the bearing preloaded while the adhesive cures. The amount of preload should be as small as possible. Excessive preload will result in high frictional torque and rapid failure.
Guide preloads
Preload Category | Preload Amount Miniature & Small Bearing (Cr = Basic Dynamic Load Rating) | Preload Amount Standard Bearing (Cr = Basic Dynamic Load Rating) | Features |
Slight Preload | 0.50% x Cr | 0.15% x Cr | Bearing rigidity not required. Emphasis on low torque. |
Light Preload | 1.25% x Cr | 0.58% x Cr | Bearing rigidity and low torque both required. |
Medium Preload | 1.75% x Cr | 1.28% x Cr | Emphasis on bearing rigidity. Relatively high torque. |
Heavy Preload | 2.50% x Cr | 2.64% x Cr | Emphasis on bearing rigidity. High torque. |
Maximum Ball Bearing Speed
A number of factors affect ball bearing speed limitation such as temperature, load, vibration, radial play, retainer, lubricant, ball material and closures.
The speeds quoted in our technical drawings are only approximate and valid for bearings used on a horizontal shaft with a metal cage, standard tolerance grade and radial play, medium loading, rotating inner ring and suitable lubricant (see below). Vertical shaft applications will require a maximum speed reduction of approximately 20 percent due to reduced cage guidance and less effective lubricant retention.
Excessive temperatures and higher loads will also require slower speeds. Bearings fitted with contact seals cannot achieve the same speed due to increased friction between the seal lip and the bearing inner ring. Lubricant choice can also have a significant impact on rated speed. The maximum speed at which a lubricant can operate effectively varies by type.
The following adjustment factors are approximate and based on bearings with metal crowns or tape cages. If a suitable lubricant is used, the maximum speed of the bearing can be increased by using nylon or phenolic cages. The use of ceramic balls can increase bearing speed by up to 40%, but ceramic balls also reduce the load capacity of the bearing due to the increased stress on the bearing rings caused by the harder ceramic balls.
Speed Reduction Table:
| Rotating Inner Ring | Rotating Outer Ring | ||
---|---|---|---|---|
Open/ZZ | 2RS | Open/ZZ | 2RS | |
Petroleum Oil | Nil Reduction | 40% Reduction | 20% Reduction | 40% Reduction |
Synthetic Oil | Nil Reduction | 40% Reduction | 20% Reduction | 40% Reduction |
Silicon Oil | 30% Reduction | 40% Reduction | 50% Reduction | 50% Reduction |
Standard Grease | 30% Reduction | 40% Reduction | 50% Reduction | 50% Reduction |
High Speed Grease | Nil Reduction | 40% Reduction | 20% Reduction | 40% Reduction |
Silicon Grease | 30% Reduction | 40% Reduction | 50% Reduction | 50% Reduction |
Ball Bearing Frictional Torque
Frictional torque affects the free running of the bearing. Bearings that contain tough grease will have difficulty spinning. This means it has a relatively high frictional moment. A bearing that is not lubricated will spin freely, which means it has low frictional torque. The force required to spin a bearing depends largely on the roundness of the bearing, the applied load, lubrication and closure. The better roundness and surface finish of the balls and raceways means less force is required to spin the bearing. The greater the load, the greater the deformation of the bearing components, resulting in increased resistance.
As for lubrication, gauge oils generally produce lower torque levels, especially at very low speeds, but the difference between these oils and many low torque greases can be very small, especially if low grease fills are used Down. High viscosity lubricants can significantly increase bearing torque due to greater lubricant resistance. Grease bearings experience brief spikes in torque levels as the grease takes a short time to “break in” or distribute inside the bearing. Contact seals will greatly increase torque values. The force required to rotate a bearing from rest (starting torque) is slightly greater than the force required to keep it spinning (running torque).
You can calculate approximate figures for frictional torque using this simple formula:
Radial ball bearings: 0.5 x 0.0015 x radial load in Newtons* x bearing bore (mm)
Axial ball bearings: 0.5 x 0.0013 x axial load in Newtons* x bearing bore (mm)
This is only valid if the bearing has a standard fill of low torque lubrication, does not have contact seals and is subjected to low speed and low load. For radial ball bearings, the axial load should be less than 20 percent of the radial load while the load should be purely axial for thrust bearings. Contact us if you need accurate figures taking into account the speed and the lubricant viscosity.
The measurements are in Newton millimetres (Nmm). This is a compound unit of torque corresponding to the torque from a force of one newton (approx 0.1 Kgf) applied over a distance arm of one millimetre.
Ball Bearing Noise and Vibration
Excessive vibration increases bearing noise and can significantly reduce bearing life. Bearing rings and balls are not perfectly round, and the balls and raceways, even after extensive fine grinding and polishing, are not perfectly smooth. Machining imperfections in the form of rough or uneven surfaces can cause one ring to move or wobble radially relative to the other, causing bearing vibration and noise. The smoothness or quietness of the bearing can be checked with an accelerometer which measures bearing vibrations in the outer ring, usually the inner ring is rotating at 1800 rpm. To understand how to measure bearing vibration, it is important to understand how vibration works.

The amount of oscillation in a vibrating object is called displacement. When a bearing outer ring vibrates, the outer surface will move upwards to the upper limit, then down to the lower limit and then back to the start point. The measurement between upper and lower limit is called peak to peak displacement. The whole oscillation movement from start point through upper and lower limits and back to start point is called a cycle. This vibration cycle will repeat as long as the bearing is rotating. We can also measure the number of these cycles in a given time. This gives us the frequency. Frequency is most commonly expressed as cycles per second (CPS) or Hertz (Hz) which is the same thing.
Vibration can increase the rate of fatigue and shorten bearing life. Displacement measurements do not tell us enough. Vibration in a bearing or a machine will usually occur at many different frequencies and they all contribute to fatigue so we need to take all of these frequencies of vibration into account in our measurements of vibration. We can achieve this by measuring vibration velocity.
Vibration velocity (displacement x frequency) gives us a good indication of the severity of the vibration. If a bearing component is moving a particular distance (displacement) at a particular rate (frequency) it must be moving at a certain speed. The higher the vibration velocity measurement, the noisier the bearing. Vibration velocity is measured on a Bearing Vibration Tester in microns per second or an Anderon Meter in Anderons. One Anderon equals 7.5 microns per second. The readings are separated into three frequency bands: low (50 to 300 Hz); medium (300 to 1800 Hz) and high (1800 to 10000 Hz). Although vibration velocity shows the fatigue potential, vibration force can cause deformation to balls and rings and can be very damaging at high frequencies where velocity readings may be quite low. For this reason we also measure vibration acceleration.
Vibration acceleration is an indication of vibratory force (force = mass x acceleration) and since force is damaging at higher frequencies, vibration acceleration is a useful measurement where a bearing will experience vibration frequencies above 2000 Hz. Vibration acceleration is measured in G (9.81 m/s²) but you will often see these measurements converted to decibels (dB).
A low noise/vibration rating is achieved by paying particular attention to the surface finish of the raceways and balls, the roundness of the rings and balls and correct cage design. Finely filtered low noise greases can also be used. These contain fewer, smaller solid particles which generate noise when they pass between the balls and raceway.
External factors such as surrounding vibration can affect bearing noise. Another problem, particularly with smaller and thin-section bearings, is ring distortion caused by poor shaft or housing roundness. Dirt or dust contamination will also increase noise and vibration levels. Poor fitting practice or incorrect handling is sometimes to blame, causing shock loads which, in turn, create scratches or dents in the raceway.
Ball Bearing Lubricants
Proper lubrication is critical to bearing performance. Lubrication creates a thin film between the contact areas of the bearing to reduce friction, dissipate heat and inhibit corrosion of the balls and raceways. Lubricants affect maximum operating speeds and temperatures, torque levels, noise levels and ultimately bearing life. Mineral or synthetic based lubricants are most commonly used. There are many different types designed for general or high speed use, low noise applications, waterproofing or extreme temperatures.
Silicone lubricants have a wide temperature range and exhibit less change in viscosity with temperature. They are also well water resistant and safe to use with most plastics. They are not suitable for high loads and high speeds.
Perfluorinated or PFPE lubricants are non-flammable, oxygen compatible and highly resistant to many chemicals. They will not react with plastics or elastomers. Many have low vapor pressure and are suitable for vacuum or cleanroom applications, while some can withstand temperatures in excess of 300°C.
Dry Lubricants For use where standard lubricants may cause contamination, such as in vacuum environments. Popular materials such as molybdenum disulfide or tungsten disulfide can be polished or sputtered onto the balls and raceways to provide smooth operation and higher operating speeds than unlubricated bearings.
Solid polymer lubricants consist of a synthetic polymer impregnated with lubricating oil, which fills most of the internal space of the bearing. This type of lubricant is typically used in dusty environments or sealed bearings where lubricant leakage cannot be tolerated, such as clean environments and vertical shaft applications. Solid lubricants have excellent water resistance and can withstand regular washdowns. They can also withstand high vibrations and centrifugal forces.
Dampening greases are widely used in automotive parts to prevents rattles and squeaks. They are also used to give a “quality” feel to switches, slides, threads and gears. They can be used in slow rotating bearings in, for example, potentiometers for the same reason.
Food grade lubricants are required for the food and beverage industries to conform with strict hygiene regulations. HI approved lubricants are required for bearings were there may be incidental contact with food and H2 approved greases are used where there is no contact. These greases are also designed to be highly resistant to being washed out by cleaning processes.
Lubricant Viscosity
Low viscosity oils and greases are used where low lubricant resistance is required such as sensitive instruments. Higher viscosity lubricants may be specified for high load, high speed or vertical shaft applications. Low viscosity oils (or greases with low viscosity base oils) are preferred for high speed applications as they generate less heat. Although greases often provide much greater resistance than oils, many modern low torque greases can produce torque figures that are similar to some oils, particularly where a low grease fill is used.
Oils
Most oils maintain their consistency well over a wide temperature range and are easy to apply. For very low torque applications, a light instrument oil should be specified. Higher running speeds are possible with oil but, as it tends not to stay in place, continuous lubrication must be applied by oil jet, oil bath or oil mist unless speeds are low or rotation is for short periods. An oil-impregnated phenolic retainer or a synthetic retainer made from a material with a very low coefficient of friction such as Torlon do not need continuous external lubrication. These types of retainer are often used in high speed, low torque dental bearings.
Greases
Greases are simply oils mixed with a thickener to so that they stay inside the bearing. Greases are generally suitable for heavy loads and have the obvious advantage of giving constant lubrication over a long period without maintenance.
Surprisingly, too much grease can be bad for a bearing. A high grease fill will mean greater rolling resistance (higher torque) which may not be suitable for many applications but worse still is the risk of heat build-up. The free space inside a bearing is important in allowing the heat to radiate away from contact area between balls and raceway. As a result, too much grease can lead to premature failure unless speeds are low. The standard fill is 25% – 35% of the internal space but this may be varied if required. A smaller percentage may be specified for a high speed, low torque application while a much higher fill may be advisable for a low speed, high load application.
Grease Speed Rating
Greases have speed ratings sometimes called “DN” ratings. The calculation for the “DN” of an application is as follows:
Speed in rpm x (bearing ID + bearing OD) ÷ 2
Assume a bearing rotates at 20,000 rpm. The bearing ID is 8mm and the OD is 22mm. The above formula produces a DN of 300,000 so the grease should be rated above this figure. Many modern greases are suitable for high speeds with some rated at 1 million DN or .
Manufacturers can take several approaches to ensure a long and successful bearing life. The first step is to limit radial loads to between 6% and 12% of the dynamic load rating of the bearing. Although the bearing can withstand higher loads, its life will be shortened.
The next step is to choose the right material. Selecting the correct type of bearing can also play an important role, based on AUB Bearings’ experience as specialists in thin section, corrosion resistant, miniature bearings and ceramic bearings. While all radial ball bearings have some thrust load capability, if greater thrust loads are present, it is usually best to use heavy bearings with deep raceways, as they can withstand up to 50% of the rated static radial load in the axial direction load.
Although thin-section bearings (the difference between the inner and outer diameter of the bearing is small) are very suitable for compactness and weight reduction. Due to the shallow raceways, they can only accommodate axial loads between 10% and 30% of the bearing’s static radial load rating. Additional radial or moment loads will further reduce thrust load capacity. Excessive thrust loads on thin section bearings can cause the balls to come dangerously close to the top of the raceway.
By selecting the appropriate bearing type and considering the key factors governing radial and thrust loads, engineers can ensure that they continue to innovate while delivering the highest levels of precision, smoothness and bearing life.