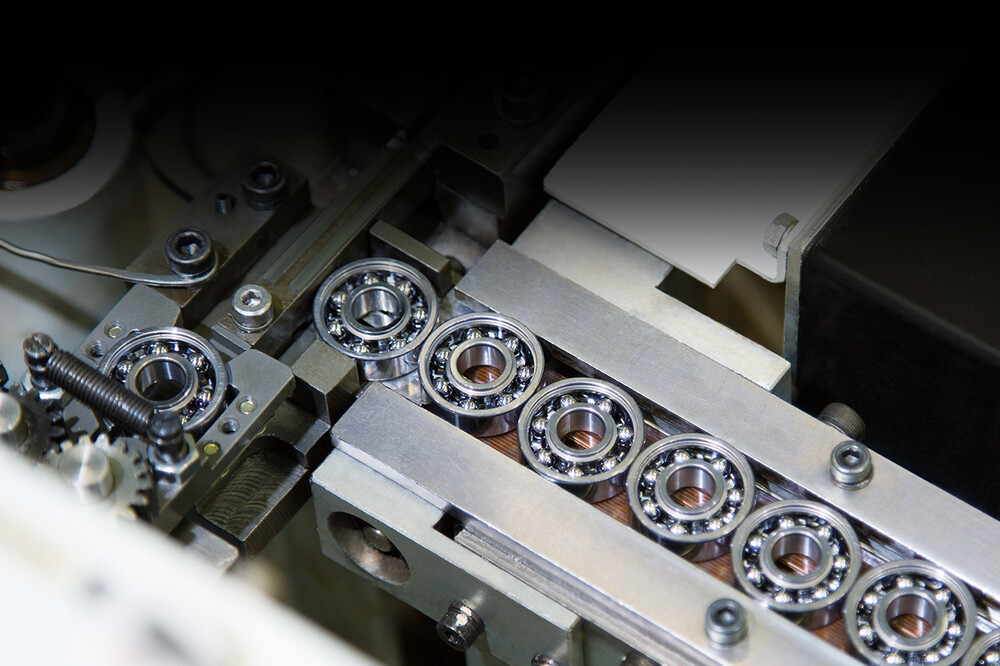
Bearing Manufacturer & Supplier
Specialize in ball bearings, roller bearings, thrust bearings, thin section bearings etc.
Guidelines for Ball Bearing Manufacturing
Ball bearings have played the role of unsung heroes for centuries, facilitating rotational motion and playing an integral role in the smooth operation of machinery in numerous industries. Ball bearings were originally patented by Philip Vaughan in 1794 to support carriage axles, and have since been improved and changed to support a variety of rotating applications. How are ball bearings made? What are ball bearings made of? Let’s take a closer look at the ball bearing manufacturing process, quality control measures. This blog will describe the modern process of ball bearing manufacturing that is widely used today, from the design of the balls to parts assembly and packaging.
Table of Contents
ToggleWhat is a ball bearing
Designed to reduce rotational friction, ball bearings facilitate movement while positioning moving machine parts and carrying radial and bearing loads. Their main purpose is to ensure the smooth operation of rotating parts in machinery. Ball bearings rely on balls to separate two bearing rings or races. This helps minimize surface friction and contact between moving parts. As the balls spin, they cause a lower coefficient of friction compared to flat surfaces rubbing against each other.
Ball bearings vary depending on the mechanism involved, with the most common being radial ball bearings or single row deep groove ball bearings. Spherical ball bearings have minimal contact with their contained races, so they can transfer axial or radial loads with fast, smooth motion. Typical components of ball bearings include:

Inner ring/race: The inner part of the bearing mounted around the axis of rotation. The inner surface of the inner ring, called the raceway, is designed to match the contours of the balls, allowing them to roll smoothly and efficiently.
Outer ring /race: The outer part of a bearing that holds the balls in place. It is usually mounted inside a housing or hole and remains stationary.
The main purpose of a Race is to basically act like a path, allowing frictionless sliding. Simply put, a race is needed to control the respective balls, and it provides a fixed path for the balls to roll. There are two types of races in bearings. Inner ring, outer ring and a set of balls. Both seats contain a grooved ring in their seat that retains a steel ball. Apparently, the steel ball will come into direct contact with each race at one point. The inner ring is located on the inside of the ball, on the other hand, the outer ring is located on the outside of the ball. An inner ball is sandwiched between these two types of races. The two races also rotate in opposite directions to maintain their rotation.

Balls: Steel balls are spherical components used as rolling mechanisms in rotating parts such as bearings, tools, and wheels. There are many specifications and sizes for various applications. Balls play the most crucial role in performing functions. The most important purpose is that it represents the importance of the rolling and rotational aspects of the bearing. Without it, the bearing may not rotate in any direction. Spherical rolling elements that allow smooth rotation and carry the load between the inner and outer rings. They are made of extremely hard and durable materials such as chrome steel, ceramic or stainless steel.
Cage or retainer: A component that separates and maintains the spacing between the balls, rollers, or needle rollers, keeping them at a symmetrical radial spacing, and holding the bearings together. The cage holds the balls in uniform rings so that they are equally spaced within the bearing. It can be manufactured into a variety of shapes and developed using low-friction materials, allowing the ball to continue rolling efficiently. It ensures that the balls do not come into contact with each other during operation, thus reducing friction and wear. The materials of the bearing cage include: steel bearing cage, ceramic bearing cage, high-strength polymer (nylon, POM, etc.), etc.
Shields or seals: These are protective caps that are typically mounted on the outer ring of the bearing and provide a barrier to prevent contaminants from entering the bearing, thereby extending its service life.
Bearings are vital to manufacturing and are used in many different types of equipment and machinery. From basic industrial equipment to complex machinery, bearings reduce friction and enable them to handle different types of loads. Therefore, the use of high-quality and reliable materials is crucial to the bearing manufacturing process. Different materials are used to manufacture various types of high-quality bearings and their many components. These materials undergo specific processes to obtain the required properties, thereby increasing the bearing life and performance. Aubearing’s team can discuss the different materials used in bearing manufacturing and how each affects the use, integrity and functionality of the bearing.

Most ball bearings are made from a type of steel called high carbon chromium steel, often referred to as chromium steel. This is used for cost and durability reasons. Bearings are also made from other materials, such as stainless steel, ceramics and plastics. However, each of its features is adapted to a different purpose.
Chrome Steel (GCr15 & 52100)
Chromium steel (GCr15 &SAE 52100) is the most commonly used material for manufacturing precision ball bearings, roller bearings and tapered roller bearings. Specifically, it is used to manufacture the load-bearing components of bearings, such as inner rings, outer rings, balls and rollers. Chrome steel is an efficient and economical bearing material because of its durability and strength in harsh conditions. Although chromium steel is less resistant to corrosion, it is durable and can still resist some degree of corrosion in certain environments. SAE 52100 is a chromium steel containing 1% carbon and 1.5% chromium alloy. This material remains stable at temperatures in excess of 250 degrees Fahrenheit and provides reliable bearings and long service life. Chromium steel undergoes controlled machining and heat treatment methods to make the bearings strong and crack-resistant. These processes give the bearings and their components a surface hardness of 60 to 64 on the Rockwell scale C, which makes them resistant to subsurface rolling contact fatigue. Chromium steel is a good general purpose bearing steel due to its excellent hardness and wear resistance. However, due to its lower chromium content, it has poor corrosion resistance compared to other materials. It is recommended that users protect chromium steel bearings with a coating of oil or rust inhibitor to prevent corrosion.

In addition to containing at least 18% chromium, stainless steel also contains nickel. When the chromium in stainless steel comes into contact with oxygen, a chemical reaction occurs, forming a layer of chromium oxide on the surface of the bearing component. This passivating chemical film provides additional protection to the bearings. There are two common types of stainless steel bearings: martensitic and austenitic.
Stainless steel bearings offer several significant advantages, as stainless steel in particular has greater resistance to chemicals and corrosion, as well as better stability in high-temperature environments. It features the same deep grooves and tight fit between raceways and balls as standard made from chrome steel. Therefore, bearings are often made from grade 440 stainless steel where corrosion resistance is required. Grade 440 stainless steel is a very hard steel that has good corrosion resistance, but is not suitable for use with salt water and many chemicals.

Martensitic stainless steel bearings (SV30) are often modified during the processing of raw steel, resulting in a reduction in carbon content and an increase in nitrogen content in the material. The result is steel with high strength, hardness and enhanced corrosion resistance. Austenitic stainless steel bearings (AISI316), on the other hand, are non-magnetic and highly resistant to corrosion due to their low carbon content. Likewise, grade 316 stainless steel is used in corrosive applications. However, due to their carbon content, stainless steel bearings are less hard and their load carrying capacity is 20% lower than 52100 chromium steel bearings. 316 stainless steel is therefore softer and therefore can only be used at lower loads and speeds.
Ceramics (zirconia and silicon nitride) are suitable for highly corrosive or extreme temperature applications. Ceramic materials are also used in the manufacture of bearings and bearing components. However, these materials are often classified as niche areas of the bearing industry. The most common ceramic material is silicon nitride. Bearing balls made of silicon nitride are known for their excellent surface hardness, up to 78 on the Rockwell C scale, and their extremely smooth surfaces. However, there is a problem with using ceramic materials in bearing construction. Bearings made of ceramic materials are generally expensive than bearings made of pure stainless steel.

Completely ceramic ball bearings are made of ceramic materials. The inner ring, outer ring and balls are made of silicon nitride (Si3N4) or zirconium oxide (ZrO2). The main features are its higher hardness and better elasticity compared to chromium steel bearings. In addition, it can run completely dry, has excellent corrosion resistance, can run in concentrated acid, and will not corrode when completely immersed in seawater, and is suitable for temperature changes and lasts much longer than steel bearings. Ceramics are often used when hybrid bearings are made, where the steel rings are made of stainless steel and the balls are made of ceramic.
Carbon alloy steel
Carbon alloy steel is commonly used in the production of “semi-precision” or “commercial grade” bearings and bearing components. Aubearing offers carbon alloy steel bearings with accuracy grades ABEC #1-5 or higher. Typically, low carbon alloys are used to make bearing cages, metal guards, and metal washers. They are less resistant to corrosion than other bearing materials, so they must be coated with a layer of oil or grease to prevent corrosion. Electroplating can also be used to prevent oxidation.
Other non-metallic materials
Since bearings are often installed in machines that carry or handle loads, a common misconception is that bearings can only be made of metal. However, non-metallic materials can also be used to produce bearings and their components. Various types of plastics are suitable for good to very good corrosion resistance, but only for low loads and low speeds. Some examples of the types of non-metallic materials that can be used in bearing construction include, but are not limited to:

A. Plastic
Plastic is sometimes used to make bearing cages to reduce production costs, but this material is not always suitable for harsh conditions, especially high-temperature applications. The most common type of plastic is nylon plastic, but molded acetal or POM can also be used as alternatives. Other polymers are used in special bearing designs with specific performance requirements such as high speed, low torque, or low noise.
For example, high-speed ball bearings used in machine tool spindles have cages made of phenolic (phenol-formaldehyde) material. Although the phenolic cage and bearing components are lightweight, they are strong and durable.
B. Rubber
Rubber is also used in the manufacture of bearings, especially their seals. Nitrile or Buna rubber is often used due to its good mechanical properties. Rubber is generally inexpensive, can withstand many different temperature ranges, and is resistant to many chemicals. Meanwhile, materials such as elastomers or rubbers, such as fluoroelastomers and silicones, are often used when applications require their unique properties.
Obviously, there are a variety of materials that can be used in the construction of bearings, and each material can be used for different purposes and achieve different desired properties. Therefore, the importance of the material from which a particular bearing is made cannot be underestimated.
Ball bearing manufacturing process
How are ball bearings made? How do they make the balls so round? The answer is a multi-step manufacturing process that includes machining, heat treatment, grinding, honing, grinding and assembly. Although there may be differences, the following procedure applies to the vast majority of standard ball bearings produced today.
Material selection: high-quality steel, such as high-carbon chromium steel. Depending on the application requirements of the bearing, some plastics, ceramics, stainless steel, and other materials may even be used. Due to its high strength and wear resistance, it is the most commonly used material for manufacturing ball bearings.
Forged or cast: The selected material is forged or cast into the shape of the bearing component. Forging involves heating and shaping steel, adjusting its grain structure to improve durability. Alternatively, casting, less common but used for larger or complex parts, involves molding molten metal into the desired shape.

Heat Treatment: Forged or cast parts are heat treated to increase their hardness and durability. Parts are heated to a high temperature, then cooled quickly in a process called quenching, and then tempered, in which the part is reheated to a lower temperature and then cooled slowly. The process strikes a balance between wear-resistant hardness and toughness to resist impact loads.
Machining, Grinding & Super Fine Grinding: The heat-treated parts are then machined and ground with high precision to final dimensions. The machining process can include turning, milling and drilling, all performed using computer-controlled machines to ensure accuracy. Ultra-fine grinding to achieve correct sphericity and surface finish, ensuring smooth and efficient operation.
Assembly and lubrication: Finally, the inner ring, outer ring, ball and cage are assembled into the bearing, and lubricant is applied to reduce friction and wear between the moving parts and ensure the smooth and efficient operation of the bearing. The type of bearing lubricant (oil or grease) depends on the application.
The manufacturing process of ball bearings involves complex procedures to ensure that the final product is smooth and perfectly round.
Manufacturing of inner and outer rings of bearings
The manufacturing process for inner and outer raceways is very similar. They begin as steel tubes that are cut by automated machines into the basic shape of the raceways, leaving a small amount of extra material to account for warping during the heating process. Afterwards, the necessary manufacturing information and bearing number are printed on the outer ring surface. Visit our bearing numbering system to learn about bearing numbering. Then comes the reinforcement phase.
The rings are hardened in a heat-treating furnace and heated to about 1550 degrees Fahrenheit (840 degrees Celsius) for anywhere from 20 minutes to several hours, depending on the size of the part. The ring is then quenched in oil at 375° F for 15 to 20 minutes. The next step is to temper the ring at 340°F for about two hours. And temper in a second oven at around 300 degrees Fahrenheit (148 degrees Celsius). This process makes the raceway both strong and durable.

The raceways are finished using grinding wheels as it is now difficult to cut the raceways to the required size with cutting tools. Every part of the ring must be ground to ensure correct bearing width, radius, race position and geometry. Some bearings, such as angular contact bearings, require additional grinding during this process to ensure the rings are the correct size. Raceway grinding helps achieve raceway position, geometry and radius. End grinding ensures the ring has the proper bearing width. Then the inner hole is ground on the inner ring, and the outer ring is ground at the same time. Finally, the seat undergoes a honing process to achieve a perfect surface finish and geometry.
Balls for manufacturing ball bearings
Bearing balls undergo a very specific and thorough manufacturing process, resulting in perfectly round and smooth balls that minimize friction within the bearing. These balls begin as wire or rods that contain the necessary materials needed to form the finished ball. This wire undergoes a process called “cold heading.” During this process, the wire ends hit each other, forming a ball with a small ring around it.
The ball is then rolled to remove any rough edges. In this process, the ball is repeatedly fed into a groove between two cast iron discs, one of which is rotating and the other is stationary. The rough grooves effectively remove burrs and make the ball fairly round and slightly oversized for easier grinding. Next, the ball undergoes a heat treatment process similar to the raceway to improve durability before being ground to the proper size and roundness.

Finally, the ball is moved to a grinder, where a soft cast iron disc is used to polish the ball, similar to the tumble grinding process but with less pressure. Polishing paste is used to make the surface completely smooth without further removal of material. The balls remain in the grinder for 8-10 hours to produce perfectly smooth balls.
Manufacture of cages for ball bearings
The cage is part of the bearing and is made from a variety of materials, including stamped steel, stamped brass, machined steel, machined bronze, molded nylon or acetal (POM), and phenolic resin. For steel or metal cages, the outline of the cage is stamped out of a thin sheet of metal and then placed into a die-like structure called a “die” that bends the cage into the appropriate shape. The cage can then be removed and ready for assembly. For plastic cages, a process called “injection molding” is used, where molten plastic is injected into a mold and allowed to harden.

Assembling ball bearings
After all the bearing parts are assembled, the bearing can be assembled. First, place the inner ring inside the outer ring. The balls are then inserted between the raceways and evenly spaced. Finally, install the cage to hold the ball in place. Plastic cages snap in easily, while steel cages usually need to be riveted together. The bearings are then coated with rust inhibitor or other special surface treatment for the specific application and packaged for shipping.

Ball bearings undergo rigorous testing and quality control procedures to ensure their reliability and durability. Common inspection and measurement techniques include:
Visual inspection: Check the bearings for any visible defects such as cracks, wear or surface irregularities.
Dimensional measurement: Use special bearing testing instruments to measure key dimensions of bearings, such as inner diameter, outer diameter, ball size and width.
Roundness and run-out measurement: Assess the roundness of bearing components and measure any run-out or deviation from the ideal circular shape.
Surface roughness analysis: Use instruments such as profilometers to evaluate the smoothness or roughness of bearing surfaces to ensure proper operation and reduce friction.
Hardness testing: Determine the hardness of bearing components using methods such as Rockwell or Vickers hardness testing to ensure they meet required specifications.

Noise and vibration analysis: Specialized equipment is used to detect and analyze noise and vibration levels during bearing operation, which can indicate potential problems or anomalies.
Bearing Lubrication Analysis: Evaluates lubricant condition and characteristics such as viscosity, cleanliness and contamination levels to ensure optimal lubrication and extend bearing life.
Non-destructive testing (NDT): Using techniques such as ultrasonic testing or magnetic particle testing to detect internal defects or cracks without damaging the bearings.
Durability and performance testing: Bearings are subjected to simulated operating conditions such as bearing loads, speeds and temperatures to evaluate their durability, fatigue resistance and overall performance.
Statistical process control
Statistical process control (SPC) is a quality control method used in ball bearing manufacturing. It uses statistical analysis to monitor the production process and identify any potential problems before the product is completed. SPC involves monitoring the manufacturing process for signs of change and deviations from expected production parameters. This allows manufacturers to identify and resolve any potential issues with the product before it reaches the customer.Additionally, SPC can be used to optimize production processes and reduce production costs to maintain high quality standards. By leveraging SPC, ball bearing manufacturers can continually improve their processes and products to better serve their customers.
Conclusion
At Aubearing, we specialize in manufacturing ball bearings to suit a variety of shapes, materials and size requirements. You can choose from our steel, stainless steel or chrome steel, ceramic ball bearings. Our ball bearings are used in appliances such as pumps, office automation products, medical equipment, power tools, encoders, AC/DC motors, flow meters and measuring equipment.