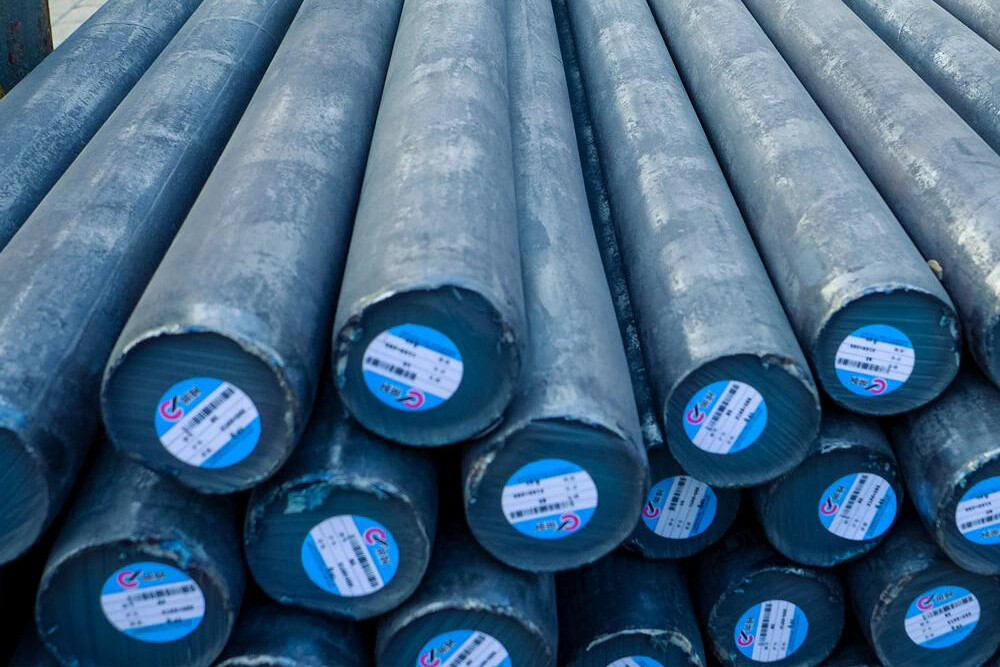
Bearing Manufacturer & Supplier
Specialize in ball bearings, roller bearings, thrust bearings, thin section bearings etc.
Basic Performance Requirements of Bearing Steel
Bearing materials include inner rings, outer rings, rolling elements and cages, rivets and other auxiliary materials. The vast majority of bearings and their parts are made of bearing steel. With the development of modern science and technology and the increasing use of rolling bearings, the requirements for bearings are getting higher and higher, such as high precision, long life and high reliability. For some special-purpose bearings, bearing materials are also required to have properties such as high temperature resistance, corrosion resistance, non-magnetic, ultra-low temperature, and radiation resistance. In addition, bearing materials also include alloy materials, non-ferrous metals and non-metallic materials. In addition, bearings made of ceramic materials are now used in locomotives, automobiles, subways, aviation, aerospace, chemical industry and other fields.
Table of Contents
ToggleWhat is bearing steel?
Bearing steel is also called high carbon chromium steel, with a carbon content Wc of about 1% and a chromium content Wcr of 0.5%-1.65%. Bearing steel is divided into six categories: high carbon chromium bearing steel, chromium-free bearing steel, carburized bearing steel, stainless bearing steel, medium and high temperature bearing steel and antimagnetic bearing steel.
High carbon chromium bearing steel GCr15 is the most produced bearing steel in the world. The carbon content Wc is about 1%, and the chromium content Wcr is about 1.5%. Over the past 100 years since its birth in 1901, the main components have basically not changed. With the advancement of science and technology, research work continues and product quality continues to improve, accounting for than 80% of the world’s total bearing steel production. So if there is no special instructions for bearing steel, it refers to GCr15 (AISI 52100).

Basic properties of bearing steel
The basic material requirements of bearings depend to a large extent on the working performance of the bearings. Whether the material used to manufacture rolling bearings is suitable will have a great impact on its performance and life. In general, the main damage forms of rolling bearings are fatigue spalling under stress and damage to bearing accuracy due to friction and wear. In addition, there are cracks, indentations, rust and other reasons that cause abnormal damage to the bearings. Therefore, rolling bearings should have high resistance to plastic deformation, low friction and wear, good rotation accuracy, good dimensional accuracy and stability, and long contact fatigue life. And many of these properties are determined by the material and heat treatment process. Since the basic requirements for materials for rolling bearings are determined by the damage mode of the bearing, the materials for manufacturing rolling bearings are required to have the following properties after a certain heat treatment in the post-process:
High contact fatigue strength
Contact fatigue damage is the main form of normal bearing damage. When a rolling bearing is running, the rolling elements roll between the raceways of the inner and outer rings of the bearing. The contact parts are subjected to periodic alternating loads, which can reach hundreds of thousands of times per minute. Under the repeated action of periodic alternating stress, the contact surface Fatigue peeling occurs. Once the rolling bearing begins to peel off, it will cause the bearing to vibrate, increase noise, and the operating temperature to rise sharply, causing the bearing to eventually be damaged. This form of damage is called contact fatigue damage. Therefore, the steel for rolling bearings is required to have high contact fatigue strength.
High wear resistance
When rolling bearings work normally, in addition to rolling friction, there is also sliding friction. The main parts where sliding friction occurs are: the contact surface between the rolling element and the raceway, the contact surface between the rolling element and the cage pocket, the cage and the ferrule guide rib, and the roller end surface and the ferrule guide. Wait between the sides. The existence of sliding friction in rolling bearings inevitably causes wear of bearing parts. If the wear resistance of the bearing steel is poor, the rolling bearing will lose precision prematurely due to wear or the rotation accuracy will decrease, resulting in increased vibration and reduced service life of the bearing. Therefore, bearing steel is required to have high wear resistance.
High elastic limit
When the rolling bearing is working, since the contact area between the rolling element and the ring raceway is very small, when the bearing is bearing load, especially when bearing a large load, the contact pressure on the contact surface is very large. In order to prevent excessive plastic deformation from occurring under high contact stress, resulting in loss of bearing accuracy or occurrence of surface cracks, the bearing steel is required to have a high elastic limit.
Four appropriate hardness
Suitable hardness
Hardness is one of the important indicators of rolling bearings. It is closely related to the material contact fatigue strength, wear resistance, and elastic limit, and directly affects the life of the rolling bearing. The hardness of the bearing is usually determined based on the way and size of the load the bearing bears, the overall size of the bearing, and the wall thickness. The hardness of the steel used for rolling bearings must be appropriate. If it is too large or too small, it will affect the service life of the bearing. As we all know, the main failure forms of rolling bearings are contact fatigue damage, and loss of bearing accuracy due to poor wear resistance or dimensional instability; if the bearing parts lack a certain toughness, they will suffer from brittle fracture when subjected to large impact loads. Bearing damage. Therefore, the hardness of the bearing must be determined based on the specific conditions of the bearing and the mode of damage. For bearing accuracy loss due to fatigue spalling or poor wear resistance, bearing parts should be selected with higher hardness; for bearings that bear larger impact loads (such as rolling mill bearings, railway bearings and some automobile bearings, etc.), the hardness should be appropriately reduced. Hardness is necessary to improve the toughness of the bearing.
Good impact toughness
Many rolling bearings will be subject to certain impact loads during use, so the bearing steel is required to have a certain degree of toughness to ensure that the bearings are not damaged by impact. For bearings that bear large impact loads, such as rolling mill bearings and railway bearings, materials are required to have relatively high impact toughness and fracture toughness. Some of these bearings use bainite quenching heat treatment process, and some use carburizing steel materials, just to These bearings are guaranteed to have good impact resistance toughness.
Good dimensional stability
Rolling bearings are precision mechanical parts, and their accuracy is measured in microns. During long-term storage and use, changes in the internal structure or stress will cause changes in the bearing size, causing the bearing to lose accuracy. Therefore, in order to ensure the dimensional accuracy of the bearing, the bearing steel should have good dimensional stability.
Good anti-rust performance
Rolling bearings have many production processes and a long production cycle. Some semi-finished products or finished parts need to be stored for a long time before assembly. Therefore, bearing parts are prone to certain corrosion during the production process or during the storage of finished products, especially It’s in humid air. Therefore, bearing steel is required to have good anti-rust properties.
Good process performance
During the production process of rolling bearings, their parts undergo multiple cold and hot processing processes. This requires that bearing steel should have good process properties, such as cold and hot forming properties, cutting and grinding properties, heat treatment properties, etc., to meet the needs of large-volume, high-efficiency, low-cost and high-quality production of rolling bearings.
In addition, for bearings used under special working conditions, in addition to the above basic requirements, corresponding special performance requirements must be put forward for the steel used, such as high temperature resistance, high speed performance, corrosion resistance and antimagnetic properties.
Bearing steel heat treatment process
The bearing steel heat treatment process consists of two main links: pre-heat treatment and final heat treatment. GCr15 steel is the most widely used type of bearing steel. It is a high-carbon chromium bearing steel with low alloy content and good performance. GCr15 bearing steel has high and uniform hardness, good wear resistance, and high contact fatigue performance after heat treatment.
Annealing
(1) Complete annealing and isothermal annealing: Complete annealing is also called recrystallization annealing, generally referred to as annealing. This annealing is mainly used for castings, forgings and hot-rolled profiles of various carbon steels and alloy steels with hypoeutectoid composition, and sometimes Also used in welded structures. It is generally used as the final heat treatment of some unimportant workpieces, or as the pre-heat treatment of some workpieces.
(2) Spheroidizing annealing: Spheroidizing annealing is mainly used for hypereutectoid carbon steel and alloy tool steel (such as steel types used in manufacturing cutting tools, measuring tools, and molds). Its main purpose is to reduce hardness, improve machinability, and prepare for subsequent quenching.

(3) Stress relief annealing: Stress relief annealing is also called low-temperature annealing (or high-temperature tempering). This kind of annealing is mainly used to eliminate residual stress in castings, forgings, welding parts, hot-rolled parts, cold-drawn parts, etc. If these stresses are not eliminated, it will cause the steel parts to deform or crack after a certain period of time or during subsequent cutting processes.
Quenching
In order to improve the hardness, the main methods are heating, heat preservation and rapid cooling. The most commonly used cooling media are brine, water and oil. The workpiece quenched in salt water is easy to obtain high hardness and smooth surface, and is not prone to soft spots that are not quenched, but it is easy to cause serious deformation of the workpiece and even cracking. The use of oil as the quenching medium is only suitable for quenching some alloy steels or small-sized carbon steel workpieces where the stability of supercooled austenite is relatively large.

Tempering
(1) Reduce brittleness and eliminate or reduce internal stress. After quenching, steel parts will have great internal stress and brittleness. If they are not tempered in time, the steel parts will often deform or even crack.
(2) Obtain the mechanical properties required by the workpiece. After quenching, the workpiece has high hardness and high brittleness. In order to meet the different performance requirements of various workpieces, the hardness can be adjusted through appropriate tempering to reduce the brittleness and obtain the required Toughness, plasticity.
(3) Stable workpiece size
(4) For some alloy steels that are difficult to soften by annealing, high-temperature tempering is often used after quenching (or normalizing) to properly gather carbides in the steel and reduce the hardness to facilitate cutting.

Basic quality requirements for bearing steel
Strict chemical composition requirements.
General bearing steel is mainly high-carbon chromium bearing steel, which is hypereutectoid steel with a carbon content of about 1%, adding about 1.5% chromium, and a small amount of manganese and silicon elements. Chromium can improve heat treatment performance, improve hardenability, structural uniformity, tempering stability, and improve the anti-rust performance and grinding performance of steel.
But when the chromium content exceeds 1.65%, the retained austenite in the steel will increase after quenching, reducing the hardness and dimensional stability, increasing the inhomogeneity of carbides, and reducing the impact toughness and fatigue strength of the steel. For this reason, the chromium content in high-carbon chromium bearing steel is generally controlled below 1.65%. Only by strictly controlling the chemical composition of bearing steel can the structure and hardness that meets the bearing performance be obtained through the heat treatment process.
Higher dimensional accuracy requirements.
For hot-rolled annealed bars forged on high-speed heading machines, there should be higher requirements for dimensional accuracy. Steel for rolling bearings requires high dimensional accuracy because most bearing parts must be pressure formed. In order to save materials and improve labor productivity, most bearing rings are forged and formed, steel balls are formed by cold heading or hot rolling, and small-sized rollers are also formed by cold heading. If the dimensional accuracy of the steel is not high, the cutting size and weight cannot be accurately calculated, and the product quality of the bearing parts cannot be guaranteed, and it is easy to cause damage to equipment and molds.
Specially strict purity requirements.
The purity of steel refers to the number of non-metallic inclusions contained in the steel. The higher the purity, the fewer non-metallic inclusions in the steel. Harmful inclusions such as oxides and silicates in bearing steel are the main reasons for early fatigue spalling of bearings and significantly reducing bearing life. In particular, brittle inclusions are the most harmful because they are easy to peel off from the metal matrix during processing, seriously affecting the surface quality of bearing parts after finishing. Therefore, in order to improve the service life and reliability of bearings, the content of inclusions in bearing steel must be reduced.
Strict low-magnification tissue and microscopic (high-magnification) tissue requirements.
The low-magnification structure of bearing steel refers to general porosity, central porosity and segregation. The microscopic (high-magnification) structure includes the annealed structure of steel, carbide network, banding and liquid segregation, etc. Carbide liquid is hard and brittle, and its hazards are the same as brittle inclusions. Reticular carbides reduce the impact toughness of steel and make it uneven in structure, making it easy to deform and crack during quenching. Banded carbides affect annealing and quenching and tempering structures as well as contact fatigue strength. The quality of low and high magnification structures has a great impact on the performance and service life of rolling bearings. Therefore, there are strict requirements for low and high magnification structures in bearing material standards.
Surface defects and internal defects are prohibited
For bearing steel, surface defects include cracks, slag inclusions, burrs, scabs, oxide scales, etc., and internal defects include shrinkage holes, bubbles, white spots, severe porosity and segregation, etc. These defects have a great impact on bearing processing, bearing performance and life. It is clearly stipulated in the bearing material standards that these defects are not allowed.
Prohibition of uneven carbides
In bearing steel, if there is severe uneven distribution of carbides, it will easily cause uneven structure and hardness during heat treatment. The uneven structure of steel has a greater impact on the contact fatigue strength. In addition, severe carbide unevenness can easily cause cracks in bearing parts during quenching and cooling, and carbide unevenness can also reduce the life of the bearing. Therefore, in the bearing material standards, there are clear regulations for different specifications of steel. special requirement.
Strict surface decarburization layer depth requirements.
There are strict regulations on the surface decarburization layer of steel in the bearing material standards. If the surface decarburization layer exceeds the scope of the standard and is not completely removed during the processing before heat treatment, it will be removed during the heat treatment and quenching process. It is easy to produce quenching cracks, causing parts to be scrapped.
Other requirements.
In the bearing steel material standards, there are also strict requirements for the smelting method, oxygen content, annealing hardness, fracture surface, residual elements, spark inspection, delivery status, marking, etc. of the bearing steel.