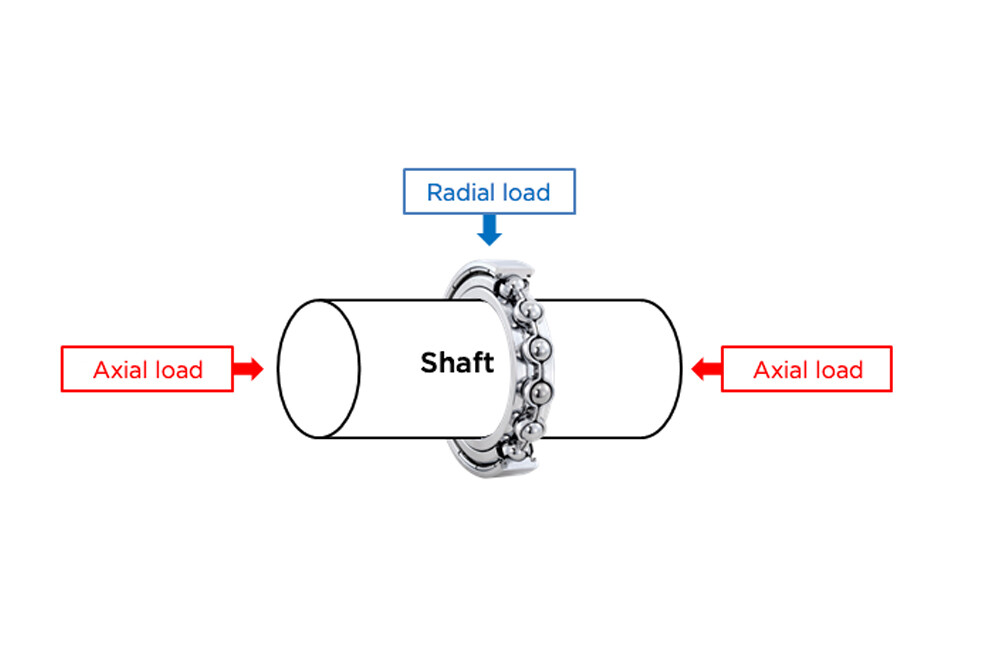
Bearing Manufacturer & Supplier
Specialize in ball bearings, roller bearings, thrust bearings, thin section bearings etc.
Guidance on Bearing Loads
Bearing load is closely related to the service life and working performance of the bearing. Understanding bearing loads is critical when you are designing new applications, adapting existing ones, and especially when analyzing the causes of bearing failure and failure. If a bearing is selected with insufficient load capacity it can lead to premature wear, overheating and catastrophic consequences.
Table of Contents
ToggleWhat is bearing load?
Simply put, bearing load is the amount of force or pressure exerted on the bearing. Bearing load is defined as the force transmitted from one bearing ring to another through some or all of the rolling elements. Applied loads are typically transferred to the shaft, then to the inner ring of the bearing, and finally to the outer ring of the bearing. The magnitude and direction of bearing loads depend on a variety of factors, including machine weight, operating speed, acceleration, deceleration, shock, vibration, temperature and lubrication. Improper alignment, installation or maintenance can also affect bearing loads. Bearing loads support many different combinations, but most types of applied loads can be boiled down to the following four main types:
Radial load
Axis load
Preloaded
Centrifugal load

This article will discuss these four types of applied loads, how it affects bearing life, and selecting which bearing can best support the appropriate applied load.
Bearing radial load
Bearing radial load is the force acting on the bearing outer ring perpendicular to the axis of the shaft. Typical examples of radial loads on bearings are the weight of horizontal shaft assemblies, gears, pulleys, or cutting tools. When working, the shaft assembly radially pushes the inner ring of the bearing and transmits the load to the outer ring of the bearing through the rolling elements. Radial loads generally do not transmit forces to the rolling elements in an equal and uniform manner. That’s why when you look at a load, you see a force distribution shaped like a bell curve. The rolling element that is directly subjected to the applied load is the one that withstands the greatest forces. Each successive rolling element then transfers smaller and smaller loads in one direction to the other. To calculate the radial load capacity of a bearing, it is necessary to determine the weight being supported and the forces acting on it. To distribute the load between bearings, ensure that the calculated loads are within the maximum load capacity of the bearing selected according to the manufacturer’s specifications. If the application imposes radial loads on the bearings, radial ball bearings or angular contact bearings would be a good option.

Bearing axial load
Bearing axial load is a force parallel to the axis of the shaft, acting on the inner or outer ring of the bearing, sometimes called a thrust load. Typically you will find axial loads directly aligned with the shaft, just like a drill bit. Axial loads are caused by thrust or tension and can be unidirectional or bidirectional. Other times, axial loads can be reaction loads that are offset from the shaft axis, as in the case of bevel gears. Axial loads transfer forces to the rolling elements in an equal and uniform manner, resulting in a balanced load distribution. Typically you will see the force on each ball being evenly distributed. Because the ball contacts the raceway at an angle, the resultant force will radiate outward and in line with the bearing axis. If your application imposes axial loads on the bearing, an angular contact bearing with a higher contact angle (approximately 25°) would be a good option. However, with offset axial loads, moment forces are exerted on the inner ring, resulting in uneven load distribution on the rolling elements of the bearing. To calculate axial load capacity, consider bearing size, material and geometry, as well as load direction and magnitude. Manufacturers rate bearings based on standardized formulas and tests. Applications with high axial loads include pumps, automotive transmissions and compressors.

Bearing preload
Bearing preload is a special type of bearing axial load (or thrust load). Bearing preload is the predetermined load applied to the bearing and should be separated from the applied load. Adding bearing preload creates optimal synergy between rolling elements and bearing races. The role of bearing preload force:
Prevent excessive slipping
Increase rigidity, reduce vibration and sliding friction
High operating accuracy – even with changing load conditions
Increase load capacity
In general, if you are designing a high-speed application, consider using light preload on angular contact bearings. Aubearing recommends our SM angular contact bearings or KH angular contact bearings. On the other hand, if you are designing an application that requires strict rigidity and accuracy, then you may want to consider applying medium or heavy preload to the angular contact bearing. Aubearing recommends our S angular contact bearing series.
Bearing centrifugal load
Bearing centrifugal loads arise from the rotational speed (RPM) of the application, particularly high-speed applications such as turbines and centrifuges. High-speed applications create strong centrifugal loads, which are one of the factors that affect the application’s ability to reach its maximum speed. As the inner ring rolling elements rotate, they want to move tangentially along a straight path, but the outer ring must force them to follow the arc of the bearing. This interaction creates centrifugal radial loads. Centrifugal force is the force that an object moving along a curved path feels outward away from the center of rotation. During bearing rotation, the interaction between the rolling elements and the outer ring generates centrifugal radial loads, as follows:
The inner ring rotates the rolling elements
A rolling element that follows motion wishes to continue moving straight along a path tangent to the arc of rotation
The outer ring must force the rolling elements to continue moving along the arc of the bearing
Centrifugal loading is very important in selecting appropriate bearings as it affects bearing life. If the application requires high speed, consider using an angular contact bearing with smaller balls, such as Aubearing’s KH series. Another option is to switch from bearing steel balls to ceramic balls. Smaller and/or lighter balls reduce the rotating mass and thus the applied centrifugal load.
Extra: Hertzian Contact Pressure
As stated above, all the loads we discussed arise from contact forces that are transmitted from one bearing ring to another through the rolling elements. But what we didn’t mention is that this contact force creates pressure where the rolling elements push against the raceway; this is called Hertzian contact pressure or Hertzian stress. Hertzian contact pressure is an important reference factor in determining the amount and type of load a bearing can withstand. The ability of a bearing to withstand a load depends on how close the Hertzian contact pressure is to the bearing stress limit. The closer the bearing is to its stress limit, the shorter the time required for the bearing to undergo plastic deformation.
For example, for steel AISI 52100 ball bearings, the generally accepted stress limit is 4,200 MPa. Aubearing believes that the Hertzian contact pressure of steel balls is higher than 1,500 MPa and that of ceramic balls is higher than 1,800 MPa, which is enough to approach the stress limit and thus have a significant impact on the overall life of the application. If the application has high hertz stress, changes to the application may be required to reduce the stress. Some solutions could be changing bearing sizes, using ceramic balls, or adding bearings to the system to help distribute the load.

Calculate bearing loads
Bearing load capacity can be calculated using a variety of formulas and software programs, including those of the bearing manufacturer. Table of contents, online calculators, and finite element analysis (FEA) simulations. The most commonly used radial and axial load formulas are:
Radial load capacity = (C/P)^(1/3) x Fr
Axial load capacity = (C0/P)^(1/2) x Fa
In the formula, C is the basic dynamic load rating, P is the equivalent dynamic load of the bearing, C0 is the basic static load rating, Fr is the radial load, and Fa is the axial load. To obtain accurate results when calculating bearing load capacity, seek expert advice or use a software program provided by the bearing manufacturer.
Selecting bearings with sufficient centrifugal load capacity is critical for high-speed applications to prevent premature failure. Centrifugal loads can cause bearing deformation, vibration and fatigue. To calculate centrifugal load capacity, use formulas and software programs such as those provided by the manufacturer. Table of contents, online calculators and FEA simulations. The most common formula is: centrifugal load capacity = (C0/P) x V^2 x 10^-9. where C0 is the basic static load rating, P is the equivalent dynamic bearing load, and V is the bearing speed in rpm.
Rated bearing load
We always express the load rating of a bearing in Kgf (kilogram force). This is the force exerted by a kilogram of mass on the Earth’s surface. Elsewhere, you may see forces expressed in Newtons. Newton is defined as the force that accelerates a kilogram of mass at one meter per second (or 1 m/s²). Since the gravity at the Earth’s surface is 9.80665 m/s², 1 Kgf = 9.80665 Newtons, but for simplicity, let’s say 1 Kgf = 10 Newtons.
Rated dynamic radial load
The official definition of a dynamic radial load rating is: “a constant static radial load at which 90% of a set of identical chromium steel bearings (with only the inner ring rotating) can withstand one million revolutions before showing signs of fatigue”. One million rpm does sound like a big number, but let’s check again. If operated at around 10,000 revolutions per minute (rpm) with maximum dynamic load applied, the bearings would only last an hour and a half (approximately 100 minutes). These numbers are used to calculate rating life, but bearings should not be subjected to anywhere near such loads in normal applications unless you don’t expect them to last very long. If long life is required, it is best to limit the actual load to between 6% and 12% of the bearing’s dynamic load rating. Can withstand heavier loads, but life will be shortened. AISI440C/KS440 stainless steel bearings will support approximately 80% – 85% of the chromium steel bearing load. The load rating of a thrust bearing is based on a constant axial load for one million revolutions. Aubearing’s team of experts can help provide life rating data for a variety of different bearings.

Rated static radial load
The static radial load rating is the pure radial load (or axial load for thrust bearings) that causes complete permanent deformation of the ball or raceway. Static loads close to this number may be bearable for some applications, but not where any smoothness or accuracy is required. The static load rating of stainless steel bearings is approximately 75% to 80% of the load rating of chromium steel bearings. The load capacity of bearings may be limited by the lubricant. Some lubricants are only suitable for light loads, while others are designed for high load applications. Full complement bearings have higher load ratings. The axial load capacity of radial ball bearings can be increased by specifying loose radial clearance.
Rated axial load
Heavy-duty bearing types such as the 6200 or 6300 series can handle axial loads up to 50% of the rated static radial load. Due to their shallow raceways, thin-section deep groove ball bearings can only withstand axial loads between 10% and 30% of the bearing’s rated static radial load. Note that these numbers are based on purely axial loads. Additional radial loads or moments (misalignment loads) will have an impact on the axial load capacity. Exceeding the total recommended limits for combined loads will adversely affect bearing life. Full complement ball bearings have filling grooves machined on the inner and outer rings. This groove interferes with the rotation of the ball under axial loads, so the use of full complement bearings under axial loads is not recommended.
Effect of bearing load on life
Selecting the right bearings with adequate load capacity is critical to the efficient operation and durability of machinery. Too little capacity can lead to premature failure, downtime, repairs and safety risks, while too much load can lead to overheating, wear and tear and increased energy consumption. Incorrect load capacity can lead to catastrophic failures, safety hazards and costly downtime. Consult an expert or bearing manufacturer to ensure proper capacity for your application.
The basic fatigue life, known as L10, is calculated as the number of revolutions at which 90% of all bearings in a specific group reach or exceed the calculated time to failure (probability of failure: 10%). Look up the bearing’s dynamic capacity in a catalog, estimate radial load and rotational speed, and you can calculate your own L10 bearing life. The L10 life calculation indicates the bearing life under your operating conditions with 90% accuracy.
Therefore, loadings are usually obtained by multiplying theoretical values by various factors over time. There’s a lot of math involved, but you can find the information on the Aubearing website.
Choose the right bearing
When selecting bearings, consider application requirements, load type, speed, environment and temperature. Ball bearings are suitable for low to medium loads, while roller bearings are suitable for higher loads. Sliding bearings are suitable for low-speed, high-load machinery. Maintain bearings with regular inspection, cleaning and lubrication to ensure optimal performance and service life. There are a number of things manufacturers can do to ensure their bearings have a long and successful service life. The first step is to limit radial loads to between 6% and 12% of the bearing’s dynamic load rating. Although bearings can withstand higher loads, their lifespan is shortened.
The next step is to choose the right material. Aubearing’s experience as a specialist in thin-section, corrosion-resistant, miniature bearings and ceramic bearings Choosing the right bearing type can also make a difference. Although all radial ball bearings have some thrust load capacity, if larger thrust loads are present, it is usually better to use heavy-duty bearings with deep raceways, as these bearings can withstand axial loads up to 50% of the static radial load. Load rating.
Although thin-walled bearings (where the difference between the bearing’s inner and outer diameters are small) are great for compactness and weight savings. Because the raceways are shallow, they can only support axial loads between 10% and 30% of the bearing’s rated static radial load. Additional radial loads or moment loads will further reduce thrust load capabilities. Excessive thrust loads on thin-walled bearings can cause the balls to come dangerously close to the top of the raceway. By selecting the right bearing type and considering the key factors that control radial and thrust loads, engineers can ensure they continue to innovate while delivering the highest levels of accuracy, smoothness and bearing life.

Conclusion
To select the correct bearing for an application, it is critical to understand bearing loads. Radial, axial and centrifugal loads determine the appropriate load capacity. Aubearing offers a wide range of bearings suitable for different conditions and applications, as well as high-quality products and expert advice. Aubearing primarily manufactures ball bearings and roller bearings for use in various industries in the United States and around the world.
Our industrial-grade bearings must not only provide long service life according to rolling fatigue standards, but they must also be structurally held together to protect against shock, overloading and occasional high-speed excursions. To this end, the design of every bearing is optimized, including our large bore bearings.