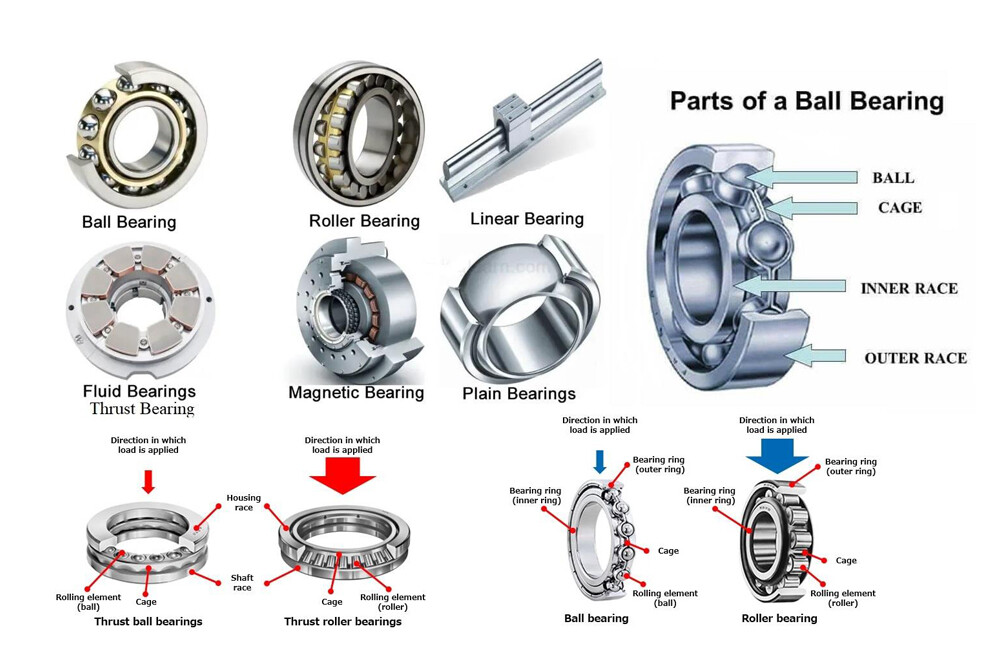
Bearing Manufacturer & Supplier
Specialize in ball bearings, roller bearings, thrust bearings, thin section bearings etc.
The Ultimate Guide to Ball Bearing Applications
Ball bearings are used in many machines with rotating motion, from fans and car engines to large medical precision equipment, ensuring smooth and efficient operation. Ball bearings are rolling bearings that serve three primary functions while facilitating motion: carrying loads, reducing friction, and positioning moving machine parts. A good understanding of ball bearing applications can help us grasp their important role in making many mechanical systems run efficiently.
Table of Contents
ToggleBall Bearing Design
Ball bearings consist of four main components: inner ring, outer ring, balls (rolling elements) and cage (ball separator). Ball bearings use the rolling motion of balls to reduce surface contact and friction between moving planes. The rotation of the balls results in a lower coefficient of friction compared to flat surfaces rubbing against each other. Because there is little surface contact between the ball and the race, the dimensional load capacity of ball bearings is generally lower than that of other rolling bearings. The outer ring of the ball bearing is fixed and installed into the machine. The function of the rolling elements is to carry the load and distribute the load throughout the raceway. The rolling elements rotate at a different speed than the inner ring, but they rotate around the inner ring. The separator acts as a barrier to prevent the balls from hitting each other. The separator is located between the balls.

Ball bearings can include one or rows of balls, depending on application requirements. Single-row bearings offer greater precision and accuracy, but usually need to be installed in pairs to evenly distribute loads. Double-row ball bearings save space because they do not require a second bearing and can provide higher load capacities, but require better alignment when installed. Multi-row ball bearings are sometimes used in applications with extremely high load requirements. Ball bearings can also be equipped with a flange or housing, which is the unit that secures the bearing to the mounting surface. This simplifies installation and axial positioning and improves bearing safety. Different types of housing units are available depending on the bearing location and mounting surface dimensions.
The role of ball bearings
As we all know, ball bearings are one of the most commonly used mechanical parts and are used in both domestic and industrial environments, such as: automobiles, household appliances, bicycles, motorcycles, drills, motors, turbines, office equipment, medical equipment, robots, etc. As mentioned earlier, this is because ball bearings play three key roles:
Carrying load
Each ball bearing can carry a corresponding load. Therefore, ball bearings with double or multiple rows can handle heavier loads and remain durable. Bearings have static and dynamic load-carrying capabilities, which are reflected in axial retention limits.
Reduce frictional resistance
In theory, only magnetic bearings do not experience friction, while ball bearings can greatly reduce frictional resistance. Ball bearings minimize friction between the two races, but some friction is still needed to stabilize one or the other race. Allowing this reduced friction resistance means that temperatures, wear rates and the chance of parts failure are also reduced.

Positioning moving mechanical parts
In a mechanical system, “joints” are always needed to connect parts. For example, in the case of a rotating component such as a bicycle fork and its wheels, ball bearings act as a joint that holds together two mechanism components (sometimes with different axes).
As factories, equipment and industrial manufacturing evolve, diverse bearing applications are needed to reduce time, space and downtime. Ball bearings can significantly reduce wear between parts, effectively combine moving and static components without manual operation, and are capable of carrying specified loads, thus greatly reducing the possibility of mechanical failure.
Types of ball bearings
Ball bearings work by transferring load from the outer ring to the balls and then to the inner ring. Since the spherical shape of the ball only touches the inner and outer rings at very small points, the friction is very small. However, this can also become a big trouble if the bearings are used incorrectly. Since the contact area for a given load is small, the ball can deform and damage the bearing if overloaded. Therefore we must understand the various types of ball bearings. Ball bearings are available in many different designs and applications, serving specific industrial applications and load types. Some common types of ball bearings include:
The raceway grooves of ball bearings are very deep; the arcs of their inner and outer rings are slightly larger than the diameter of the ball. This design is ideal for high-speed applications and can handle both radial and axial loads. Deep groove ball bearings have low friction, low temperature and low noise during operation, so they are suitable for various industries.

Thrust ball bearings are designed to withstand thrust loads during high-speed operation. They consist of three parts: a seat ring, a shaft ring and a steel ball cage assembly. The shaft ring that matches the shaft is called the shaft ring, and the seat ring that matches the housing is called the seat ring. According to the stress situation, they are divided into one-way thrust ball bearings and two-way thrust ball bearings. One-way thrust ball bearings can withstand one-way axial load. Bidirectional thrust ball bearings can withstand bidirectional axial loads, in which the shaft ring matches the shaft. The mounting surface of the seat ring is a spherical bearing, which has self-aligning performance and can reduce the impact of installation errors.

Angular contact ball bearings have raceways on the inner and outer rings, and the inner and outer rings can move relative to each other along the bearing axis. This type of bearing is particularly suitable for bearing compound loads, that is, loads acting simultaneously in the radial and axial directions. The axial load bearing capacity of angular contact ball bearings increases with the increase of contact angle α. Larger contact angles provide higher axial load capabilities, while smaller contact angles increase speed capabilities. The contact angle is the angle between the line connecting the contact points of the ball and the raceway in the radial plane and the vertical line of the bearing axis. High-precision and high-speed bearings usually have a contact angle of 15 degrees. Angular contact bearings are available in single row or double row. Single row minimizes wobble and friction issues, while double row avoids multiple bearing issues such as diameter matching and runout matching.

Thin-section bearings are actually a type of deep groove ball bearing, designed for maximum economy in applications where space is limited. Thin-section bearings are available in open and shielded designs with the smallest possible difference between the outer and inner diameters, keeping the assembly narrow and lightweight. The use of thin-section bearings keeps friction low, although the miniaturization of the housing does reduce load capacity compared to standard ball bearings.

Four point contact ball bearings
The inner ring of this type of bearing is split into two parts, giving the ball four points of contact with the raceway. This unique design enables these bearings to withstand axial loads in both directions, as well as radial and axial loads simultaneously. Designed for harsher conditions, they can handle higher load capacities than angular contact bearings. They also eliminate the need for multiple bearings and are space-saving than double-row bearings. These bearings are best suited for low to medium speed applications with high oscillatory motion.

Aligning ball bearings consist of two rows of balls, an inner ring with two deep raceway grooves, and an outer ring with a spherical raceway. Although their load capacity is limited, they are capable of correcting misalignments that occur during operation. This makes them ideal for long-axis applications such as transmissions or textile machinery. They are also used in a variety of other applications due to their low coefficient of friction, low maintenance requirements and high-speed performance.

Precision miniature ball bearings are constructed to provide greatly improved performance for demanding applications. Optimal materials and construction enhance performance levels at high speeds and challenging conditions. They are typically used where high precision, rigidity, noise reduction, longevity or reduced friction are required, such as in the aerospace, robotics or medical industries.

Ball bearings are made of various materials, including steel, ceramic or plastic. These types of ball bearings differ in operating speed, temperatures they can reach, and other characteristics relevant to the purpose of the ball bearing. Understanding the advantages and disadvantages of each material will allow you to make a informed decision when you need ball bearings.
Steel Bearings
Steel bearings use components made entirely of steel or steel alloys that contain trace amounts of other elements in their composition. They are ideal for handling very large loads while achieving high rotational speeds when rotating. Steel ball bearings can provide you with very precise measurements because they are manufactured with high precision. Their properties can be used in cars, motorcycles, bicycles, vibrating screens, conveyors, etc. Unfortunately, steel bearing materials can cause corrosion in the presence of water or gas, which changes the chemical composition of the steel itself. When these types of ball bearings are used in manufacturing and other harsh environments, they can also be very heavy and noisy.

Steel bearings also require constant lubrication of the steel metal to keep them working efficiently. If not properly maintained, bearings may fail and fail to live up to their expected service life. Manufacturers produce and sell steel ball bearings in different styles. You can buy bar bearings with a higher carbon content that are heat treated or hardened by other methods. Variations in carbon content in steel bearings can affect their performance.
Ceramic ball bearings
Ceramic ball bearings are often manufactured as “hybrid bearings” which use an outer ring, inner ring and cage made of steel, while the ball itself is made of ceramic. Ceramic properties allow them to operate at rapid rotations per minute while maintaining low operating temperatures and limiting the noise they produce. These ceramic-steel hybrid designs can be damaged by corrosion, but the ceramic balls themselves are less susceptible to corrosion than steel materials and are durable and lighter than steel ball bearings. Ceramic ball bearings can be used in electrical applications where steel ball bearings cannot be used because ceramic ball bearings do not conduct electricity, but they are also very expensive. Ceramic ball bearings can withstand high temperatures, allowing them to operate at higher speeds.

Ceramic ball bearings are 40% lighter than steel ball bearings. Engineers typically make them from zirconium oxide, silicon carbide, and silicon nitride to achieve these chemical and physical properties. They are used in angular bearings, thrust bearings, pillow block bearings, needle roller bearings and roller bearings. Ceramic materials may be stronger than steel, but they are generally harder than ball bearing materials.
Plastic Ball Bearings
Recent innovations have produced plastic ball bearings that use plastic rings and plastic cages, and can come in the form of balls made of plastic, glass, or stainless steel. The most common ball materials for plastic ball bearings are stainless steel balls or glass balls. Plastic ball bearings with glass balls are a good choice when you can’t use metal. They have high chemical resistance and are lighter in weight than steel balls. Most plastic ball bearings are self-lubricating, lightweight, corrosion-resistant, and quiet in operation. Unfortunately, plastic ball bearings cannot withstand high temperatures like other ball bearings and sometimes cannot handle loads as high as they do.

Ball bearing replacement
Ball bearings should be inspected when they have reached their predicted service life or show signs of material degradation. Some symptoms of bad ball bearings could be excessive noise or overheating. In the case of open bearings, first assess the condition of the lubricant, then remove the balls from the races and clean the surfaces thoroughly. Surfaces should be carefully cleaned and inspected for wear or abnormalities. In the case of permanently dust-proof or sealed ball bearings, provide initial torque and observe the bearing rotating freely. Replace damaged bearings based on the results of appropriate inspections.

Ball bearing applications
Ball bearings are very important in most daily activities. The most widely used type of ball bearing is used in common equipment that the vast majority of people heavily rely on in their daily lives.
One of the most typical uses of ball bearings is in the field of transportation, as all modes of transportation rely on wheels or rotating parts. A common use of ball bearings is in the wheels of cars, motorcycles, bicycles, and skateboards. Likewise, they are found in electric vehicles, wheelchairs, and any other application that utilizes wheel rotation. In autonomous vehicles, ball bearings are absolutely essential. The minimum number of bearings in a car is 36, with most models actually having ball bearings. Ball bearings are used in gearboxes, wheels, engines, transmissions, air conditioning compressors, suspensions, etc. As you can imagine, they are also vital to aircraft manufacturing, as well as any other type of vehicle.

Household Appliances
The average home has at least 15 different appliances that use bearings, and that’s a conservative estimate. Ball bearings are commonly used in refrigerators, air conditioners, ovens, dishwashers, generators, washers and dryers, microwaves, blenders, ceiling fans, vacuum cleaners, food processors, and even kitchen or bathroom drawers.

Personal Device
In addition to typical household appliances, many personal devices also contain bearings. This may include computer fans, game consoles, fitness equipment, skateboards, etc. Although you may not interact directly with bearings often, you rely on them for most routine tasks. If you use any electrical equipment, it’s likely that it uses ball bearings. Even in basic items, such as cell phones, ball bearings are used to facilitate rotational motion.

Manufacturing and Industry
Manufacturing is absolutely inseparable from ball bearings. Ball bearings are needed in manufacturing equipment in food processing, mold making and paper product production, as well as nearly every consumer product imaginable. A wide variety of ball bearings are used in agricultural equipment used in production, packaging and transportation. Ball bearings in construction equipment are used in the construction of all the homes and buildings where we live and work.

Engine: Ball bearings enhance engine operation and improve fuel efficiency.
Wheels: They support the weight of the vehicle and ensure smooth rotation of the wheels.
Transmission: Within the transmission, ball bearings facilitate smooth gear transitions.

Aerospace industry
Aircraft engines: Bearings allow for consistent rotation of the rotor, which is critical to aircraft safety.
Landing Gear: They ensure smooth movement during takeoff and landing.
Control Systems: Ball bearings are critical to the precise operation of aircraft control mechanisms.

Robot arms: Thin-section bearings ensure precise and controlled movement during tasks such as welding.
Joints: In robots, ball bearings allow for smooth and natural movement.

Surgical Tools: Bearings in surgical instruments allow for smooth, precise movement during surgery.
Medical Scanners: MRI and CT scanners use ball bearings for smooth, accurate rotation, ensuring clear diagnostic images.
Prosthetics: Ball bearings in prosthetics provide users with smoother, natural movement, improving their mobility.

This blog delves into the question, “What are the guidelines for ball bearing applications?”, showcasing their wide range of applications across different industries. Ball bearings are critical components in many commercial, industrial and scientific applications, enabling rotation with extremely low friction and high durability. Choosing the right bearing for your application requires careful consideration of speed, load conditions and temperature to prevent premature ball bearing failure. The ball bearings manufactured by Aubearing are known for their quality construction and excellent performance characteristics, making them a supplier of bearings to different industries in than 50 countries around the world, ranging from handheld devices to medical equipment and high-power motors.