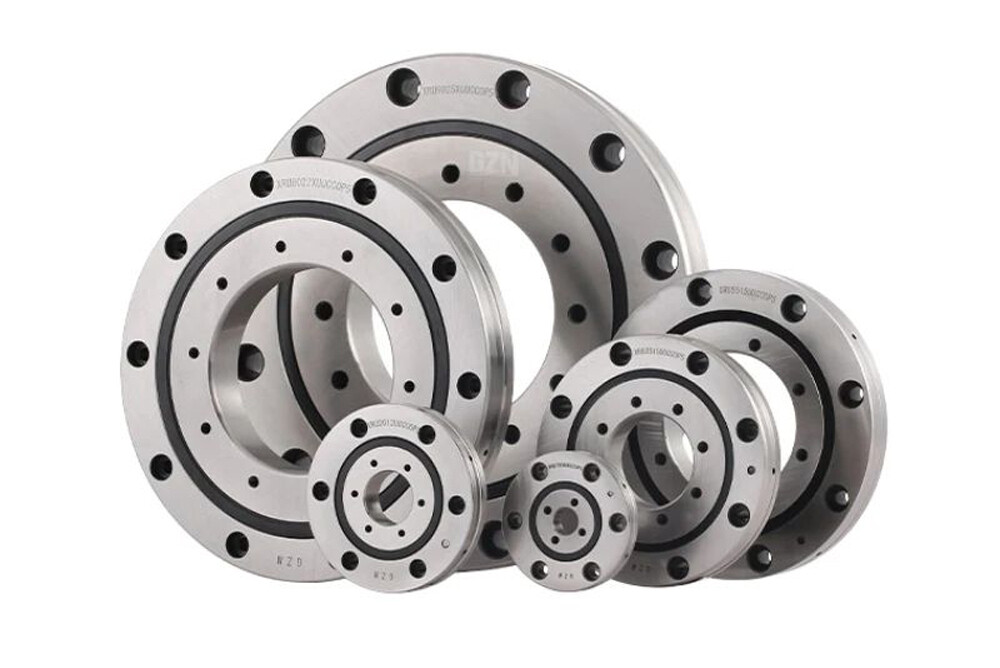
Bearing Manufacturer & Supplier
Specialize in ball bearings, roller bearings, thrust bearings, thin section bearings etc.
You Should Know About Robot Bearings
As one of the key parts of industrial robots, robot bearings mainly refer to thin-section bearings and crossed roller bearings. In addition, there are harmonic reducer bearings, linear bearings, spherical bearings, etc. The reason why industrial robots’ thin-section bearings are better than other bearings: The development of modern industrial robots tends to be lightweight, and bearings must be installed in a limited space, with small size and light weight. At the same time, the robot’s high load, high rotation accuracy, high running stability, high positioning speed, high repeat positioning accuracy, long life, and high reliability require that the supporting robot bearings must have high load-bearing capacity, high precision, and high stiffness. , low friction torque, long life, etc. Bearings for industrial robots are most suitable for joints or rotating parts, rotating tables of machining centers, rotating parts of manipulators, precision rotating tables, medical robot arms, etc.
Table of Contents
ToggleCrossed roller bearings
The rolling elements of crossed roller bearings, such as cylindrical rollers or tapered rollers, are arranged perpendicularly to each other on the 90-degree V-shaped groove rolling surfaces through spacers. Crossed roller bearings can withstand multi-directional loads such as radial load, axial load and moment load. The size of the inner and outer rings has been miniaturized. It is very thin and close to the extreme small size. It has high rigidity, and the accuracy can reach P5, P4, and P2 levels, and the service life is than 6000h.

Excellent rotational accuracy
The internal structure of crossed roller bearings uses rollers arranged perpendicularly at 90° to each other. Spacers or isolation blocks are installed between the rollers to prevent the rollers from tilting or rubbing against each other, effectively preventing rotational torque. increase. In addition, there will be no contact or locking between the rollers; and because the inner and outer rings are separate structures. The gap between them can be adjusted to ensure high-precision rotation even if preload is applied.
Simple installation
The outer ring or inner ring that is separated into two parts is fixed together after the rollers and retainers are installed, so the installation operation is very simple.
Ability to withstand large loads
Because the rollers are arranged vertically to each other through spacers on the 90° V-groove rolling surface, this design enables crossed roller bearings to withstand large radial loads and axial loads. Loads and moment loads in all directions.
Saving installation space
The dimensions of the inner and outer rings of crossed roller bearings are minimized, especially the ultra-thin structure is close to the limit of small size and has high rigidity, so it is most suitable for joints or rotating parts of industrial robots, CNC It is widely used in rotary tables of machining centers and medical equipment.
Crossed roller bearing types
RB (for outer ring separation and inner ring rotation): This series model is the basic type of crossed cylindrical roller bearings. The dimensions of the inner and outer rings are minimized. Its structure is that the outer ring is a separate type and the inner ring is integrated. The design is suitable for parts requiring high rotation accuracy of the inner ring.
RE (inner ring separation type, outer ring rotation type): This series of models is a new model based on the design concept of the RB type. Its main dimensions are similar to the RB type. Its structure is that the inner ring is a separate type and the outer ring is an integrated design, which is suitable for parts that require high rotation accuracy of the outer ring.
RU (inner and outer ring integrated type): This series of models does not require fixing flanges and support seats because the mounting holes have been processed. In addition, due to the integrated inner and outer ring structure with a seat, installation has almost no impact on performance, so stable rotation accuracy and torque can be obtained. Both the outer and inner rings can rotate.
CRB (separable outer ring, inner ring rotation): Its structure is a full complement roller bearing with a separated outer ring and an integrated inner ring without a cage. Suitable for machinery requiring high rotation accuracy of the inner ring.
CRBC (separable outer ring, inner ring rotation): Its structure is that the outer ring is separated, the inner ring is an integrated design, and a full complement roller bearing with a cage. Suitable for machinery requiring high rotation accuracy of the inner ring.
CRBH (inner and outer ring integrated type): This series of models has an integrated inner and outer ring. Both the outer and inner rings can rotate.
RA (outer ring separation type, inner ring rotation): This series of models is a compact model that reduces the thickness of the inner and outer rings of the RB type to the limit. Suitable for parts that require light weight and compact design, such as industrial robots and rotating parts of manipulators.
RA-C (single crack type): The main dimensions are the same as RA type. Since this model has a notch structure in the outer ring, the outer ring also has high rigidity, so it can also be used for outer ring rotation.
XR/JXR (crossed tapered roller bearings): This type of bearing has two sets of raceways and rollers, which are combined at right angles to each other, and the rollers are staggered and opposite. The cross-sectional height of the bearing is similar to that of a single-row bearing, thus saving space and bearing seat material. The large cone angle and tapered geometric design make the overall effective span of the bearing several times the width of the bearing itself. Crossed tapered rollers can withstand high overturning moments and are suitable for machine tools, including vertical boring machines and grinder tables, machine tool precision circular indexing tables, large gear hobbing machines, turrets, industrial robots, etc.
Thin Section Bearings
The cross-sections of each series of thin-section bearings are mostly square, and the dimensions are designed to be fixed values. In the same series, the cross-sectional size is constant and does not increase with the increase of the inner diameter, so it is called a thin-section bearing. Thin-section robot bearings are mostly used in waists, elbows, wrists and other parts of industrial robots that require small cross-sections and limited space. When the inner diameter is the same, thin-section bearings contain steel balls than standard rolling bearings, which improves the force distribution inside the bearing, reduces the elastic deformation at the contact point between the steel balls and the groove, and improves the bearing capacity. The most famous Kaydon Reali-Slim thin section bearing is composed of seven open series and five sealed series. There are three types of open series: radial contact type C, angular contact type A and four-point contact type X. In addition, there are thin-section bearings in the 6700, 6800, and 6900 series, as well as options such as dust covers, flanges, and stainless steel.
Type A -angular contact thin section bearings
Kaydon Reali-Slim® Type A angular contact ball bearings have sufficient radial clearance to create a large contact angle to resist axial loads. Standard Reali-Slim® Type A angular contact ball bearings use extra-deep ball grooves (25% of ball diameter) with a contact angle of 30°.
The distinguishing feature of Kaydon Type A thin section bearings is the assembly method. One ring (usually the outer ring) is countersinked to reduce one shoulder of the raceway so that, with the help of the temperature difference between the two rings, the outer ring can fit over the inner ring, ball and separator assembly. This provides a non-separable bearing capable of carrying greater radial loads while resisting considerable axial forces in one direction. After axial force is applied, the surfaces of the inner and outer rings are approximately flush to minimize preload adjustment. Because of their thrust capability in only one direction, Kaydon Type A thin section bearings should generally be installed in pairs (back-to-back, face-to-face, in series) with another identical bearing so that axial force is present to establish and maintain the contact angle and minimize backlash. Axial motion under thrust load.

Back-to-back arrangements provide greater rigidity under moment loads and should be used when the space between individual bearings is small or when a pair of adjacent bearings is used.
Face-to-face arrangement has a higher tolerance for misalignment between the shaft and the housing, which should be considered when there are multiple bearing pairs on the shaft. When individual bearings are mounted face to face, they must be sufficiently spaced to resist moment loads. If required, facing pairs can be mounted with another bearing to form a “fixed float” arrangement, keeping the pair in a fixed position.
Tandem bearing sets have unidirectional thrust capabilities and must be mounted opposite another bearing or bearing set.
Type C -radial contact bearings
Kaydon Type C radial contact bearings are designed to achieve ball to race contact in the ball center plane when purely radial loads are applied and no thrust is present. Necessary radial clearance can be increased or decreased to meet operating conditions.
Kaydon Reali-Slim® Type C radial contact ball bearings are single row radial ball bearings with extra-deep ball grooves in both rings (groove depth = 25% of ball diameter). The bearing is usually assembled by eccentric displacement of the inner ring within the outer ring, which allows half the number of balls to be inserted. After the balls are inserted, the race is positioned concentrically and the balls are spaced around the entire circumference to allow assembly of the separator. This method of assembly is often called “Conrad assembly”.

Another assembly method is to insert the balls into a “fill groove” created by notching the raceway shoulders of one or both races. This method allows for the assembly of up to complete balls to increase load capacity. With filled slots, both dynamic radial and thrust capabilities are compromised by disruption of the ball contact path, and rotational speed must be limited. Kaydon Type C thin wall bearings perform best with small diameter clearance (the gap between the ball and the race). Standard Reali-Slim® Type C radial contact ball bearings provide clearance that allows:
Interference fit between bearing race and mounting parts
Different thermal expansion or contraction of steel races
The misalignment between the shaft and the housing may require corresponding clearance adjustment
Type x four-point thin section bearings
Kaydon X-type bearings have a unique “Gothic Arch” construction that allows four points of contact between the ball and raceway. Kaydon Type X thin section bearings are assembled using the Conrad method or the filled groove method. Type X bearings have the same groove depth as Type A and Type C bearings (25% of the ball diameter). The deep grooves combined with the four-point contact geometry enable the bearing to resist a combination of radial, thrust and moment loads. The Kaydon X-bearing implementation resembles a pair of A-bearings in tandem back-to-back.
Similar to C-type bearings, X-type bearings usually have radial clearance. The nominal contact angle and thrust capacity of type X bearings do not depend on this clearance. On the contrary, when the thrust or moment load is large, the clearance should be minimized to prevent the contact angle from being too large. For many applications requiring greater stiffness, Reali-Slim X-type bearings are equipped with internal preload. This is achieved by using balls with a diameter larger than the space between the raceways. In this case, the balls and raceways will have some elastic deformation in the absence of external loads. Type X bearings are designed for stand-alone use. Using two X-bearings on a common shaft may produce unacceptable frictional torque.

Harmonic reducer bearings
The harmonic reducer mainly uses a flexible bearing. The harmonic generator is used to cause the flexspline to produce controllable elastic deformation. The controllable elastic deformation of the flexible bearing is used to transmit motion and power. It is mainly used in robot joints with small and medium torques. , the accuracy is at P5 level (some P4 levels), the service life is than 6000h, and it has the characteristics of compact structure, high movement accuracy and large transmission ratio.

Key technologies of robot bearings
The development of modern industrial robots tends to be lightweight, but lightweight and high performance are contradictory. This requires that the design of robot bearings be fully optimized. Thin-walled bearings for industrial robots must not only ensure sufficient load-bearing capacity, but also require precise positioning and flexible operation. Therefore, the bearing design analysis and the determination of the main parameters cannot only use the rated dynamic load as the objective function, but must use the rated dynamic load as the objective function. Indicators such as stiffness and friction torque are used as objective functions to carry out multi-objective optimization design. At the same time, the finite element analysis method of thin-walled bearings based on the deformation of the ferrule and frame must be used.

(1) High-precision detection technology for dynamic quality of robot bearings;
(2) Micro-deformation heat treatment processing technology of robot bearing rings;
(3) Bearing ring precision grinding processing technology based on grinding deterioration layer control;
(4) Precise control technology of negative clearance of robot bearings;
(5) Precision assembly technology of robot bearings;
(6) Non-contact measurement technology for robot bearing rings;
Factors to consider when choosing robot bearings
The robot bearing model is generally selected by the user’s technical personnel based on the use conditions and load of the supporting products. Business personnel mainly understand whether the actual load of the user is consistent with the selected bearing. If the bearing does not meet the usage requirements, the customer should be advised to change the model as soon as possible. However, unless there is a special product, there will generally be no problem in selecting the model.
Selection of bearing clearance
When purchasing a bearing, users generally only tell them what model and grade it is, and rarely put forward requirements for the bearing’s clearance. They need to understand the bearing’s usage conditions. The bearing’s speed, temperature, and fit tolerance are all directly related to the bearing’s clearance. s Choice.
Bearing grease selection
The selection of grease is generally based on the bearing’s speed, temperature resistance, noise requirements and starting torque.
Selection of bearing seal types
There are two types of seals: contact seals and non-contact seals. Contact seals have good dustproof performance but large starting torque. Non-contact seals have small starting torque, but the sealing performance is not as good as contact seals.
Robot bearing maintenance
Robot bearings require regular maintenance. Common maintenance methods include cleaning, oil change and bearing replacement.
(1) Cleaning: Robot bearings will accumulate dust and dirt during application, so they need to be cleaned regularly to ensure the normal operation of the bearings.
(2) Oil change: The lubricating oil of robot bearings needs to be replaced regularly to ensure the lubrication effect of the bearings.
(3) Replace bearings: If the robot bearings are damaged or faulty, they need to be replaced in time.
Robot bearing fault diagnosis
Robot bearing failures are mainly manifested by noise, temperature increase, vibration increase and other phenomena. For bearing fault diagnosis, vibration analysis and failure mode analysis are usually required.
(1) Vibration analysis: Through vibration analysis, the type, location and cause of bearing failure can be determined. Vibration analysis can be performed using equipment such as laser interferometers and acceleration sensors.
(2) Failure analysis: Failure modes of robot bearings usually include wear, fatigue and improper maintenance. Through failure mode analysis, the cause of bearing failure can be determined so that correct repair measures can be taken.
Robot bearings are an important part of robots, and different types of bearings are suitable for different robot application scenarios. The installation, maintenance and fault diagnosis of robot bearings are indispensable links in robot production and application. To ensure the high quality and long-term performance of robots, companies should pay attention to the selection, installation, maintenance and fault diagnosis of robot bearings.