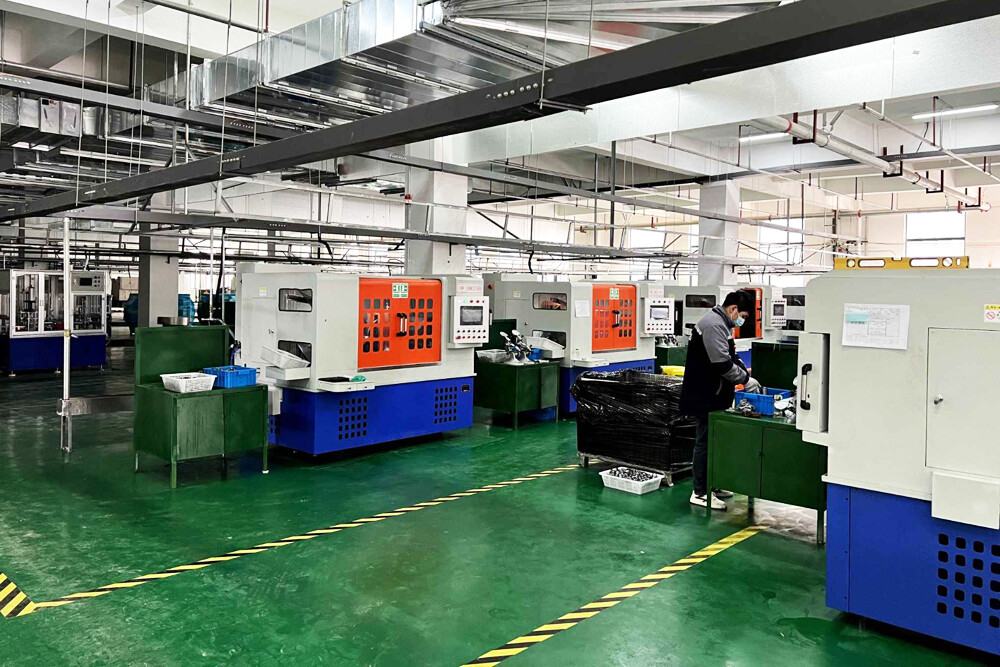
Bearing Manufacturer & Supplier
Specialize in ball bearings, roller bearings, thrust bearings, thin section bearings etc.
Manufacturing and Maintenance Thin Section Bearings
Kaydon Thin-section bearings are a precision special type of bearings, generally consisting of an inner ring, an outer ring, rolling elements and a cage. Thin-section bearings have a square cross-section and are designed to have fixed dimensions of width and thickness (cross-section) that do not increase with the increase in inner diameter. Thin-section bearings have the advantages of light weight, compact structure, and small moment of inertia. They are widely used in high-end product fields such as industrial robots, aerospace vehicles, aerospace satellites, and medical care, and the market size is gradually increasing. In this blog, we will introduce in detail the processing process of Kaydon thin-section bearing rings, processing difficulties, and solutions for protecting thin-section bearings.
Table of Contents
ToggleThin section bearing manufacturing
Although thin-section bearings have many advantages, manufacturing constant-section bearings is a particularly difficult task, especially processing the rings of constant-section bearings. The cross-sectional area of thin-section bearings is small, which results in small radial wall thickness and poor rigidity. It is easy to produce large radial deformation. Therefore, the ferrules are subjected to many processes such as turning, heat treatment, and grinding. In order to avoid ring roundness deformation, poor flatness, defects such as ellipses, edge circles, and end face warpage deformation, special means need to be used to process the bearing rings.

Forging
For large size and Kaydon thin section bearing rings with small aspect ratio, two or pieces are produced by forging together. After the rough grinding process, the rings are separated by wire cutting to reduce the processing difficulty of the forging process. , reduce ferrule deformation and end face processing allowance, save raw materials, and improve production efficiency.

Turning process
In the process of turning thin-section ferrules, the main thing is clamping and positioning to avoid excessive cutting force, unreasonable fixture design, cutting thermal deformation and vibration during the cutting process from affecting the processing accuracy. In order to reduce deformation due to excessive machining stress, use steel soft claws with a large envelope circle contact area and unquenched clamping rings for rough turning, such as using a multi-point clamping chuck (twelve-point clamping chuck). clamp or twenty-four-point clamp); change the positioning clamping scheme (change radial clamping to end face positioning and pressing method); adjust process parameters (high-speed cutting, small back cutting amount, larger main deflection angle of the tool, larger Small tool tip arc radius, reasonable selection of cutting fluid, etc.). Add an additional tempering after rough turning to eliminate stress. Afterwards, the end face is soft ground, and then the ferrule is finely turned.

Heat treatment process
During the heat treatment process, the internal structure of the ferrule undergoes phase transformation, mainly from austenite to martensite, the density becomes smaller, the volume expands, and tissue stress is generated; in addition, the ferrule changes from high temperature (thin-section bearings are generally 830 to 845 ℃ ) is rapidly quenched and cooled in its expanded state, producing thermal stress. When these two internal stresses exceed the yield limit of the material, the material will undergo plastic deformation. Usually, die quenching is used to control the deformation. When there is no condition for die quenching, and the outer diameter of the ferrule after quenching is too large to exceed the process requirements, the method of comprehensive shaping and then tempering is used to correct it, so that it can be controlled within the process requirements. within the range.

Grinding
The main things in grinding are: selecting appropriate grinding equipment, processing methods and grinding process parameters. For example, the method with reinforced rings and a “one-on-two” structure is used for processing; the outer diameter surface is ground by multiple fine adjustments of the machine tool; tempering stabilization is added during the process to ensure that the grinding quality of the ferrules is satisfactory. Process requirements.

Causes of damage to thin-section bearing cages
The thin-section bearing cage plays the role of isolating the rolling elements at equal distances, preventing the rolling elements from falling, and guiding and driving the rolling elements to rotate. Generally speaking, the cage of constant-section thin-section bearings will not be damaged under reasonable working conditions, but incorrect operations in daily production will reduce the service life of the bearing cage. Common cage failure phenomena include: cage damage, loose or broken rivets, broken cage, and scattered rolling elements. So, what are the reasons for the fracture of the equal-section thin-section bearing cage?
Insufficient lubrication
When the bearing is running, if the lubrication work is not done well, it will affect the normal operation, so be sure to ensure that the lubricating oil is sufficient for the use of the bearing. If the lubricating oil is not enough, the thin-section bearings of equal cross-section will be in a In a lean oil state, it will be easier to cause bite wear, which will worsen the condition of the working surface, so that the tears from the bite wear will enter the cage, causing the cage to generate abnormal loads. This may cause the cage to break.
Abnormal load on cage
When the cage has problems during installation, such as improper installation, tilt, excessive interference, etc. It will be easier to reduce the clearance, which will intensify friction and heat during use, soften the surface, and cause premature abnormal peeling. As the peeling expands, the peeling foreign matter will enter the cage pockets, causing the cage to run blocked and cause Additional loads are generated, which aggravates the wear of the cage. Such worsening circulation may cause the cage to break and be scrapped.
Foreign body invasion
In fact, the intuitive reason for the cage to break is because foreign matter enters the cage. Once the foreign matter enters, it will affect the operation of the cage, especially some hard foreign matter, which will increase the wear of the cage and produce abnormal additional loads. , which may cause the cage to break.
Creep phenomenon
Creep phenomenon is also one of the causes of cage fracture. The so-called creep phenomenon refers to the sliding phenomenon of ferrules. When the interference of the mating surface is insufficient, the load point moves in the peripheral direction due to sliding, causing the ferrule to deviate in the circumferential direction relative to the shaft or housing. Once creep occurs, the mating surface will wear significantly, and the wear powder may enter the inside of the thin-section bearing with equal cross-section, causing abnormal wear, raceway peeling, cage wear and additional load, and may even cause the cage to break.
Cage quality is too poor
The quality of the cage also affects its use. If the quality is very poor, it may break if it encounters wear during use. Especially if the cage is defective, it is likely to break. Common Defects include: cracks, large foreign metal inclusions, shrinkage cavities, bubbles, or riveting defects, missing nails, pad nails or gaps between the two halves of the cage, severe riveting damage, etc. These conditions may cause the cage to Broken.
Thin section bearing maintenance
After thin-section bearings have been used for a period of time, in order to ensure their normal operation, they must be cleaned and inspected regularly. In order to increase the service life of bearings, thin-section bearings of equal cross-section need to be maintained frequently.
Clean
First, clean the bearings. Put the bearings in gasoline and wipe off the sludge and dust on the surface of the thin-section bearings. If the bearings are rusty, use metallographic sandpaper to wipe and polish them until the bearing surface is rusty. Until there is no rough feeling to the touch.
Cleaning bearings is generally divided into two steps, namely coarse cleaning and fine cleaning. When performing rough cleaning, first remove the bearing and put it into a container, using a metal mesh as the bottom. This will prevent the removed bearing from directly contacting the dirt outside, and then use a brush to remove the grease and grease on the surface of the bearing. Dust, sludge and other sticky substances should be removed. At the same time, attention should be paid to the dirt on the surface of the thin-section bearings of equal cross-sections so as not to damage and contaminate the rolling surfaces of the bearings. After all the above has been cleaned, fine cleaning can be carried out.
During fine cleaning, first put the bearing into the cleaning oil, rotate it continuously, and clean the bearing carefully. At the same time, pay attention to keeping the cleaning oil clean during cleaning.
Anti-rust
After cleaning, use a dry rag to wipe the bearing dry, and then put it into anti-rust oil for soaking. During the soaking process, keep the bearing all in contact with the anti-rust oil, and continue to rotate the bearing, so that the anti-rust oil can be removed. Rust oil forms an oil film covering the surface of the bearing to prevent rust.
lubricating
After the anti-rust is completed, apply anti-rust oil, butter and other substances evenly on the surface of the bearing. The inner and outer rings, steel balls and cages of the bearing should be coated. When applying, apply while rotating the bearing to ensure anti-rust. The oil fully enters the inside of the bearing and lubricates the bearing.
Store
When storing thin-section bearings of equal cross-section, try to store them in an environment with a humidity lower than 65% and a temperature of about 20 degrees. It is better to store them on a shelf higher than 30cm, and try to avoid direct sunlight and cold walls in the storage place.
About Aubearing
Aubearing is a bearing manufacturing company integrating R&D, design, production and sales. Equipped with advanced testing instruments and production equipment: testing instruments include spectral metallographic structure detector, three-dimensional coordinate measuring machine, projection length measuring machine, BVT vibration and noise measuring instrument, roundness meter, profile meter, roughness meter, etc., and production equipment: Precision equipment such as fully automatic servo grinders, wire drawing superfinishing machines, surface finishing machines, assembly fitting machines, ultrasonic cleaning machines, etc., ensure our production strength and the stability of bearing quality. The rotation accuracy of the products produced reaches P6, P5, and P4 levels, and the vibration noise is Z2V2, Z3V3, and Z4V4.

Aubearing specializes in manufacturing ultra-thin equal-section bearings, industrial automation robot bearings, thin-walled deep groove ball bearings, thin-walled angular contact ball bearings and various non-standard special-shaped bearing series. Now the company has matured in R&D and manufacturing to replace Kaydon ultra-thin bearings and equal-section thin-walled ball bearings. Ultra-thin equal-section bearings consist of seven open series and five sealed series, with bore diameters ranging from 1 inch to 40 inches, and cross-sectional size ranges. From 0.1875×0.1875 inches to 1.000×1.000 inches; divided into three types: deep groove ball type (Type C), angular contact type (Type A), four-point contact type (Type X).






Thin-section bearings manufactured by Aubearing are widely used in transmission devices such as automobiles, bicycles, reducers, medical equipment, sports equipment, aviation, robot joints, machine tools, packaging equipment, textile machinery, semiconductor processing equipment, RV reducers and rotating worktables. The annual production capacity reaches than 2 million sets.