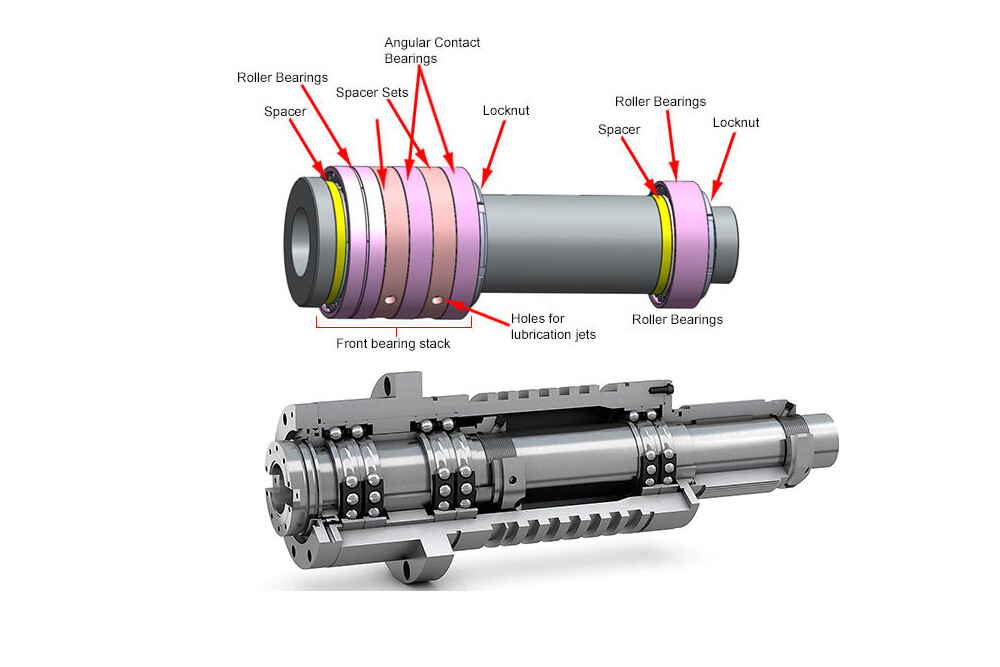
Bearing Manufacturer & Supplier
Specialize in ball bearings, roller bearings, thrust bearings, thin section bearings etc.
The Ultimate Guide to CNC Machine Tool Spindle Bearings
As technology develops, CNC machine tools are expected to be precise, efficient and reliable than ever before. To stay competitive, CNC machine tool manufacturing companies are investing in high-quality bearings to ensure optimal performance of their spindles. High-quality bearings can improve the efficiency and reliability of machine tool spindles, thereby increasing production and reducing wear and tear on machinery. Therefore, factors considered when selecting machine tool spindle bearings are very important to obtain accurate results. Load capacity, speed requirements, stiffness, lubrication, environmental conditions and noise levels are the main considerations guiding engineers when selecting spindle bearings. In this article, we will discuss the types commonly found in machine tool spindles and how to evaluate, inspect and monitor bearing operation to ensure optimal performance.
Table of Contents
ToggleWhat are spindle bearings?
A machine tool spindle has two main functions. One is to rotate the tool to turn, mill, grind or drill or tap the workpiece. The second is to transmit torque and speed to the cutting area. The purpose of machine tool spindle bearings is to precisely guide spindle movement to ensure optimal speed and accuracy. Bearings affect the speed, rotation, vibration, accuracy and temperature of machine tools, which in turn affects the quality of the final manufactured product. Bearings can be designed to facilitate the movement of the spindle in the transverse and radial axes and must be able to withstand the load pressure, temperature and high rotational speed of the machine tool spindle.

Types of machine tool spindle bearings
There are five main types of bearings used in machine tool spindles. Each type has its own advantages and disadvantages. It is important to understand how they work and the differences between them so that you can choose the most suitable one.
The contact angle between the balls of angular contact bearings and the inner and outer raceways enables them to support axial loads in one direction and a certain amount of radial loads at the same time. Therefore, they are widely used in high-speed precision applications where accuracy and stiffness are critical, such as machine tool spindles. Aubearing offers angular contact spindle bearings in sizes from 6 to 360 mm, with multiple options in materials, configurations, and to meet the needs of specific applications. Advantages of angular contact bearings:

Very suitable for high-speed operation and low friction;
Compact structure, ideal for machines with limited space requirements.
No adjustment required to obtain correct internal clearance or preload.
The lower shoulder allows a large number of balls to be accommodated in the bearing, resulting in a relatively high load-bearing capacity
Excellent rigidity to minimize deflection during processing, thereby improving accuracy;
Cylindrical roller bearings enhance motion by using cylinders instead of balls. Cylindrical roller bearings are primarily designed to carry radial loads. Cylindrical roller bearings consist of an inner ring and an outer ring, and the cylindrical rollers are fixed by a cage. These bearings provide a larger contact surface area for effective load distribution. Cylindrical roller bearings are suitable for medium to high speed applications. Cylindrical roller bearings are available in many designs, different series and various sizes. Features and benefits of using cylindrical roller bearings for machine tool spindles:

High Radial Load Capacity: Cylindrical roller bearings excel in applications requiring substantial radial load capacity, making them suitable for heavy-duty machining operations.
Low Friction: These bearings exhibit low friction during operation, thereby increasing efficiency and reducing heat generation
Suitable for high-speed applications: With proper design and lubrication, cylindrical roller bearings can achieve high-speed capabilities
Longer service life than ball bearings of the same size
Tapered roller bearings are designed to carry compound loads acting simultaneously. Composite loads include radial and axial forces. The projected lines of the raceways intersect at a common point on the bearing axis, thus providing true rolling action. Tapered roller bearings are designed in a way to provide low friction torque during operation. The axial load carrying capacity of tapered roller bearings increases with increasing contact angle. The contact angle of tapered roller bearings typically ranges from 10° to 30°. Single row tapered roller bearings usually correspond to a second tapered roller bearing. By applying preload, rigid bearing applications can be achieved. Advantages of tapered roller bearings:

Tapered roller bearings are capable of carrying both radial and axial loads, making them suitable for a variety of machine tool applications.
These bearings offer excellent rigidity and stability, ensuring precise machining performance.
Tapered roller bearings are known for their excellent performance in demanding applications
Hybrid ceramic ball bearings consist of AISI 52100 steel rings and silicon nitride (ceramic) balls. Hybrid ceramic bearings are an excellent electrical insulator, have extremely high speed capabilities, and last longer than standard radial or deep groove ball bearings. Harder ceramic balls have a higher surface roughness without removing material from the raceway. Lighter weight ceramic balls reduce the risk of false Brinell damage. Because ceramic balls are 40% less dense than steel balls, they produce smaller centrifugal loads and lower internal friction in the bearings. Bearings run much cooler during operation due to lower density and friction. The initial cost of hybrid bearings may be higher than standard steel bearings, but the difference is quickly made up through maintenance savings. Due to the properties of ceramic, hybrid bearings may last up to 10 times longer than standard steel bearings.

Hybrid bearings provide superior high-speed performance, reduce heat generation during operation and speed up machining processes
Ceramic materials enhance the bearing’s resistance to corrosion and wear, extending service
bearings provide lower friction, helping to improve efficiency and overall machine performance
Their unique properties make them best suited for specific applications requiring high-speed performance and corrosion resistance.
Factors to Consider When Selecting Spindle Bearings
During the CNC machining process, the spindle bearing will be affected by many factors. Every CNC machining job is unique, but the physics are constant. Having a clear understanding of these factors will help you make better decisions that will take your machining skills to new heights.
CNC machine tool requirements
The first step in the spindle bearing selection process is to clarify the operating requirements of the CNC machine tool. This involves understanding factors such as load type (radial, axial or combined), operating speed, temperature and environmental conditions. The nature of the application will influence the selection of various bearing types, including deep groove ball bearings, cylindrical roller bearings, angular contact bearings, etc.
Load capacity and speed requirements
Load capacity is the primary consideration in bearing selection because it directly determines the bearing’s ability to support applied loads without premature failure. Engineers need to evaluate the static and dynamic load capabilities of the bearing to determine the maximum load the bearing may encounter during operation.
Dynamic load rating (C) is a key specification provided by bearing manufacturers and represents the load at which 90% of a set of identical bearings can operate without fatigue failure after one million revolutions. By calculating the equivalent dynamic bearing load (P), which takes into account various load components such as radial and axial loads, engineers can evaluate how the bearing will perform under real-world conditions.
Operating speed is equally important, as too high an RPM can cause serious problems such as overheating and increased wear rates. The bearing’s speed limit (n_limit) defines the maximum speed that the bearing can withstand without adverse effects. Engineers must ensure that the bearing’s dynamic load rating and speed limit meet the specific requirements of the application to avoid premature failure and ensure optimal performance.
Rigidity and precision
Rigidity is critical for high-speed machine tool spindles because precise positioning and minimal deflection are critical to manufacturing precision parts. Highly rigid bearings ensure that shafts and components remain in their intended position, ensuring accuracy and repeatability.
The two basic measures of stiffness are axial stiffness (K_a) and radial stiffness (K_r). Axial stiffness reflects the bearing’s resistance to axial deflection when subjected to axial load, while radial stiffness indicates the bearing’s resistance to radial deflection when subjected to radial load. Bearings with higher stiffness values are suitable for applications requiring precise positioning, such as CNC machines, robots and medical inspection equipment.
In precision engineering, low runout and axial runout are critical to minimizing eccentricity during rotation. Bearings with tight dimensional tolerances, such as those meeting ABEC 7 or higher standards, ensure low runout and axial runout values, helping to improve the accuracy and smoother operation of high-performance machine tool spindles.
Spindle bearing life
Spindle bearing life is critical to predicting maintenance intervals and overall system reliability. Bearing rating life is defined as the number of revolutions or hours of operation before failure occurs in 90% of a group of identical bearings and can be calculated using industry standard formulas including ISO 281 and ASTM F2812. These calculations take into account factors such as load, speed, material, lubrication and operating conditions to estimate bearing service life.
Environmental conditions
Environmental factors have a significant impact on spindle bearing selection, as harsh conditions can lead to premature wear and failure. Factors such as humidity, dust, particles, corrosive chemicals, etc. can affect bearing performance and service life. To address these challenges, engineers may choose bearings with additional protection features: Sealed or shielded bearings provide effective defense against contaminants, preventing external particles from penetrating the bearing and reducing the opportunity for maintenance. For example, in corrosive environments, it is best to use bearings made of stainless steel, ceramic or other corrosion-resistant materials to mitigate the effects of chemicals.
Lubrication options
Proper bearing lubrication is the foundation for extended bearing life and optimal performance. The function of lubricants is to reduce friction, dissipate heat and prevent wear and corrosion. The choice of lubricant type (oil or grease) and properties (viscosity, additives, etc.) depends on factors such as speed, temperature, load and sealing mechanism. Industry standards such as ISO 281:2007 provide guidance on determining lubrication requirements based on operating conditions.
Conclusion
Machine tool spindles can only use high-quality precision bearings to produce precision parts. The selection of machine tool spindle bearings is crucial and must be accurate. Lack of lubrication, clearance, accuracy grade, contact angle and other details can lead to premature bearing failure. If you’re ready to take your machine tool spindle bearing performance even further, look no further than Aubearing. At Aubearing, we are committed to providing quality ball bearings, angular contact bearings, cylindrical roller bearings, tapered roller bearings and hybrid ceramic bearings. Aubearing is designed to deliver superior precision and performance, ensuring your machine is running at its best.