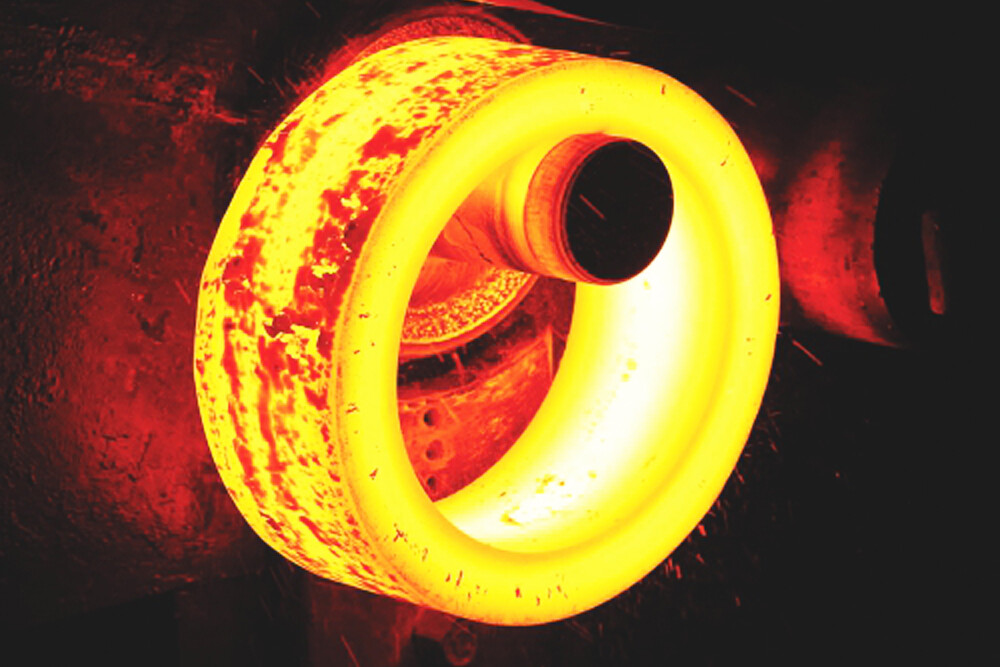
Bearing Manufacturer & Supplier
Specialize in ball bearings, roller bearings, thrust bearings, thin section bearings etc.
The Ultimate Guide to Bearing Making
Ball bearings are the most widely used bearings and play an important role in various mechanical movements. Ball bearings are used to support rotation, reduce friction, and support radial and axial loads in high-load, high-speed applications where reliability and efficiency are critical. Without ball bearings, many machines and equipment would not operate efficiently or safely. . So, you may be very interested in how ball bearings are made. At Aubearing, we specialize in manufacturing ball bearings to suit a variety of shapes, materials, sizes and other requirements. Based on many years of experience in manufacturing ball bearings, Aubearing has summarized the process guide for bearing manufacturing.
Table of Contents
ToggleWhat are ball bearings?

Ball bearings are composed of an inner ring, an outer ring, balls, a cage and a seal. The inner ring and outer ring are in contact with the shaft and the outer shell respectively. The balls separate the inner ring and the outer ring and reduce the friction of the rolling elements. The cage separates the balls and keeps them evenly spaced, preventing the balls from rubbing against each other, and the seals help prevent dust, debris, and other contaminants from entering the bearings, extending the life of the bearing system. Balls are the rolling elements that keep the bearing races separated. The balls roll along the raceways so that the machinery or equipment can rotate smoothly. Ball bearings are used in equipment such as pumps, office automation products, medical equipment, power tools, encoders, AC/DC motors, flow meters and measuring equipment.
There are many types of ball bearings. One is deep groove ball bearings, which are the most common type of ball bearings and are used in a wide range of applications that require high speeds and low friction. The second is angular contact ball bearings, which are designed to handle both radial and axial loads and are ideal for high-speed, high-precision applications such as machine tools, pumps and turbines. The third is thrust ball bearings, which are designed to handle axial loads in one direction and are often used in applications such as automotive transmissions and heavy machinery that require high axial load capabilities. The fourth is the self-aligning ball bearing, which is designed to compensate for the misalignment between the shaft and the housing. It is ideal for applications where shaft deflection, misalignment or installation errors may exist. The fifth is miniature bearings, used in small applications such as small motors and medical equipment. Sixth, flange ball bearings are used in applications where the bearing needs to be positioned in a specific position, such as on a shaft that needs to be fixed in place or on a support structure.
How to Make Ball Bearings
Ball bearings come in hundreds of sizes, from ultra-small 1.0 mm diameter bearings used in micro medical dental equipment and micro motors to large bearings over 17 feet in diameter used in heavy-duty equipment. How are ball bearings made? How to make ball balls so round? The answer is a multi-step manufacturing process, including machining, heat treatment, grinding, honing, assembly, quality control, etc. Although there may be differences, the following process is suitable for manufacturing the vast majority of today’s standard ball bearings.
Bearing manufacturers select suitable materials based on customer requirements. Depending on the application, materials such as steel, ceramic and stainless steel are available. Factors to consider include load capacity, rotational speed, operating temperature, corrosion resistance and cost. Each bearing material has unique advantages and disadvantages that play a decisive role in affecting the performance and life of a ball bearing in its intended application. Cage materials include stamped steel, stamped brass, machined steel, machined bronze, molded nylon or polyoxymethylene (POM) and phenolic resin.
Steel: The most widely used material for ball bearings is steel. Steel has excellent strength, hardness and wear resistance and can withstand tremendous pressure. Typically high carbon chromium steel (commonly known as bearing steel) is used. The specific steel grades used may include AISI 52100, AISI 440C or other similar alloys. These steels undergo a heat treatment process to achieve the required hardness and toughness. AISI 52100 is a chromium steel (1% carbon, 1.5% chromium alloy) that is dimensionally stable to 250 degrees Fahrenheit or higher, depending on the heat treatment process. AISI 52100 also offers excellent elasticity, processability and uniformity. Another popular material is AISI 440C stainless steel, which is used for its anti-corrosion properties. AISI 440C costs to machine than 52100 and cannot handle as much load. At 70 degrees Fahrenheit, the 440C has 85% of the load capacity of the 52100. Other martensitic stainless steels are also used to reduce bearing noise or increase fatigue life. AISI M50 steel is used in critical system applications such as the aerospace industry. Other alloys include M50. M50 is twice as reliable as 52100 and contains 4% molybdenum for added strength. The main trade-off is cost, as the M50 is roughly ten times expensive than the 52100.

Ceramic: Ceramic ball bearings offer several advantages over steel bearings. They are usually made from materials such as silicon nitride (Si3N4) or zirconium oxide (ZrO2), silicon carbide. Ceramic ball bearings offer excellent corrosion resistance, are lighter, have a lower coefficient of friction, are electrically insulating, and can operate at higher temperatures. They are typically used in applications requiring high speeds, extreme temperatures, or resistance to harsh environments. The price of ceramic ball bearings is usually much expensive than AISI 52100 and AISI 440C. The most common ceramic bearings are hybrid ceramic bearings, with the inner and outer rings made of stainless steel and the balls made of ceramic.

Stainless steel: The biggest advantage of stainless steel ball bearings is corrosion resistance. The most common stainless steel alloy bearings, such as AISI 304 or AISI 316, contain high concentrations of chromium and nickel. Stainless steel bearings are commonly used in industries such as food processing, medical equipment and marine applications.

Plastic: It sounds weird, yes, the material of ball bearings can also be plastic. Plastic ball bearings are mainly used in low-load, lightweight and non-precision applications, such as children’s toys. Since the manufacturing process of plastic bearings is different from that of metal bearings, the manufacturing process of plastic bearings will not be discussed in this blog.

Making bearing inner and outer rings
The manufacturing process of the inner and outer rings of the bearing is the same because they are both metal rings, but they are different in size. The ring starts out as tubing, utilizing an automated machine similar to a CNC lathe, whose cutting tools cut the metal tube into its basic shape, leaving a small amount of extra material to account for warping during the next step of heat treatment. Typically, the bearing number and manufacturer information are printed on the outer ring.
Next, the metal ring is hardened in a heat-treating furnace, heating it to about 1,550 degrees Fahrenheit (840 degrees Celsius) for anywhere from 20 minutes to several hours, depending on the size of the ring. They are then cooled in oil and tempered and air-cooled in a second furnace at around 300 degrees Fahrenheit (148 degrees Celsius) to further strengthen their toughness. This process makes the raceway both strong and durable.

The inner and outer rings are ground for precise dimensions and smooth surfaces. The raceway requires grinding wheel finishing, which cannot be done with a cutting tool because the raceway is now too hard. Each section of the ring must be ground to ensure proper bearing width, radius, raceway location and geometry. Some bearings, such as angular contact bearings, require additional grinding in a subsequent process to ensure close tolerances on ring dimensions.
Making bearing balls
Balls are very important for bearings. The round and smooth ball can minimize the friction inside the bearing. The ball’s initial state is a steel wire or rod-shaped block that is “cold headed” through a very special and thorough manufacturing process. Cold heading means cutting the wire and striking it at both ends to form a rough ball. There is a ring (also called a burr) around the ball. Next, turn the rough ball over to remove the “burr edges.” The ball is repeatedly fed into a groove between two cast iron disks, one of which rotates and the other is stationary. The rough grooves effectively tear off the burrs, leaving the ball fairly rounded and slightly larger than the actual application size for the next step of grinding. Of course, the balls undergo a similar heat treatment (heating and tempering) as the raceways to increase durability, toughness and hardness. Finally, the balls are moved to a grinder to achieve the proper size and roundness. The ball is polished with a grinder or polishing paste can be used to make the surface perfectly smooth. The balls stay in the grinder for 8-10 hours to create perfectly smooth balls.

Ball bearing cages are usually made of steel and are made from thin sheet metal. The final shape of the cage is formed in the mold. The mold consists of two pieces of steel that fit together and will be bent into the correct shape when the cage is placed into the mold and the mold is closed. Sometimes, the cage material of the bearing can also be plastic, because they are cheaper to manufacture, and some people think that plastic cages have a lower coefficient of friction than steel cages. If a plastic cage is to be made, an injection molding process is used, in which a mold is filled with molten plastic and then allowed to solidify until hard. The finished plastic cage is then removed and assembled with the other parts of the bearing.

Assembling bearings
Now that the four components of the bearing have been produced, the bearing is finally assembled. The inner ring sits inside the outer ring and is pushed to one side as far as possible to leave space between them for the balls. Carefully place the correct number of balls into the cage according to size. The cage separates the balls from each other and then presses the cage and the inner and outer rings together. If it is a steel cage, it must be installed and riveted together. To ensure that the bearings can handle higher loads, the cage and rings need to be heated to a specific temperature and held in place until the entire assembly cools. Plastic cages usually “snap in” easily. In most cases, an anti-rust formula is applied around the bearing and then shipped to the customer’s address.

The final step in the bearing manufacturing process is quality control. This involves testing ball bearings for accuracy, noise, vibration and other factors. Ball bearings undergo rigorous testing and quality control procedures to ensure their reliability and durability.
Clean bearing surface dirt: Use a recognized solvent to remove any dirt, debris and rust from the bearing.
Inspection: Visually inspect the bearing for any visible defects and use magnetic particles to inspect the bearing for cracks, worn or irregular surfaces and other problems.
Dimensional measurement: Use special bearing testing instruments or three-dimensional coordinate measuring instruments to measure key dimensions such as inner and outer diameters, steel ball sizes, and widths.
Roundness and vibration measurement: Evaluate the roundness of bearing components and measure any runout or deviation from the ideal circular shape.
Surface roughness analysis: Evaluates the smoothness or roughness of a bearing surface.
Packaging: Apply the correct lubricant to the bearing based on the type of bearing. Finally, it is placed in a vibrating drum for thorough cleaning and sealed into a bearing package.
Due to the precision of the bearings, Aubearing will conduct rigorous testing throughout the process to ensure the highest quality of the finished product. We will conduct testing throughout the entire process to check for defects, as well as regular testing during the heat treatment process. Size and shape are also crucial, and the surfaces of the balls and raceways must be as smooth as possible.
Conclusion
This guide outlines the entire bearing manufacturing process from materials to quality control systems, giving engineers interested in the process a comprehensive understanding of the steps required to create high-quality bearings. The manufacture of ball bearings is a complex process that requires precision and attention to detail. With the continuous advancement of bearing technology and the accumulation of bearing knowledge, manufacturers can confidently produce high-quality bearings that meet customer needs.