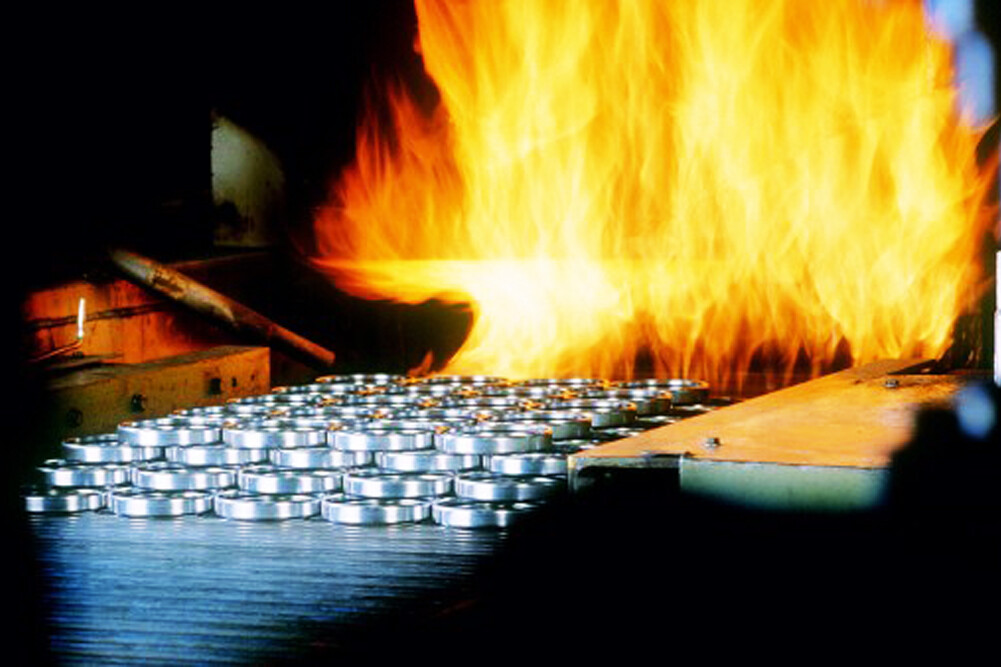
Bearing Manufacturer & Supplier
Specialize in ball bearings, roller bearings, thrust bearings, thin section bearings etc.
Improvement of heat treatment process for thin-section bearings
Aiming at the problem of deformation of thin-section bearing rings with larger outer diameters after conventional heat treatment processes, Aubearing improved the heat treatment process through experimental analysis. By lowering the quenching temperature, selecting appropriate heating time, increasing the quenching oil temperature, and reducing the oil stirring speed (or even no stirring), the probability of deformation of thin-section bearing rings can be effectively reduced.
Table of Contents
ToggleCauses of deformation of thin-section bearing rings
One of the main reasons for the deformation of bearing rings is the thermal stress and large organizational stress caused by uneven thermal expansion and contraction between the surface and interior of the ring and different internal structural transformations during the heat treatment heating and cooling process. When the ferrule undergoes overall plastic deformation, the deformation manifests itself as expansion or contraction in the diameter direction; when local plastic deformation occurs, it manifests as an increase in roundness or cylindricity errors. Since the cooling rate of quenching oil is fast, far exceeding the heating rate of the ferrule in the heating furnace, and the thin-walled ferrule has poor stiffness, most of the deformed ferrules are produced during the cooling process.

There are many factors that affect the heat treatment deformation of bearing rings. Any method that can reduce the thermal stress and internal structural stress generated during the heat treatment process can reduce the deformation of thin-section bearing rings. From the perspective of heat treatment process, by lowering the quenching temperature, appropriately controlling the holding time, increasing the quenching oil temperature, and reducing the stirring speed of the quenching oil, the deformation of the ferrule can be effectively reduced. Therefore, to control its deformation, an appropriate heat treatment process must be developed to control thermal stress and tissue stress.
Original heat treatment process
Taking the 6014-2RLD outer ring as an example, the material is GCr15; the heat treatment equipment is a roller mesh belt heat treatment production line with an endothermic protective atmosphere; the quenching oil is 1# isothermal graded quenching oil, and the normal operating temperature is 80 to 120°C. The original heat treatment process is: quenching temperature 855 ℃, heating time 30 min; quenching oil temperature 100 ℃, a set of rings is added with appropriate stress relief annealing after CNC turning; during the quenching stage, the quenching heating temperature is appropriately controlled, and the quenching cooling is reasonably controlled. Speed; blocking the oil ditch with water glass, asbestos rope or refractory soil before quenching and heating; using protective atmosphere heating, etc. can reduce the occurrence of oil ditch cracks.
Improving the structure or shape of the oil groove to avoid the effects of straight oil grooves and sharp corners will also play a positive role in controlling the occurrence of oil groove cracks. In recent years, Aubearing has produced approximately 3,000 extra-large GCr15SiMn steel ferrules that have been produced and verified based on the above-mentioned annealing and quenching processes. After quenching and tempering, they were sandblasted and inspected. No oil groove cracks were found, and all were qualified, which is also proved Proper heat treatment process can effectively avoid the occurrence of oil groove quenching cracks.

One circulating oil pump and one cooling oil pump are running normally; the tempering temperature is 180°C and the tempering time is 3 hours. After heat treatment according to this process, the roundness error of the ferrules is large, and than 50% of the rings have VD sp exceeding 0. 20 mm, so the workload of sorting and correction is huge.
Heat treatment process improvement
Analysis and conclusion of factors such as heating temperature, heating time, cooling oil temperature, cooling oil stirring speed that affect heat treatment deformation, and heat treatment process testing.
Test 1: Keep the cooling parameters unchanged and change the heating parameters.
That is, the quenching temperature is modified to 820 °C, the heating time is 40 min, and other process parameters remain unchanged. After the test, only 48% of the outer rings have VD sp ≤0. 2 mm.
Test 2: Keep the heating parameters unchanged and change the cooling parameters.
That is, the quenching oil temperature is changed to 120°C, and the circulating oil pump and cooling oil pump are shut down, while other process parameters remain unchanged. After the test, the outer ring with VD sp ≤0. 2mm accounts for 62%.
Test 3: Heating parameters and cooling parameters were changed simultaneously.
That is, the quenching temperature is modified to 820°C, the heating time is 40 min, the quenching oil temperature is 120°C, and the circulating oil pump and cooling oil pump are shut down, and the tempering process remains unchanged. After the test, the outer ring with VD sp ≤0. 2 mm reached than 70%.
It can be seen from the above three tests: Test 1 only slightly improved the deformation of the ferrule, and the effect was not significant; Test 2 significantly improved the deformation of the ferrule; Test 3 had the best effect on improving the deformation of the ferrule.
Therefore, the new heat treatment process was determined as follows: quenching temperature 820°C, heating time 40 min, quenching oil temperature 120°C, shut down the circulating oil pump and cooling oil pump, oil-free stirring; tempering temperature 180°C, tempering time 3 h . The structure and hardness obtained by the new heat treatment process meet the requirements of JB/T 1255-2001 “Technical Conditions for Heat Treatment of High Carbon Chromium Bearing Steel Rolling Bearing Parts”. Randomly sample 100 pieces from each of the new and original heat treatment ferrules, and measure VD sp. The results are shown in Table 1 .
Comparison of improved and original processes | VD sp /mm |
Total | |||||||
< 0. 10 | 0. 10 ~ 0. 15 | 0. 15 ~ 0. 20 | 0. 20 ~ 0. 25 | 0. 25 ~ 0. 30 | 0. 30 ~ 0. 35 | > 0. 35 | |||
original processes | Piece | 8 | 15 | 22 | 28 | 17 | 7 | 3 | 100 |
Percent /﹪ | 8 | 15 | 22 | 28 | 17 | 7 | 3 | 100 | |
improved process | Piece | 15 | 24 | 35 | 16 | 8 | 2 | 0 | 100 |
Percent /﹪ | 15 | 24 | 35 | 16 | 8 | 2 | 0 | 100 |
It can be seen that after the outer ring of 6014-2RLD is processed according to the original process, only 45% of the outer ring with VD sp ≤0. 2 mm and 73% of the outer ring with VD sp ≤0. 25mm are processed according to the new process. The outer ring with VD sp ≤0. 2 mm has 74%, and the outer ring with VD sp ≤0. 25 mm has 90%. Therefore, the new heat treatment process can indeed reduce the deformation of the ferrule.
In addition, the quenching temperature is used for another thin-walled bearing 6214-2RLD with a larger outer diameter (outer diameter <125. 15 ± 0. 03 mm, inner diameter < 108 + 0. 120mm, width 24. 10 ± 0. 03 mm) 830 ℃, heating time 45 min, quenching oil temperature 120 ℃, shut down the circulating oil pump and cooling oil pump, no oil stirring; heat treatment process test with tempering temperature 180 ℃, tempering time 3 h, it was found that the deformation of the ferrule was also significantly reduced. Small.
Conclusion
For bearing rings with large outer diameters that are easily deformed, by lowering the quenching temperature (820~830°C), selecting an appropriate heating time, increasing the quenching oil temperature (120°C), and reducing the oil stirring speed (or even no stirring), it can Effectively reduce the heat treatment deformation of the ferrule.