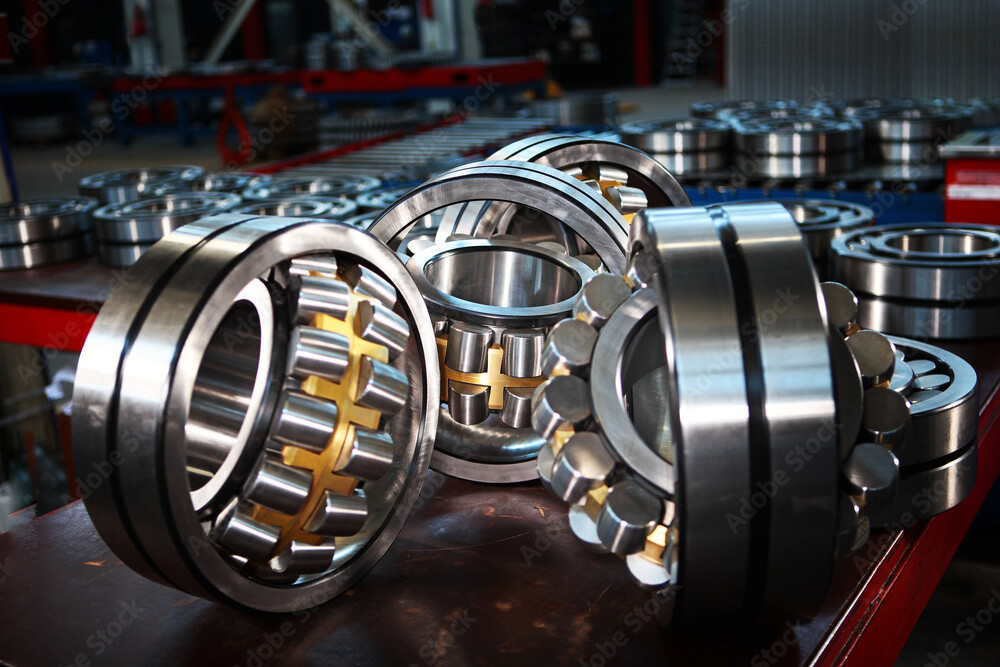
Bearing Manufacturer & Supplier
Specialize in ball bearings, roller bearings, thrust bearings, thin section bearings etc.
Everything you should know about spherical roller bearings
Bearings are an important part of industrial machinery. There are many types of bearings to choose from. According to incomplete statistics, there are than 400,000 types of bearings in the world. Each bearing has its own purpose and advantages and disadvantages.
Spherical roller bearings are designed to carry high loads, are suitable for radial and axial loads, and are self-aligning, making them one of the most popular bearings today. Among all rolling bearings, spherical roller bearings are suitable where high impact forces are present. In addition to shock loads, this type of bearing is also able to handle various misalignments and shaft deflections.
Spherical roller bearings are very strong because the load is evenly distributed on the rollers. Self-aligning roller bearings, often called anti-friction bearings, have a low coefficient of friction; the rollers are placed relatively loosely between the outer and inner rings, resulting in less friction and less heat; as a result, the life of the bearing The period will be extended.

AUS is committed to becoming a world-class manufacturer of ball bearings and roller bearings. Based on than 20 years of bearing manufacturing experience, some information about spherical roller bearings is summarized.
Table of Contents
ToggleWhat is a spherical roller bearing?
Spherical roller bearings provide the versatility of bi-directional motion. Its main function is to reduce friction between components while allowing for misalignment. There are two types of self-aligning roller bearings: unsealed/open bearings and sealed. Both types of bearings are designed to withstand high loads; however, sealed bearings benefit from a housing that helps extend their life. Efficient double lip seals keep lubricant out and contaminants out. Understanding both bearing types and which type is required for a particular application is critical when purchasing.

Several factors determine the effectiveness of spherical roller bearings in a particular application, including:
Minimum load, for high speed operation with stable acceleration and deceleration, the bearing must apply a minimum axial load to the rollers. This prevents damage to the cage due to inertial forces as well as sliding or excessive friction. The minimum load required can be lowered by using a good quality lubricant.
Operating temperature is the ambient temperature range in which the bearing operates most reliably. At low temperatures, the viscosity of the lubricating oil increases, thus requiring a higher minimum load. Spherical roller bearings operate at particularly high temperatures if the bearing material is subjected to a heat treatment process.
Reference speed is the rotational speed at which the heat generated by rotation equals the heat removed from the lubricant and bearing geometry.
Limiting speed is the highest speed at which the bearing is designed to operate. It depends on: the strength of the bearing cage, the quality of lubrication, centrifugal and rotary forces, the precision of bearing manufacturing and the characteristics of the lubricant.
Advantages of spherical roller bearings
Bearings reduce friction and allow for smoother rotation.
It allows angular misalignment. Spherical roller bearings are self-aligning and can therefore accommodate misalignment.
The bearing supports the rotating shaft in the bore of the inner ring.
Due to the many spherical rollers, these bearings have excellent radial load and unidirectional combined load carrying capacity.
Spherical roller bearings are capable of medium and high speeds.
Spherical roller bearings reduce maintenance requirements.
Known for extended life.
Reduced noise and vibration levels.
Spherical roller bearings are often used in demanding applications in harsh environments, especially where housing alignment is difficult to establish or some shaft misalignment is expected. Spherical roller bearings can remain effective at temperatures up to 500°F if the rollers and raceways are dimensionally stabilized and heat treated. Bearings can be manufactured with ultra-precise running accuracy and tighter bore and diameter tolerances for vibration and shock loaded applications.
Spherical Bearing Design
Spherical bearings have two rows of rollers separated by a cage or rib and, depending on the size and application, can be sealed or unsealed. An outer ring raceway and an inner ring double raceway support the rotating shaft. The quality and alignment of the raceways, cages and rings determine the overall performance and quality of the product. Asymmetrical rollers increase performance and precision, while symmetrical rollers provide better load distribution and less vibration, ultimately increasing durability. All sizes and types of spherical roller bearings have a tapered bore and can be mounted using adapters, removable sleeves or directly on matching tapered shafts.
Spherical roller bearing material
Spherical roller bearings can be manufactured in a variety of materials depending on the application and operating environment. AISI 52100 chrome steel is one of the most commonly used materials in the production of these bearings due to its durability, but steel plate, polyamide and brass are also used in some applications. One of the most important parts of a spherical bearing is the cage that holds the bearing in place. This cage is usually made of pressed steel or brass because of the strength and temperature resistance of both materials.

Spherical bearings often have seals to keep out contaminants such as dirt, liquids, debris, and harsh temperatures. Bearings of this type do not even require lubrication if they do not exceed 50% of their maximum permissible rotational speed.
Commonly used types of spherical roller bearings
21300 Series – ISO Dimension Series 13 Spherical Roller Bearings
22200 Series – ISO Dimension Series 22 Spherical Roller Bearings
22300 Series – ISO Dimension Series 23 Spherical Roller Bearings
23000 Series – ISO Dimension Series 30 Spherical Roller Bearings
23100 Series – ISO Dimension Series 31 Spherical Roller Bearings
23200 Series – ISO Dimension Series 32 Spherical Roller Bearings
232/Series – Extra Large ISO 32 Series Spherical Roller Bearings
23900 Series – ISO Dimension Series 39 Spherical Roller Bearings
24000 Series – ISO Dimension Series 40 Spherical Roller Bearings
24100 Series – ISO Dimension Series 41 Spherical Roller Bearings
29000 Series – ISO Dimension Series 90 Spherical Thrust Roller Bearings
Service life of spherical roller bearings
Spherical roller bearing life is determined by the number of hours or revolutions before the bearing experiences mechanical fatigue. Before calculating the estimated life of a bearing, it is necessary to find the dynamic equivalent radial bearing load, which is a single value that takes into account both axial and radial stresses.
Dynamic Radial Bearing Loads:

Pr = dynamic equivalent radial load
Fr = applied radial load
Fa = applied axial load
X = dynamic radial load factor (supplied by bearing documentation)
Y = dynamic axial load factor (supplied by bearing documentation)
From this, an estimate of bearing lifespan can be identified.
n = bearing operating speed (RPM)
Spherical roller bearing lubrication
As with all bearings, spherical roller bearings need to be adequately lubricated. This can be done through grease or oil. Keep in mind that grease has a lower operational speed capacity than oil. Should an operation require very high speeds, oil is a better choice.
If grease is the preferred choice, choose a bearing that is well suited for the lubrication type. Often, manufacturers build a grease groove into the outer raceway to make for easy application of grease through grease nipples.
If oil is the preferred choice, this can be done through a sealed bearing with an oil reservoir or oil-bath lubrication. Keep in mind that with an oil bath, the lowest roller only should be in contact with the oil. This will allow for splash lubrication. If than the lowest roller is in contact with the oil, the bearing will need force to bring the rollers through the oil, losing its effectiveness and speed advantage.
Spherical roller bearing application
Spherical roller bearings are used for extremely harsh operating conditions in extremely demanding environments. These bearings are used in applications prone to misalignment or shaft deflection (bending of the shaft under certain conditions, such as axial loads). They are known to tolerate misalignment between the shaft and housing. Due to their ability to handle misalignment, spherical roller bearings are used in a variety of mechanical applications.
Applications for spherical roller bearings include vibrating screens, rolling mills, vibrating screens, conveyors, transmissions, heavy backup rolls, rock crushers, wind turbines, all types of mining and construction equipment, and material handling equipment.