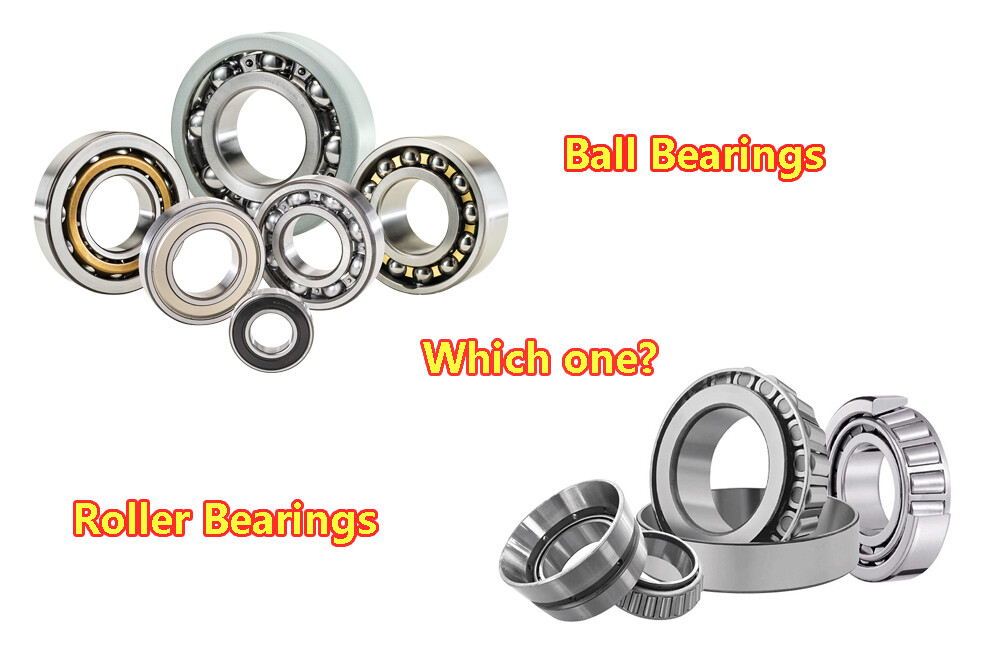
Bearing Manufacturer & Supplier
Specialize in ball bearings, roller bearings, thrust bearings, thin section bearings etc.
Ball Bearings vs Roller Bearings, Which one?
Bearings are critical components in nearly all machines, helping them run smoothly by reducing friction between moving parts. There are many types of bearings (legend has it that there are 470,000 types), each designed to handle different load conditions. This article focuses on the two main types: ball bearings and roller bearings. Based on many years of experience in manufacturing bearings, Aubearing explains their different designs and compares them, providing constructive advice on how to choose between them.
Both ball bearings and roller bearings are used in a variety of machines with rotating parts. Their properties often contribute significantly to technological and economic progress in different fields of engineering. The standardization of bearings makes it possible to select a design directly from the bearing table in the manufacturer’s bearing catalog. Bearing manufacturing companies such as SKF, NTN, Timken, FAG, Schaeffler, Aubearing, etc. are natural sources of selection information. Most of the time, a designer can select stock bearing products for his design directly from the catalog. Choosing a popular and widely used design helps achieve optimal usability and provides the most economical solution.

Table of Contents
ToggleBall Bearings
Industrial ball bearings are used in a variety of machinery and manufacturing equipment to achieve smooth, efficient rotational motion. The bearing itself consists of an outer ring, an inner ring, a set of steel balls, and a cage that keeps the balls evenly distributed. Both the outer and inner rings are typically made from extremely durable materials, such as steel or ceramic, and are designed to withstand high speeds and heavy loads. Steel balls within the bearing provide low-friction contact points between the inner and outer rings, allowing movement with minimal resistance and reducing energy lost to friction. The bearing’s cage serves to maintain the correct positioning of the balls, prevent them from contacting each other and ensure even distribution of load. Rolling motion is subject to axial and radial loads. Ball bearings are commonly used in high-speed applications such as electric motors and gearboxes. See our ball bearing overview article for information.

Ball Bearing Type
There are two basic types of ball bearings, single row or double row. The most popular are single row deep groove ball bearings, which consist of a row of balls traveling in a single groove path. Double row ball bearings consist of two rows of balls in two sets of grooved raceways. Both single-row and double-row ball bearings are composed of inner rings, outer rings, balls and cages. Both types of bearings can handle high radial and axial loads. Deep groove ball bearings are available in both low- and high-speed applications, depending on tolerance class, lubrication, internal clearance and the type of seal or guard selected. The following list outlines the various types of ball bearings, each with unique characteristics and specific uses. These bearings are critical in numerous applications including precision instruments, micromotors, gearboxes and wheel hubs.
Deep Groove Ball Bearings: Deep groove ball bearings are the most common type. They can withstand radial and axial loads.
Angular Contact Ball Bearings: Angular contact ball bearings have above average internal axial clearance. They can withstand axial loads in one direction and moderate radial loads.
Self-aligning ball bearings: Self-aligning ball bearings can adjust for alignment errors. They can withstand radial loads but can withstand minimal axial loads.
Thrust ball bearings: Thrust ball bearings are designed for high axial loads and negligible radial loads.
Miniature Ball Bearings: Miniature ball bearings are suitable for precision instrument applications where space is limited, such as micro motors.
Double row ball bearings: Double row ball bearings have two rows of balls and can withstand higher loads.
Advantages of Ball Bearings
Low coefficient of friction: The main advantage of having a large contact area is that the ball bearing experiences much less friction due to the movement of the inner and outer raceways. This means that the rotation of the part goes very smoothly. Likewise, we only need to look at a fidget spinner to understand how well ball bearings handle rotational motion. Therefore, ball bearings are the solution of choice in applications where speed and ease of operation are a priority.
Can withstand radial and thrust loads: Another unique feature of ball bearings is that they can rotate on multiple axes. This means that they react not only to radial loads, but also to thrust loads. How a ball bearing rotates depends on the angle of the thrust load. The versatility of ball bearings makes them an excellent choice for equipment that is not used to strict standards, such as toys or other items around the house.
Compact design: They require less space and can be used in smaller establishments.
Versatility: Suitable for radial and axial (thrust) loads.
Low maintenance: They have a long service life in applications with low axial loads and require less maintenance.
Disadvantages of ball bearings
Inability to support heavy weight: Although ball bearings have a smaller contact area with the load, meaning they experience much less stress, this also means the load becomes concentrated. In extreme cases, this can cause the ball bearings to deform, a precursor to complete failure. Therefore, ball bearings are usually only used in applications with smaller loads. For industrial grade equipment, roller bearings are preferred. A type of ball bearing, called a full complement ball bearing, fills the space between the inner and outer raceways with as many balls as possible. This type of bearing can handle higher loads by distributing the load over balls. However, full complement ball bearings are also susceptible to wear due to frequent contact between adjacent balls.
Durability: May deform under excessive loads, resulting in shortened bearing life.
Sensitivity: susceptible to misalignment and shock loads.
Roller bearings have cylindrical or conical rolling elements. This bearing type is designed to carry heavy radial loads due to the larger contact area between rollers and raceways.
Roller Bearing Type
The following list outlines the various roller bearing types with different characteristics and specific applications. These bearings play a vital role in various scenarios such as vehicle wheels, heavy machinery, and applications requiring high load-bearing capacity. Read our roller bearing overview article to learn .

Cylindrical Roller Bearings: Cylindrical roller bearings have cylindrical rollers that are uniformly sized along their length. These bearings are suitable for carrying heavy radial loads and can operate at high speeds. Cylindrical roller bearings are guided between flanges on the inner or outer ring. Even when the free rings are removed, they are held together with the guide rings by the cage. In the most common type of cylindrical roller bearing, the free ring has no flange, so that within certain limits the bearing rings can be displaced axially relative to each other. If the bearing is rotating, this displacement will occur without resistance, provided the rate of displacement is relatively slow (e.g. displacement due to thermal expansion of the shaft). The low friction of cylindrical roller bearings makes them suitable for relatively high speeds, and they are often used in conjunction with high-speed angular contact ball bearings in high-speed machine spindles.

Tapered Roller Bearings: Tapered roller bearings feature tapered rollers and raceways, making them ideal for vehicle hubs and other high-load applications. Tapered roller bearings are the most widely used roller bearings. They can withstand large axial and radial forces. Tapered roller bearings consist of an outer ring and an inner ring, while ball bearings consist of an outer ring and an inner ring. Tapered rollers can be assembled into cartridges, but in their simplest form they are two separate components, while ball bearings can be separable, which is usually a self-contained unit.

Tapered roller bearings use straight tapered rollers whose end faces are in contact with the guide flange on the inner ring. The roller taper and the inner ring roller path have a common vertex on the bearing axis. The outer ring is designed with a slightly curved roller path generatrix to prevent edge loading of the rollers. Although the closeness between the rollers and the outer ring is reduced, the strain of the outer ring is smaller than that of the inner ring. The guide flange of the inner ring has a spherical surface against which the ball ends of the rollers press. As with spherical bearings, pressure on the flange effectively guides the rollers. Some manufacturers such as Timken, FAG, NTN and SKF make the roller end faces flat and the flange guide faces conical. The roller ends then contact the roller flange at only two points.
Because tapered roller bearings are separable, they are usually mounted opposite each other so that one bearing can adjust to the other. After adjustment, a certain very small gap will always be left in the bearing. Temperature changes in the shaft affect this adjustment and thus the bearing clearance. Therefore, single row tapered roller bearings are usually used only when the distance is short. Tapered roller bearings have high radial load carrying capacity as well as axial load carrying capacity in one direction. Thrust capability depends on the angle of the rollers. As a measure of this angle (contact angle), it is typically 12 to 16 degrees. Some heavy-duty tapered roller bearings have contact angles of 28-30 degrees.
In many applications, tapered roller bearings are used in back-to-back pairs to support axial forces equally in either direction. Tapered roller bearings are widely used in automotive wheel bearings to carry radial and axial loads. Tapered roller bearings are commonly used in heavy-duty applications. Many different industries including agricultural, construction and mining equipment, axle systems, gearboxes, engine motors and gear reducers, driveshafts, railway axleboxes, differentials, wind turbines and all types of trailers.
Spherical roller bearings: Spherical roller bearings have an automatic self-aligning function and can withstand heavy radial loads and axial loads. They are ideal for applications involving misalignment or shaft deflection.
Needle roller bearings: Needle roller bearings have thin, long rollers and are suitable for applications where radial space is limited but load-carrying capacity is required.
Thrust roller bearings: Thrust roller bearings can withstand large axial loads and are often used in heavy machinery such as drilling rigs and extruders.
Advantages of roller bearings
Bear large loads: The large contact area provided by roller bearings allows them to withstand larger loads without deformation or failure. This makes roller bearings an excellent choice for industrial equipment designed to carry heavy loads or other applications where there is little room for failure.
Variant Designs: Contrary to ball bearings, the geometry of the rollers can vary for different types of operation. Standard cylindrical rollers are designed for purely radial loads, providing greater load capacity at the expense of the ability to handle any thrust loads.
Needle roller bearings are a slight variation of cylindrical rollers with a much smaller diameter. It is used in applications where radial space is small. Needle rollers also provide a large amount of contact area, but generate a lot of friction and vibration because they rotate so fast. Therefore, it can only be used in equipment that operates at low speeds and can withstand large amounts of vibration.
Tapered roller bearings are tapered at one end rather than being a straight cylinder throughout. This allows the roller bearings to withstand limited thrust loads. The ratio of radial load to thrust load that a tapered roller can bear is determined by the angle of the roller. Up to 30 degrees is acceptable, but most tapered rollers have angles between 10 and 16 degrees.

Durability: Sturdy and durable, it can withstand heavier loads without deformation.
Less Sensitive: resistant to shock loads and misalignment than ball bearings.
Disadvantages of roller bearings
Limited Ability to Handle Thrust Loads: Although there is an option to use tapered versions, the fact remains that roller bearings are not primarily designed for thrust loads. Therefore, the movement allowed by roller bearings is restricted. This reduces the versatility of roller bearings, which explains why they are less visible in domestic environments.
prone to misalignment: Bearings of any type, whether ball or roller, have a small amount of play between the bearing elements and the raceways. This internal clearance allows the bearing elements to move smoothly along the raceway. However, this also makes it possible for the bearing elements to deviate from their original position. Ball bearings are tolerant of angular misalignment. This is especially true for roller bearings. While ball bearings can handle misalignment up to 0.004 inches, cylindrical roller bearings may already have difficulty rotating when misalignment exceeds 0.001 inches. This means roller bearings need to be designed with greater precision, making them difficult and expensive to manufacture.
Size: Typically larger and require mechanical space.
Maintenance: frequent maintenance may be required, especially in high-speed applications due to increased friction.
The difference between ball bearings vs roller bearings
Both ball bearings and roller bearings are designed to reduce rotational friction while supporting radial and axial loads. The basic difference between roller bearings and ball bearings lies in their basic design. The main difference between roller bearings and ball bearings is that the rolling element is a roller or a ball. When comparing ball bearings and roller bearings, several factors come into play.
Due to their lower coefficient of friction, ball bearings are generally suitable for applications requiring high speed operation.
Roller bearings have a large contact area and are ideal for heavy radial load applications.
Due to the smaller contact area, the load capacity of ball bearings is lower than that of roller bearings.
Ball bearings deform less under load, making them suitable for precision applications.
Selection Criteria
Selecting the correct bearing for a specific application is critical for optimal performance and service life. The selection criteria are mainly based on the following two criteria:
Load type and capacity: Bearings must be able to withstand specific loads, whether radial, axial or a combination of loads. Roller bearings are typically used for heavy radial loads, while ball bearings are used for lighter loads.
Speed Requirement: The running speed of the application plays an important role. Ball bearings are the first choice for high-speed applications due to their low frictional resistance.Ball bearings are generally better suited for applications that may require high speed rotation. They have a lower coefficient of friction during startup and operation, which means they can reach higher speeds with less resistance.
Roller bearings, on the other hand, are better suited for applications requiring higher load capacities. This is because line contact (as opposed to point contact in ball bearings) allows the load on the bearing to be distributed widely. In terms of efficiency, ball bearings tend to have a slight advantage in minimizing friction at high speeds. However, due to their design, roller bearings can handle larger loads efficiently.
Conclusion
Bearings have been used for decades and are undoubtedly one of the most important engineering components in industrial, commercial and domestic environments. They provide smooth and consistent rotational motion and prevent wear caused by friction. Ball bearings and various types of roller bearings are all that anyone needs to provide a removable connection between components that need to rotate along any axis.