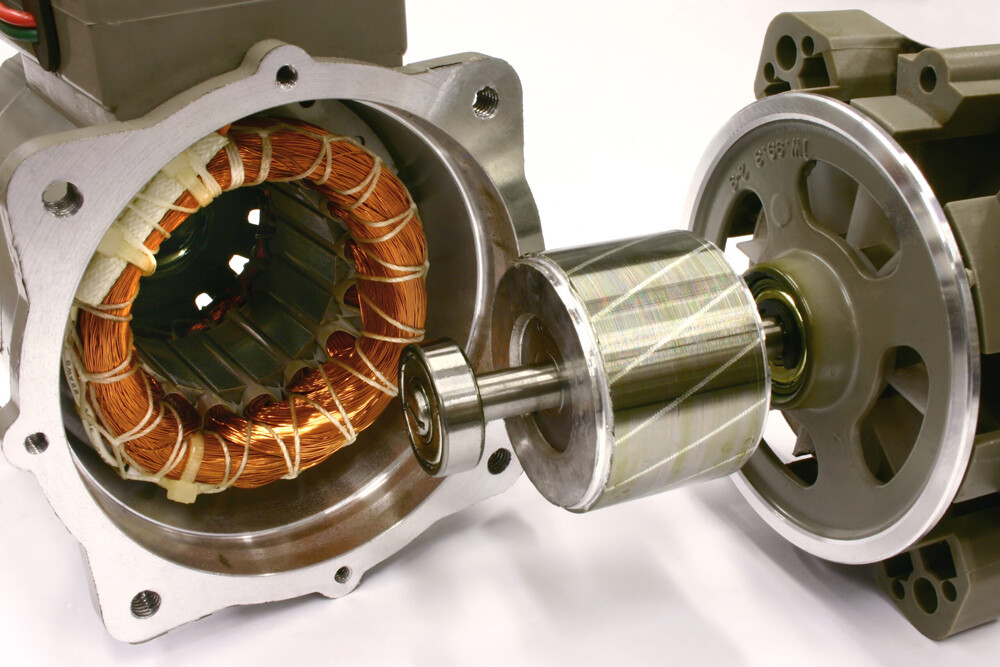
Bearing Manufacturer & Supplier
Specialize in ball bearings, roller bearings, thrust bearings, thin section bearings etc.
A Guide to Selecting Motor Bearings
As one of the core components of electric motors, motor bearings have always been an important issue in the field of motor manufacturing. The selection of appropriate bearings is directly related to several aspects such as the operating stability, service life and maintenance cost of the motor. Therefore, when manufacturing a motor, one must make a choice from numerous bearing models based on actual working conditions and performance requirements. Motor bearings are designed to continuously transfer load from the shaft to the motor and support the rotor. Failure of these bearings often results in expensive motor repairs. There is no universal “one size fits all” anti-friction bearing solution for electric motors. Each bearing type has specific performance characteristics and is therefore suitable for specific operating conditions. A mismatch between bearings and motor applications can cause serious problems. This blog reviews the design, type, considerations, etc. of selecting motor bearings, and provides constructive suggestions for you to choose a suitable motor.
Table of Contents
ToggleSelecting the wrong motor bearing example
Motors with a power greater than 125 hp, speeds exceeding 1,200 rpm and equipped with deep-groove ball bearings designed for direct belt connection tasks can lead to mechanical overloading and premature failure.
Placing a motor designed for heavy-duty belts on a coupled load may not provide sufficient radial load on the rolling elements of the bearing. They can slide or slip on the raceways, causing high temperatures and possibly complete failure of the lubrication.
If the roller bearings are underloaded (even with belt loading), premature motor failure can occur due to the same slipping phenomenon.
Mounting motors with horizontal bearings in vertical applications adds unintended additional axial loads and can cause grease loss in the bearings.
If stray current flow through the bearings (often encountered in large variable speed motors) is not addressed, galvanic corrosion damage can result, leading to premature bearing failure.
Motor bearing design
Rolling bearings (balls and rollers) in electric motors are used to support and position the rotor, keep the air gap small and consistent, and transfer load from the shaft to the motor frame. Bearings should support high- and low-speed operation, minimize friction, reduce noise, extend service life and save power. Because the design and use of electric motors vary among different industries, there are many types of bearings used to support them. Bearing types suitable for electric motors include deep groove ball bearings, angular contact ball bearings, cylindrical roller bearings, tapered roller bearings, spherical roller bearings, and spherical roller thrust bearings. Each bearing has its own configuration and performance characteristics. Electric motors typically contain locating and non-locating bearing arrangements to radially support the rotor and to axially position the rotor relative to the stator. Locating bearings position the shaft and support axial loads, whereas non-locating bearings allow the shaft to move axially and compensate for overload conditions when the shaft thermally expands.
Ball bearings are commonly used in non-belt applications in motors up to 150 horsepower. They can withstand radial and axial loads. For small motors used in horizontal machinery, the most common are two deep groove ball bearings mounted on a stub shaft in a cross-located bearing configuration to control the movement of the shaft. In most medium and large electric motors used in horizontal machines, deep groove ball bearings are used as locating bearings, while the non-locating bearings may be cylindrical roller bearings, depending on the load, speed, temperature and environment of the application. Non-locating bearings accommodate any axial expansion caused by heat or machine tolerances.

Angular contact ball bearings are designed to withstand high axial loads and allow smooth operation at high speeds within electric motors. They can be configured as single or double rows and used in a number of different cage designs. Vertical machines typically rely on deep groove ball bearings or angular contact ball bearings or spherical roller thrust bearings, depending on vertical loads, shaft and rotor weight, speed, temperature and operating environment.

Cylindrical roller bearings are exactly what motors need when handling extremely high axial loads. They operate efficiently at both medium and high speeds and come in a variety of different design configurations. They are most often used in belt or gear driven electric motors.

Sealed bearings
Sealed bearings are a bearing design commonly used in small motors that are designed to limit the bearing’s exposure to contamination. These bearings cannot be lubricated with new grease once installed. This means they have a limited lifespan and should be carefully monitored so that they can be replaced immediately if problems arise.
Shielded bearings
Shielded bearings are another bearing design used to limit contamination of rolling elements from installation to motor operation. These bearings can be re-lubricated with filled grease, but if the internal pressure is not relieved, it can cause the shield to press against the cage or rolling elements, causing big problems.
One of the factors you must always keep in mind when selecting motor bearings is which type of bearing design is best for the motor you are using for the job. If you are unsure which bearing design is best for your work environment, contact a motor bearing expert to determine which bearing setup and motor is best for you.
Effect of loading
The nature of the load is one of the main factors in bearing selection. Bearings always require a given minimum load to allow the rolling elements to rotate properly and form a better lubricating film in the rolling contact area. Otherwise, slippage may occur, resulting in higher operating temperatures and lubricant degradation. Of course, the bearing must provide sufficient load capacity to achieve a satisfactory service life in the application. All loads must be considered – not just the weight involved and the forces generated by the transmitted power, but also coupling loads and belt loads connected to the drive load. For coupled loads, the motor shaft is usually connected to the shaft driving the load via a flexible coupling. This type of load creates no axial or radial loads on the motor bearings, other than the weight of the motor rotor and shaft assembly. (However, misalignment caused by incorrect installation can increase radial loads.)

Generally speaking, roller bearings can handle heavy loads and ball bearings can handle light loads. Loads can be radial loads, axial loads, or a combination of both. Some bearings, such as cylindrical roller bearings, are generally designed to carry radial loads only; other bearings, such as angular contact ball bearings, are primarily suitable for carrying axial loads. Cylindrical roller bearings can only bear pure radial loads and minimal axial loads. Other radial bearings (such as tapered roller bearings and spherical roller bearings) can carry axial loads in addition to radial loads, but there are also minimum load considerations.
Angular contact ball bearings can support moderate axial loads at relatively high speeds. For moderate and heavy axial loads acting in one direction, specify spherical roller thrust bearings. The bearing’s ability to carry axial loads will be determined by the contact angle or load action inside the bearing (the greater the angle, the suitable the bearing is for axial loads). Single row angular contact ball bearings and tapered roller bearings can only bear axial load in one direction. In applications where axial loads act alternately, these bearings must be combined with another bearing capable of withstanding the axial loads. When radial and axial loads act simultaneously, combined loads occur. In these cases, the most common bearing solutions are single- and double-row angular contact bearings and single-row tapered roller bearings (although deep groove ball bearings may also be suitable, depending on the ratio of axial to radial loads).

Speed.
Rotational speed affects operating temperature, which in turn affects bearing and lubricant life. Therefore, the cage, lubricant, operating accuracy and clearance of the bearing, the resonant frequency of the system and the balance of the rotating parts are all important factors in bearing selection. For high-speed applications, ball bearings are often suitable than roller bearings. In ultra-high speed applications, precision bearings or hybrid bearings may provide benefits.
Temperature.
The allowable bearing operating temperatures in motor applications will limit the operating speed of rolling bearings. Bearing types with low friction and low internal bearing heat work well in high-speed operation. When the load is pure radial load, deep groove ball bearings can achieve the highest speed; when the load is combined load, angular contact ball bearings can achieve the highest speed. This is especially true for bearings with ceramic rolling elements.
lubricating
Under normal speed and temperature conditions, motor bearings are usually lubricated with grease. Grease enables simpler, cost-effective housing and seal designs, allows the lubricant to adhere better to critical surfaces, and provides reliable protection against fouling than oil. The life expectancy of a grease depends on a variety of factors, including the type of bearing, the type of grease, the direction and speed of the motor, and the operating temperature of the bearing. The small ball bearings in standard electric motors are usually equipped with seals or guards and are lubricated for life—they do not need to be re-greased, but can be replaced during normal motor service intervals. Regardless of size, heavy-duty electric motors are typically equipped with open bearings and relubrication. (If the grease life is shorter than the expected bearing life, the bearings will obviously need to be relubricated while the grease is still functioning as expected.)

Sometimes, rotational speed or operating temperature make the use of grease impractical or impossible because the grease life or relubrication time is too short. These situations require oil lubrication. Generally, only large electric motors are lubricated with oil, in part because of the need for complex seals and the potential risk of system leakage.
Operating environment
Factors such as ambient temperature, operating temperature, humidity, and the presence of contaminants such as dust, dirt, metal, wood, or plastic particles can all affect the type of bearing you choose and whether the bearing needs to be shielded or sealed. Moisture is particularly damaging to bearings, so steps must always be taken to mitigate the effects of moisture in humid or condensation-prone environments.
Causes of motor bearing failure
When a motor fails, bearings may be the culprit, but there are many causes other than bearings. These causes include winding, wiring, grease or seal failure, which in turn can lead to bearing failure (although the bearing is not the root cause). Improper use and maintenance of motors can increase the potential for problems and premature bearing failure.
Arc
Stray currents generated by arcing can cause bearing damage. Although arcs generally tend to be isolated and localized, the effect on a bearing is almost like a series of small lightning strikes that melt and realign the internal bearing surface. The result is that some surface material flakes off and falls apart, creating noise in the bearing and possibly shortening service life. One way to avoid arcing problems is to isolate the bearings from shaft currents. Special ceramic coatings can be applied to the outer or inner diameter of the bearing to prevent current flow through the bearing. Hybrid bearing designs offer another solution by replacing the metal rolling elements within the bearing with ceramic balls or rollers. They effectively isolate the bearing from the inside.

Moisture
Moisture cannot always be avoided, but it can be controlled. Moisture is usually not harmful when the motor is running. However, when the motor is turned off and cooled down, condensation will occur. Condensation cannot be prevented, but the harmful effects can be prevented by using grease with added rust inhibitors in bearing assemblies and by rotating the shaft of an idling motor frequently when condensation is suspected. Good seals help prevent moisture from intruding into the cavity. It is also important to avoid spraying water directly on the seal when flushing.
Shaft misalignment
A common root cause of premature bearing failure, misalignment between the motor shaft and the drive equipment can induce excessive vibration and internal bearing loading and shorten the service life of the motor. Couplings are usually flexible and can accommodate misalignment. However, don’t take its flexibility for granted. To achieve ideal shaft alignment, first secure the drive equipment and then install the coupling. Only after the coupling is connected to the equipment should the motor be moved to the correct alignment and secured.
Improper lubrication
Effective bearing lubrication requires appropriate lubricant type and quantity, replenishment intervals and application methods. There are no general rules for correct lubrication intervals. Instead, intervals should be determined based on bearing size and type, operating speed, general operating environment, and motor type. (Vertical motors require lubrication twice as often as horizontal motors.) Bearings that are sealed or shielded for life generally should not be relubricated. Before lubricating a bearing, determine the grease currently used and select the same type of grease or a compatible product – not all greases are compatible. (Lubricant manufacturers provide compatibility charts.) Always consider the motor manufacturer’s recommendations.
Avoid over-lubrication
Adding lubricant than specified will shorten grease life by causing increased friction and temperature—potentially damaging bearings and adversely affecting motor performance. If there is too much grease, the rolling elements require energy to rotate. This puts a greater burden on the motor. Over-lubrication can also lead to undesirable heat buildup as the rolling elements try to push excess grease away. Heat buildup causes friction, wear and shortened grease life.
Conclusion
Proper selection, installation and maintenance of bearings can help optimize the performance and service life of your electric motor. First, you need to understand the operating conditions of the motor, including information on speed, workload, temperature, and noise. Especially under high-speed operation, bearings must have high active stability and rigidity to ensure the normal operation of the motor. Determine the model according to the usage conditions and requirements of the motor. It is recommended to choose some well-known brands and high-quality bearing models. At the same time, pay attention to the specifications and accuracy of the bearings. Carry out appropriate calculations and tests, verify and adjust the bearing model to ensure that the motor can operate normally under various working conditions. In addition, during use, some basic maintenance and upkeep work is required, such as cleaning and lubricating the bearings.


Choosing the right bearing type is important, but not the only criterion. In addition, it is also necessary to consider the influence of many factors such as bearing material, accuracy, lubrication method, and size. For large motors or motors running at high speed, special attention should be paid to the technical indicators and quality of the bearings. When performing motor maintenance and parts replacement, attention should be paid to bearing selection, installation, and debugging to ensure the normal operation of the motor. In short, choosing the correct motor bearing model is an important safeguard to ensure the normal operation of the motor. When selecting motor bearings, it is necessary to evaluate and select based on actual conditions and requirements to ensure the service life and performance level of the motor. Sorting through all the relevant factors can be difficult, but you don’t have to do it alone. A knowledgeable bearing manufacturer can help you find the best solution for your specific application needs.