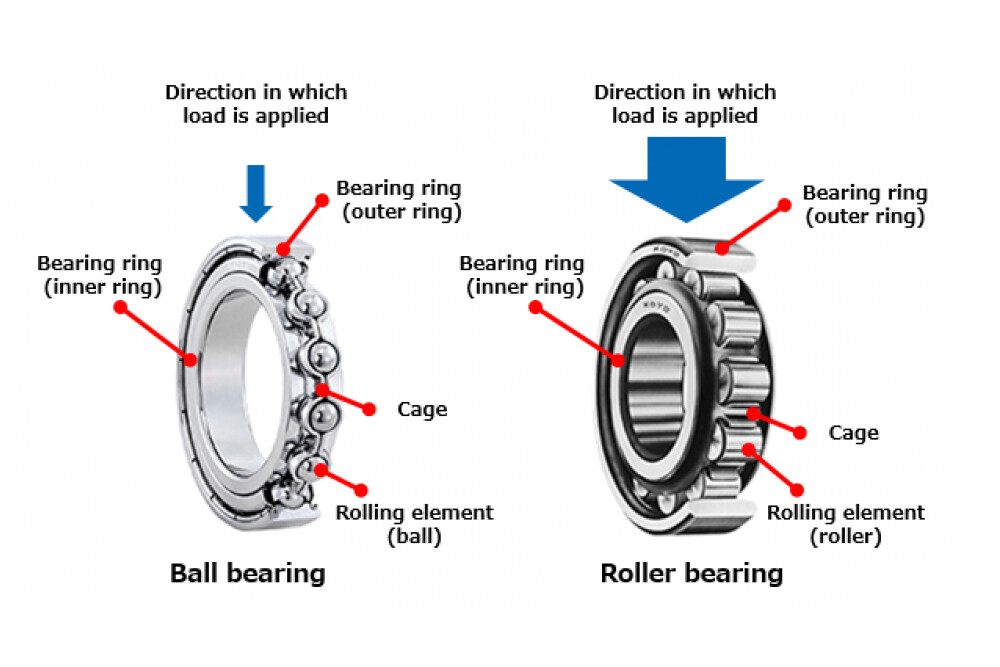
Bearing Manufacturer & Supplier
Specialize in ball bearings, roller bearings, thrust bearings, thin section bearings etc.
You Should Know About Rolling Bearings
A rolling bearing is a precision mechanical component that changes the sliding friction between the running shaft and the shaft seat into rolling friction, thereby reducing friction losses. Rolling bearings generally consist of four parts: inner ring, outer ring, rolling elements and cage. The function of the inner ring is to cooperate with the shaft and rotate together with the shaft; the function of the outer ring is to cooperate with the bearing seat and play a supporting role; the rolling element is Because the cage evenly distributes the rolling elements between the inner ring and the outer ring, its shape, size and number directly affect the performance and life of the rolling bearing; the cage can evenly distribute the rolling elements and guide the rolling elements to rotate for lubrication.
Table of Contents
ToggleComponents of rolling bearings
The five components of rolling bearings are: inner ring, outer ring, rolling elements, cage, and grease. Rolling bearings generally consist of four components: inner ring, outer ring, rolling elements and cage. In addition, lubricants have a great impact on the performance of rolling bearings, so lubricants are sometimes regarded as the fifth largest component of rolling bearings. The components of rolling bearings have the following functions:
The inner ring usually fits tightly with the shaft and rotates with the shaft.
The outer ring usually cooperates with the bearing seat hole or the mechanical component shell to play a supporting role. However, in some applications, the outer ring rotates and the inner ring is fixed, or both the inner and outer rings rotate.
The rolling elements are evenly arranged between the inner ring and the outer ring with the help of the cage. Its shape, size and quantity directly affect the load-bearing capacity and performance of the bearing.
The cage evenly separates the rolling elements, guides the rolling elements to move on the correct track, and improves the internal load distribution and lubrication performance of the bearing.

Rolling bearing rings
(1) Inner ring: The bearing ring with the raceway on the outer surface.
(2) Outer ring: The bearing ring with raceway on the inner surface.
(3) Tapered inner ring: the inner ring of tapered roller bearings.
(4) Tapered outer ring: the outer ring of tapered roller bearings.
(5) Double raceway tapered inner ring: a tapered roller bearing inner ring with double raceways.
(6) Double raceway tapered outer ring: a tapered roller bearing outer ring with double raceways.
(7) Wide inner ring: A bearing inner ring that is widened at one or both ends to improve the guidance of the shaft in its inner bore or to provide supplementary position for installing fasteners or seals.
(8) Locked inner ring: a grooved ball bearing inner ring with all or part of the shoulder removed.

(9) Locked outer ring: A grooved ball bearing outer ring with all or part of the shoulder removed.
(10) Stamped outer ring: A ferrule that is stamped from a thin metal plate and sealed at one end (sealed stamped outer ring) or open at both ends, generally pointing to the outer ring of the radial needle roller bearing.
(11), Flange outer ring: Bearing outer ring with flange.
(12) Aligning outer ring: An outer ring with a spherical outer surface to adapt to the permanent angular displacement between its axis and the axis of the bearing seat.
(13) Aligning outer seat ring: The ferrule used for aligning the outer ring and the seat hole has a spherical inner surface that matches the spherical outer surface of the outer ring.
(14) Outer spherical surface: The outer surface of the bearing outer ring is part of the ball surface.
(15). The rib on the front of the conical outer ring: the rib on the front of the raceway of the conical outer ring is used to guide the roller and bear the thrust of the large end face of the roller.
(16) Middle retaining ring: A bearing ring with double raceways, such as the middle integral rib of a double raceway conical inner ring.
Manufacturing of rolling bearing rings
(1) Forging: During the forging process, overburning, overheating, internal cracking into network carbides, etc. will reduce the toughness and strength of the ferrule. Therefore, the processing temperature, circulating heating and post-forging heat dissipation conditions (such as spray cooling) must always be strictly controlled. Especially after the final forging of larger types of ferrules, those with a temperature above 700°C must not be piled up.
(2) Heat treatment: Close monitoring of heat treatment equipment is an important task in the workshop. Monitoring equipment reliability. Important temperature control equipment such as instruments and thermocouples must be closely monitored to ensure accurate and reliable measurement data; those with excessive errors must be replaced in a timely manner, and operation while sick is strictly prohibited.

(3) Monitoring of grinding process. The finished imported bearing rings are not allowed to have grinding burns and grinding cracks, especially the mating surface of the inner ring driver taper must not have burns. If the ferrules are pickled, they should be fully inspected to remove burned products. Severely burned ones cannot be repaired or those that fail to be repaired should be scrapped. Rings with grinding burns are not allowed to enter the assembly process.
(4) Identification management. After the steel is put into storage and before the ferrule is ground, each process must be strictly managed, and two different materials and products, GCR15 and GCR15SIMN, must be strictly distinguished.
Installation of rolling bearing rings
When installing bearing rings, special attention should be paid to the installation sequence. Precision bearings should also pay attention to the positive and negative ends. Installing them backwards will cause dynamic imbalance and affect the performance of the bearing.
Rolling element
The rolling element is the core element in the rolling bearing. Due to its existence, there is rolling friction between the relative moving surfaces. The types of rolling elements include balls, cylindrical rollers, tapered rollers, needle rollers, etc. The rolling elements of rolling bearings mainly include steel balls and rollers.
Basic structure of rolling bearings
The working principle of rolling bearings developed based on sliding bearings is to replace sliding friction with rolling friction. They are generally composed of two rings, a set of rolling elements and a cage. They are highly versatile, standardized and highly serialized. High mechanical base parts. Since various machines have different working conditions, various requirements are put forward for rolling bearings in terms of load capacity, structure and performance. For this reason, rolling bearings need to have various structures. However, the most basic structure is composed of inner ring, outer ring, rolling elements and cage. The functions of various parts in bearings are:
For radial bearings, the inner ring is usually a tight fit with the shaft and runs together with the shaft, and the outer ring is usually a transition fit with the bearing seat or mechanical housing hole to play a supporting role. However, in some cases, the outer ring is also running, and the inner ring is fixed to play a supporting role, or both the inner ring and the outer ring are running at the same time. For thrust bearings, the shaft ring is a tight fit with the shaft and moves together, and the seat ring is a transition fit with the bearing seat or mechanical housing hole and plays a supporting role. The rolling elements (steel balls, rollers or needle rollers) are usually evenly arranged between the two rings in the bearing with the help of a cage for rolling motion. Its shape, size and number directly affect the load capacity and performance of the bearing. In addition to evenly separating the rolling elements, the cage can also guide the rotation of the rolling elements and improve the internal lubrication performance of the bearing.
Rolling bearing classification
Classification by rolling bearing structure type
Bearings are divided into: according to the load direction or nominal contact angle they can bear:
1) Radial bearings – rolling bearings mainly used to bear radial loads, with nominal contact angles from 0 to 45. According to different nominal contact angles, they are divided into: radial contact bearings – radial bearings with a nominal contact angle of 0; centripetal angular contact bearings – radial bearings with a nominal contact angle greater than 0 to 45.
2) Thrust bearings – rolling bearings mainly used to bear axial loads, with nominal contact angles greater than 45 to 90. According to different nominal contact angles, they are divided into: Axial contact bearings – thrust bearings with a nominal contact angle of 90°; Thrust angular contact bearings – thrust bearings with a nominal contact angle greater than 45 but less than 90°.
According to the type of rolling element
1) Ball bearing—-the rolling element is ball.
2) Roller bearing—-The rolling elements are rollers. According to the type of roller, roller bearings are further divided into: cylindrical roller bearings – bearings in which the rolling element is a cylindrical roller, and the ratio of the length to diameter of the cylindrical roller is less than or equal to 3; needle roller bearings – Bearings in which the rolling element is a needle roller. The ratio of the length to diameter of the needle roller is greater than 3, but the diameter is less than or equal to 5mm; tapered roller bearings – bearings in which the rolling element is a tapered roller; spherical roller bearings – one by one The rolling elements are spherical roller bearings.
Bearing alignment function
1) Aligning bearing – the raceway is spherical and can adapt to the angular deviation and angular movement between the axis lines of the two raceways;
2) Non-aligning bearings (rigid bearings) – bearings that can resist the angular deviation of the axis center line between the raceways.
Bearings according to the number of rows of rolling elements
1) Single row bearing – a bearing with one row of rolling elements;
2) Double row bearings – bearings with two rows of rolling elements;
3) Multi-row bearings – bearings with than two rows of rolling elements, such as three-row and four-row bearings.
Bearings according to whether they can be separated
1) Separable bearings – bearings with separable parts;
2) Non-separable bearings – bearings in which the rings cannot be separated freely after the bearings are finally assembled.
Bearings according to their structural shape
Such as whether there is a filling groove, whether there is an inner and outer ring and the shape of the ferrule, the structure of the rib, and even whether there is a cage, etc.) can also be divided into multiple structural types.
Classification according to the size of rolling bearings
(1) Miniature bearings – bearings with a nominal outer diameter range of less than 26mm;
(2) Small bearings—-bearings with nominal outer diameter ranging from 28-55mm;
(3) Small and medium-sized bearings—bearings with nominal outer diameters ranging from 60 to 115 mm;
(4) Medium and large bearings—-bearings with nominal outer diameter ranging from 120-190mm
(5) Large bearings – bearings with nominal outer diameters ranging from 200-430mm;
(6) Extra large bearings—-bearings with a nominal outer diameter range of 440mm or
Rolling bearing manufacturing process
Due to the different types, structural types, tolerance levels, technical requirements, materials and batch sizes of rolling bearings, their basic production processes are not exactly the same.
Manufacturing process of bearing components:
(1) The processing process of the ferrule: The processing of the inner and outer rings of the bearing varies depending on the raw material or blank form. The processes before turning can be divided into the following three types. The entire processing process is: Rod Material or pipe material (some bars need to be forged, annealed, and normalized) —- turning processing —- heat treatment —- grinding processing —- fine grinding or polishing —- final inspection of parts —-Rustproof—-Storage—-(to be assembled together)
(2) The processing process of steel balls. The processing of steel balls also varies according to the state of the raw materials. The process before crushing or polishing the ball can be divided into the following three types. The process before heat treatment can also be It is divided into the following two types, and the entire processing process is: Cold punching of bars or wires (some bars need to be punched with rings and annealed after cold punching) – Frustrating, rough grinding, soft grinding or photo ball – –Heat treatment—-Hard grinding—-Fine grinding—-Precision grinding or grinding—-Final inspection grouping—-Rust prevention, packaging—-Storage <to be assembled>.
(3) Processing of rollers. The processing of rollers varies depending on the raw materials. The process before heat treatment can be divided into the following two types. The entire processing process is: bar turning processing or wire rod cold heading and stringing. Ring belt and soft grinding —- heat treatment —- soft spots —- rough grinding outer diameter —- rough grinding end face —- final grinding end face —- fine grinding outer diameter —- Final grinding outer diameter —- final inspection grouping —- rust prevention, packaging —- storage (to be assembled together).
(4) The processing process of the cage. The processing process of the cage can be divided into the following two categories according to the design structure and raw materials:
1) Sheet metal → shearing [1] → punching → stamping → shaping and finishing → pickling or shot peening or string polishing → final inspection → rust prevention, packaging → warehousing (to be assembled as a set)
2) The processing process of the solid cage: The processing of the solid cage varies depending on the raw materials or roughness. Before turning, it can be divided into the following four blank types. The entire processing process is: bar, tube Materials, forgings, castings—-car inner diameter, outer diameter, end face, chamfering—-drilling (or drawing, boring)—-pickling—-final inspection—-prevention Rust, packaging—-storage <to be assembled>.
Assembly process of rolling bearings:
Rolling bearing parts such as inner rings, outer rings, rolling elements and cages, etc., after passing the inspection, enter the assembly workshop for assembly. The process is as follows: parts demagnetization and cleaning → inner and outer rolling (groove) channel size group selection → assembly Set → check clearance → rivet cage → final inspection → demagnetization, cleaning → rust prevention, packaging → put into finished product warehouse (packing, shipping).
Characteristics of rolling bearings
Compared with sliding bearings, rolling bearings have the following advantages:
(1) The friction coefficient of rolling bearings is smaller than that of sliding bearings, and the transmission efficiency is high. Generally, the friction coefficient of sliding bearings is 0.08-0.12, while the friction coefficient of rolling bearings is only 0.001-0.005;
(2) Rolling bearings are made of bearing steel and undergo heat treatment. Therefore, rolling bearings not only have high mechanical properties and long service life, but also can save relatively expensive non-ferrous metals used in manufacturing sliding bearings;
(3) The internal clearance of the rolling bearing is very small, and the processing accuracy of each part is high. Therefore, the operating accuracy is high. At the same time, the rigidity of the bearing can be increased through preloading. This is very important for precision machinery;
(4) Some rolling bearings can bear both radial load and axial load, so the structure of the bearing support can be simplified;
(5) Due to the high transmission efficiency of rolling bearings and low heat generation, the consumption of lubricating oil can be reduced, making lubrication maintenance easier;
(6) Rolling bearings can be easily applied to uranium in any direction in space.
Rolling bearings also have certain disadvantages
However, everything is divided into two, and rolling bearings also have certain shortcomings, mainly:
(1) The load-bearing capacity of rolling bearings is much smaller than that of sliding bearings of the same volume. Therefore, the radial size of rolling bearings is large. Therefore, sliding bearings are often used in situations that bear large loads and require small radial dimensions and compact structures (such as internal combustion engine crankshaft bearings);
(2) The vibration and noise of rolling bearings are large, especially in the later stages of use. Therefore, rolling bearings are not suitable for occasions where high precision is required and vibration is not allowed. Generally, sliding bearings are better.
(3) Rolling bearings are particularly sensitive to foreign matter such as metal shavings. Once foreign matter enters the bearing, intermittent large vibrations and noise will occur, which may also cause early damage. In addition, rolling bearings are also prone to early damage due to metal inclusions. Even if early damage does not occur, the life of rolling bearings has a certain limit. In short, the life of rolling bearings is shorter than that of sliding bearings.
However, compared with rolling bearings and sliding bearings, each has its own advantages and disadvantages, and each has certain applicable occasions. Therefore, the two cannot completely replace each other, and each develops in a certain direction and expands its own field. However, due to the outstanding advantages of rolling bearings, there is a tendency for latecomers to catch up. Rolling bearings have developed into the main support type of machinery and are used and widely.
Cage
Cage, also known as bearing cage, refers to a bearing part that partially wraps all or part of the rolling elements and moves with it to isolate the rolling elements, and usually also guides the rolling elements and keeps them inside the bearing.
Cage material
When rolling bearings are working, sliding friction causes bearing heating and wear. Especially under high-temperature operating conditions, the action of inertial centrifugal force intensifies friction, wear and heat. In severe cases, the cage may be burned or broken, causing the bearing to not work properly. Therefore, in addition to having a certain strength, the material of the cage must also have good thermal conductivity, small friction factor, good wear resistance, strong impact toughness, low density, and a linear expansion coefficient close to that of the rolling elements. In addition, the stamped cage needs to withstand complex stamping deformation and requires the material to have good processing properties. Some cages with extremely high requirements will also be coated with a layer of silver. The types of cage materials include: mild steel/stainless steel cage, bakelite/plastic (nylon) cage, brass/bronze/aluminum alloy cage, etc.

Classification of manufacturing methods:
die-cast cage
The raw materials of the die-cast cage are aluminum alloy and brass. The raw materials are melted and poured into the die-casting mold of the die-casting machine, and the cage is die-cast in one go. The casting gate is turned on a lathe.
1) The cage is directly die-cast, which can obtain good geometric shape and dimensional accuracy without mechanical processing, and has high production efficiency.
2) After die-casting, the metal crystallizes and solidifies, with precise structure, good surface quality and wear resistance.
3) High material utilization rate and reduced cost. However, when die-casting an aluminum alloy cage, large-tonnage equipment is required, and the mold design and manufacturing are complicated. The cage pockets are easily strained during die-casting. Under the conditions where the bearing is subjected to impact, vibration and variable speed, the quality of the die-cast cage needs to be further improved.
Cage manufactured by plastic casting method
Vacuum-dried granular engineering plastics are placed in a barrel, heated by resistance wires and melted into a semi-liquid state. Pressurized by a plunger or moving screw, the semi-liquid raw materials are injected from the nozzle into the forming mold of the injection molding machine. After being insulated, , obtain the required cage after cooling. The characteristics of his craftsmanship are:
1) The cage is molded in one injection molding, which can obtain precise geometric shape and dimensional accuracy and low surface roughness value without mechanical processing, and the production efficiency is high.
2) The mold and plastic casting are simple to form, the bearing is easy to assemble, and it is easy to realize automatic control.
3) The plastic cage has good properties such as wear resistance, antimagnetic and low friction. However, due to the shortcomings of thermal deformation, aging and brittleness of the plastic itself, as well as some problems in the cage structure and plastic injection process, the application of the plastic cast cage is limited.
Grease
Grease: A thick, greasy semi-solid. Used for the friction parts of machinery to lubricate and seal. Also used on metal surfaces to fill gaps and prevent rust. Mainly made of mineral oil (or synthetic lubricant) and thickener. The main functions of grease are lubrication, protection and sealing. The vast majority of greases are used for lubrication and are called anti-friction greases. Antifriction grease mainly plays the role of reducing mechanical friction and preventing mechanical wear. At the same time, it also plays a protective role in preventing metal corrosion and sealing and dustproof. There are some greases that are primarily used to prevent metal from rusting or corroding, called protective greases.

The working principle of grease is that the thickener keeps the oil where it needs to be lubricated. When there is a load, the thickener releases the oil, thus providing lubrication.At room temperature and in a static state, it is like a solid, able to maintain its shape without flowing, and can adhere to metal without slipping. At high temperatures or when subjected to external forces exceeding a certain limit, it can flow like a liquid. When grease is sheared by moving parts in machinery, it can flow and lubricate, reducing friction and wear between moving surfaces. When the shearing action stops, it can return to a certain consistency. The special fluidity of grease determines that it can be lubricated in parts that are not suitable for lubricating oil. In addition, because it is a semi-solid substance, its sealing and protective effects are better than lubricating oil.