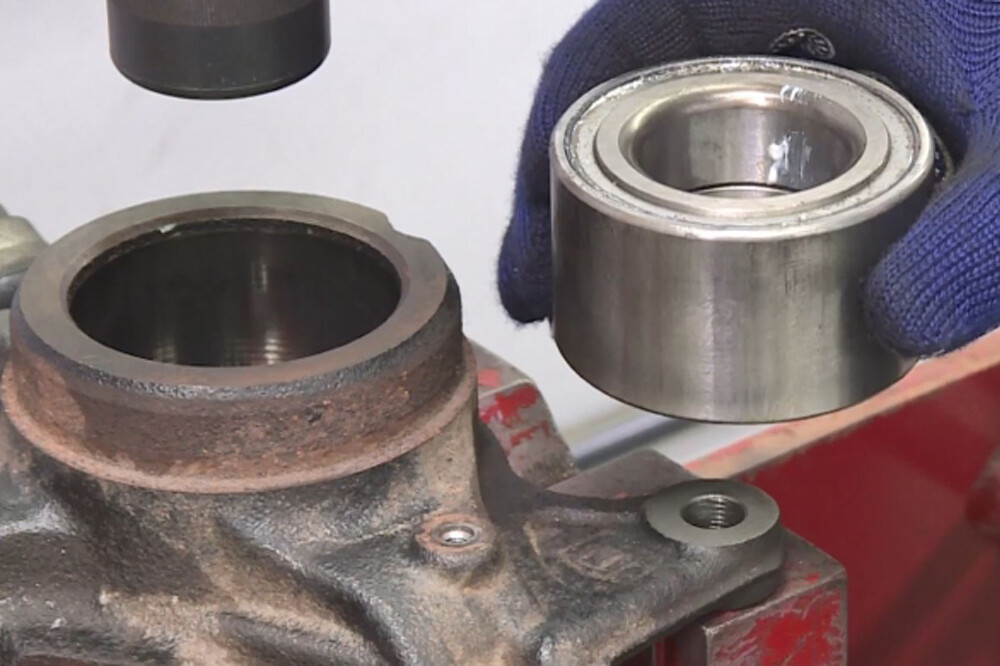
Bearing Manufacturer & Supplier
Specialize in ball bearings, roller bearings, thrust bearings, thin section bearings etc.
When do you need to replace bearings?
According to incomplete statistics, approximately 10 billion bearings are produced around the world every year. In fact, only a small percentage of bearings in use will fail, and most bearings (approximately 90%) will last longer than the maintenance intervals on the equipment they are installed on. For safety (prevention) reasons, some bearings (9.5%) are replaced before failure, and about 0.5% of bearings are replaced after damage or failure, which means that approximately 50 million bearings are replaced every year due to damage and failure. It failed and was replaced.
The effects of bearing failure can range from minor to completely catastrophic, causing irreparable damage to surrounding machinery. No business is willing to bear the cost of bearing failure if it can be avoided. That’s why it’s important to be able to recognize the warning signs of bearing failure so that you can quickly identify and replace the bearing before it occurs.
Table of Contents
ToggleWarning signs of bearing failure
Here are five warning signs of bearing failure that you should be aware of and that indicate it’s time to replace a bearing before it fails.
lubricating
36% of bearing failures are attributed to lubrication issues, and using the wrong type or amount of lubricant is known to cause bearing failure. Contamination can also occur during the relubrication process when foreign particles get stuck on the end of the grease gun and enter the bearing.
Different operating conditions require different lubricants, different relubrication intervals and different lubricant change intervals. So it’s not just about using the right lubricant, but also the right amount of lubricant in the right way at the right time. If you find that the wrong type of grease has been used on a bearing, a failure has probably occurred. Likewise, if a bearing is running dry due to lack of lubrication, or if grease is leaking through a seal due to overlubrication, bearing damage has most likely occurred. Adding grease to bearings that are having problems with lubrication seems like a good solution. In fact, it just masks the problem. You need to use data such as temperature and vibration to determine the severity of the problem and replace the bearing before it causes catastrophic failure.

For example, in the pulp and paper industry, the main causes of bearing failure are contamination and insufficient lubrication, not fatigue. Each failure produces a special damage imprint, which is called a “trace”. Therefore, in most cases, the root cause of the damage can be identified by carefully inspecting the damaged bearing. Depending on the cause of the damage, corrective measures can be taken to prevent the problem from happening again.
The purpose of a seal or shield is to prevent lubricant from flowing out of the bearing and contaminants from entering the bearing. If the seal or shield fails, it can cause premature bearing failure. When should bearings be replaced? The time from initial (initial) bearing damage to complete unusability can vary greatly. In high-speed operation, this may be only a few seconds, and in large equipment running at slow speed, it may be up to several months. “When should I replace my bearings?” This question can be best answered through bearing condition monitoring. If damaged bearings continue to operate without inspection and are not replaced before catastrophic failure occurs, secondary damage to the equipment and its components may occur. over, once a bearing fails catastrophically, the root cause of the failure can be difficult or even impossible to determine.
14% of bearing failures are caused by contamination. High-pressure washing can emulsify the grease, rendering it ineffective. This causes metal-to-metal contact within the bearing, creating heat and friction. Inefficient seals can also lead to particle contamination that destroys the grease. This particulate contamination can also be abrasive, causing damage to bearing raceway surfaces. If you realize that contamination has occurred within a bearing, it is wise to replace the bearing as soon as possible. Chances are, it’s only a matter of time before a failure has already occurred, causing further problems with your machine.

Take the application of seal failure as an example. When contaminant particles pass through the seal and enter the bearing, they will be crushed by the rolling elements and form indentations on the raceway. Harder particles may form indentations with sharp edges. Afterwards, the area around the indentation will undergo cyclic stress under the normal rolling of the rolling elements, causing surface fatigue and this part of the metal begins to separate from the raceway. This phenomenon is called exfoliation. Once spalling occurs, the damage increases until the bearing becomes unusable.
Vibration
Vibration is a sure sign of bearing failure. If the raceway surface of a bearing is damaged by wear, the rolling elements (balls or rollers) will bounce on the raceway surface during operation, causing severe vibrations. If you find that the bearing suddenly vibrates during operation, you need to replace it. If not, you may find that catastrophic failure is just around the corner, resulting in excessive downtime and high costs.
Too much noise
If your bearing suddenly makes a noise during operation, the bearing may be faulty. This excessive noise occurs when the bearing raceways are damaged, causing the rolling elements to bounce or rattle during rotation. If you notice that the bearings are making excessive noise while running, they need to be replaced as soon as possible. The fault has already occurred inside the bearing, and the machine may fail at any time.
Bearing operating temperature is too high
A bearing’s rolling elements become damaged when they run on unlubricated raceways, which causes excessive friction. The energy generated by this friction causes the bearing temperature to rise. The severe the damage, the higher the temperature will be due to the degree of friction present. Regularly checking the temperature of your bearings can alert you to a bearing failure that needs to be addressed as soon as possible. It is important not only to replace the bearings but also to find the root cause of the failure. Performing an effective root cause analysis allows you to take mitigation measures to avoid future bearings suffering the same fate, further downtime and additional business costs. Condition monitoring systems are a great way to continuously monitor the health of your machine during operation, alerting you to potential problems. This gives you time to fix the problem and prevent a failure.
Development stages of bearing damage
The service life of the bearings has been tested before they are shipped from the factory. However, due to different environments or methods of use, the actual service life of the bearings may differ from the actual life. Some bearings have problems before they reach the end of their life, and they have to be replaced in advance. There are special mathematical formulas for calculating the frequency of bearing failure. However, it is troublesome to calculate in actual work. The convenient method is to use special software to obtain it. As long as you input the bearing model and manufacturer information, you can get the corresponding information. bearing failure frequency. Overall, the fault frequency precursors can be analyzed using the following conditions:

Budding stage
The first stage is the budding stage when the bearing begins to fail. At this time, the temperature is normal, the noise is normal, and the total vibration speed and spectrum are normal. However, the peak energy total and spectrum show signs, reflecting the initial stage of bearing failure. At this time, the real bearing failure frequency appears in the ultrasonic segment in the range of approximately 20-60khz.
Slightly noisy
In the second stage, the temperature is normal, the noise increases slightly, the total vibration speed increases slightly, and the vibration spectrum does not change significantly, but the peak energy increases greatly and the spectrum becomes prominent. The bearing failure frequency at this time appears in the range of approximately 500hz-2khz.
Temperature is slightly high and noise is heard
In the third stage, the temperature rises slightly, noise can be heard, the total vibration speed increases greatly, and the bearing failure frequency and its harmonics and sidebands are clearly visible on the vibration speed spectrum. In addition, the noise level on the vibration speed spectrum rises significantly. Compared with the second stage, the total amount of peak energy becomes larger and the spectrum becomes prominent. The bearing failure frequency at this time appears in the range of approximately 0-1khz. It is recommended to replace the bearings at the end of the third stage, when the wear and tear that can be seen by the naked eye and other rolling bearing failure characteristics should have appeared.
As the temperature rises, the noise increases
In the fourth stage, the temperature increases significantly, the noise intensity changes significantly, the total vibration velocity and vibration displacement increase significantly, and the bearing failure frequency on the vibration velocity spectrum begins to disappear and is replaced by a larger random broadband high-frequency noise horizon; The total amount of spike energy increases rapidly, and some unstable changes may occur. Bearings must never be allowed to operate in the fourth stage of failure development, otherwise catastrophic damage may occur.
Conclusion
According to research results, the entire service life of a general rolling bearing is from the time the bearing is installed and put into use. During the first 80% of its life time, the bearing is normal. And then corresponding to the development of rolling bearing failure, its remaining life is 10%~20%L10 in the first stage, 5%-10%L10 in the second stage, 1%~5%L10 in the third stage, and about 1h or 1%L10.
Therefore, when facing bearing problems in actual work, considering that the fourth stage of bearing failure development has unforeseeable sudden hazards, it is recommended to replace the bearing in the late third stage, so as to avoid the expansion of the fault and serious accidents. occurrence, and can ensure the service life of the rolling bearing as much as possible, and based on the fact that at this time the bearing has also seen wear, component damage and other rolling bearing failure characteristics that can be seen with the naked eye, it is convincing. As for the identification of the late third stage of bearing failure development, it needs to be comprehensively considered based on the above theoretical characteristics combined with actual temperature, noise, speed spectrum, peak energy spectrum, total trend of speed and peak energy, and actual experience.