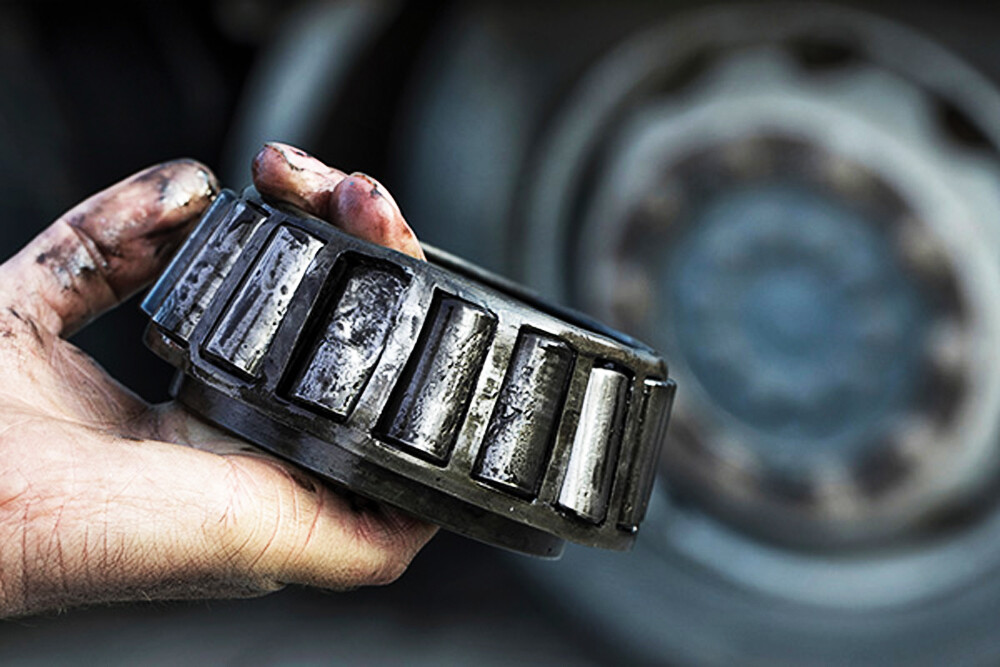
Bearing Manufacturer & Supplier
Specialize in ball bearings, roller bearings, thrust bearings, thin section bearings etc.
The Ultimate Guide to Causes of Bearing Failure
Bearings combine rotating parts (shafts) and stationary parts (bearing housings) with minimal friction. It is precisely because of the role of bearings that various rotating equipment such as cars, airplanes, generators, conveyors, and motors can run smoothly. With the rapid development of scientific and technological progress, customers have higher and higher requirements for the quality of bearing products. It is important for bearing manufacturers to provide high-quality bearings that meet standards and meet performance requirements, but it is even important to use them correctly. Based on many years of bearing manufacturing technology work, Aubearing often encounters the problem that the bearing is qualified after testing, but the bearing becomes stuck after installation or early rotation failure during use. The main symptoms include a sense of rotational stuckness, severe peeling of the working surface, severe wear and even distortion and fracture of the cage. Analysis of the failure results shows that there are not many quality problems related to the bearing itself, and most of them are caused by improper installation and use. For this reason, Aubearing believes that it is necessary to review the common failure modes of bearings and provide constructive suggestions to further improve bearing life.
Table of Contents
ToggleBasic knowledge of bearings
Rolling bearings are high-precision components made of high-hardness bearing steel (AISI52100). Now and rolling bearings use ceramic rolling elements. Bearings consist of inner and outer rings, balls or rollers, and cages. Some bearings also have seals or dust covers. Such sealed bearings are prefilled with grease at the factory. The lubricating oil or grease is critical to the thickness of the lubricating film that needs to be established to separate the rolling elements and raceways. Suitable bearings must be selected for the equipment and installed correctly to ensure that the bearings are well lubricated and free of contamination.

Causes of bearing failure
When looking for signs of damage, it is important to properly understand the internal bearing geometry and how the bearing works. Comparing the raceway load traces of damaged bearings removed from equipment with well-operating bearings can help understand the cause of bearing damage. It is also important to guard against counterfeit bearings, as counterfeit bearings often have a much shorter service life than bearings made by reputable bearing manufacturers. If the machine is overloaded, used or maintained improperly, the bearings will be affected, and 34% of premature bearing failures are due to fatigue. Because bearings will give an “early warning” when they are improperly maintained or overstressed.

Contact Fatigue
Contact fatigue failure refers to failure caused by alternating stress on the working surface of the bearing. Contact fatigue spalling occurs on the working surface of the bearing and is often accompanied by fatigue cracks. It first occurs from the maximum alternating shear stress below the contact surface, and then expands to the surface to form different spalling shapes, such as pitting or pitting spalling. Peeling off into small flakes is called shallow peeling. Due to the gradual expansion of the peeling surface, it often extends to deep layers, forming deep peeling. Deep spalling is a fatigue source of contact fatigue failure.

Wear Failure
Wear failure refers to the failure caused by the relative sliding friction between surfaces causing continuous wear of the metal on the working surface. Continuous wear will cause gradual damage to bearing parts, eventually leading to loss of bearing dimensional accuracy and other related problems. Wear may affect shape changes, increase the fitting clearance, and change the topography of the working surface. It may affect the lubricant or contaminate it to a certain extent, causing the lubrication function to be completely lost, thus causing the bearing to lose rotational accuracy or even fail to operate normally. Wear failure is one of the common failure modes of various types of bearings. According to the wear form, it can usually be divided into the most common abrasive wear and adhesive wear.

Abrasive wear refers to the wear caused by the squeeze of foreign hard particles or hard foreign matter or wear debris on the metal surface between the working surfaces of the bearing and the relative movement of the contact surfaces, often causing furrow-like scratches on the working surface of the bearing. Hard particles or foreign matter may come from inside the host or from other adjacent parts of the host system and are sent into the bearing by the lubricating medium. Adhesive wear refers to the uneven stress on the friction surface due to microscopic protrusions or foreign matter on the friction surface. When the lubrication conditions seriously deteriorate, local friction heat is generated, which can easily cause local deformation of the friction surface and friction micro-welding. Serious The surface metal may be partially melted, and the force on the contact surface will tear the local friction welding point from the matrix and increase the plastic deformation. This adhesion-tear-adhesion cycle constitutes adhesive wear. Generally speaking, slight adhesive wear is called abrasion, and severe adhesive wear is called occlusion.
Fracture Failure
The main reasons for bearing fracture failure are design defects and overload. When the applied load exceeds the strength limit of the material and causes the part to break, it is called overload fracture. The main reason for overload is sudden host failure or improper installation. Defects such as micro-cracks, shrinkage cavities, bubbles, large foreign matter, overheated tissue and local burns in bearing parts can also cause fractures at the defects during impact overload or severe vibration, which is called defect fracture. It should be pointed out that during the manufacturing process of bearings, instruments can be used to correctly analyze whether the above-mentioned defects exist during factory re-inspection of raw materials, forging and heat treatment quality control, and machining process control. Control must still be strengthened in the future. But generally speaking, most of the common bearing fracture failures are overload failures.

Clearance change failure
When the bearing is working, due to the influence of external or internal factors, the original fitting clearance changes, the accuracy decreases, and even causes “seizure”, which is called clearance change failure. External factors such as excessive interference, improper installation, expansion caused by temperature rise, instantaneous overload, etc., and internal factors such as retained austenite and residual stress in an unstable state are the main reasons for clearance change failure.
Improper assembly
16% of premature failures of various bearings are due to improper assembly (usually due to excessive force…) and incorrect use of assembly tools. Some equipment requires mechanical, hydraulic or heating methods for correct and efficient installation and removal. SKF offers a full range of tools and equipment based on a variety of professional engineering service technologies to make these jobs easier, faster and cost-effective. Professional assembly using specialized tools and techniques is another solution for maximizing machine uptime.

Improper lubrication
Although a variety of “maintenance-free” sealed bearings can be installed, 36% of premature bearing failures are caused by incorrect technical application and improper use of grease. Any improperly lubricated bearing will inevitably fail prematurely before its normal service life. Since bearings are usually the most difficult parts of mechanical equipment to assemble and remove, problems can arise if they are not lubricated regularly. When manual maintenance is not possible, SKF can develop a fully automatic lubrication system to achieve optimal lubrication results. Effective lubrication using SKF grease, tools and technology as required will help to significantly reduce downtime

Pollute
Bearings are precision parts. If the bearings and grease are contaminated, they will not operate effectively. Further, since greased, maintenance-free sealed bearings make up only a small percentage of all bearings in use, at least 14% of all premature bearing failures are due to contamination issues. SKF has excellent bearing manufacturing and design capabilities and can provide sealing solutions for a variety of harsh working environments.

Bearing failure analysis method
In the process of analyzing bearing failure, many complicated phenomena are often encountered. Various experimental results may be contradictory or unclear. This requires repeated experiments and demonstrations to obtain sufficient evidence or counter-evidence. Only by using correct analysis methods, procedures, and steps can we find the real cause of failure. Generally speaking, bearing failure analysis can be roughly divided into the following three steps: collection of failed objects and background data, macroscopic inspection and microscopic analysis of failed objects.
Collection of invalid objects and background materials
Collect as many parts and fragments of failed things as possible. Fully understand the working conditions, usage process and manufacturing quality of failed bearings. Specific contents include:
(1) The load, rotation speed, working conditions of the main engine and other design working conditions of the bearing.
(2) Failure conditions of bearings and other related parts, and types of bearing failures.
(3) Bearing installation and operation records. Are there any abnormal operations during operation and use?
(4) Whether the actual load endured by the bearing during operation complies with the original design.
(5) The actual rotation speed of the bearing and the frequency of different rotation speeds.
(6) Whether there is a sharp increase in temperature or smoke, noise and vibration during failure.
(7) Whether there are corrosive media in the working environment, and whether there is any special surface oxidation color or other contamination color between the bearing and journal.
(8) Bearing installation records (including re-inspection of bearing dimensional tolerances before installation), bearing original clearance, assembly and alignment conditions, the rigidity of the bearing seat and machine base, and whether there are any abnormalities in the installation.
(9) Whether there is thermal expansion and power transmission changes during bearing operation.
(10) Bearing lubrication conditions, including lubricant brand, composition, color, viscosity, impurity content, filtration, replacement and supply status, etc., and collecting its sediments.
(11) Whether the material selection of the bearing is correct and whether the material quality meets the relevant standards or drawing requirements.
(12) Whether the manufacturing process of the bearing is normal, whether there is plastic deformation on the surface, and whether there are any surface grinding burns.
(13) Repair and maintenance records of failed bearings.
(14) Failure conditions of bearings of the same batch or type.
In the actual work of collecting background materials, it is difficult to meet all the above requirements. However, the information collected, the conducive it will be to obtain correct analytical conclusions.
Macroscopic inspection
Macroscopic inspection of failed bearings (including dimensional tolerance measurement and surface condition inspection and analysis) is the most important step in failure analysis. The overall appearance inspection can provide an overview of the bearing failure and the characteristics of the damaged parts, estimate the cause of the failure, observe the size, shape, location, quantity and characteristics of the defects, and intercept appropriate parts for further microscopic inspection and analysis. The contents of macro inspection include:
(1) Changes in appearance and size (including vibration measurement analysis, dynamic function analysis and raceway roundness analysis).
(2) Changes in clearance.
(3) Whether there is corrosion phenomenon, where it is, what type of corrosion it is, and whether it is directly related to the failure.
(4) Whether there are cracks, the shape of the cracks and the properties of the fracture.
(5) What type of wear is it and how much it contributes to failure.
(6) Observe the discoloration and location of the working surface of each bearing part to determine its lubrication condition and surface temperature effect.
(7) Mainly observe the failure characteristic area for abnormal wear, foreign particle embedding, cracks, scratches and other defects.
(8) Cold pickling method or hot pickling method is used to check whether there are soft spots, decarburized layers and burns on the original surface of bearing parts, especially surface grinding burns.
(9) Use an X-ray stress measuring instrument to measure the stress changes of the bearing before and after operation.
The results of macroscopic inspection can sometimes basically determine the form and cause of the failure, but to further determine the nature of the failure, evidence must be obtained and microscopic analysis must be done.
Microscopic analysis
Microscopic analysis of failed bearings includes optical metallographic analysis, electron microscope analysis, probe and electron energy spectroscopy analysis, etc. It is mainly based on the microstructural changes in the failure characteristic area and the analysis of fatigue sources and crack sources to provide sufficient criteria or counter-evidence for failure analysis. The most commonly used and common methods in microscopic analysis are optical metallographic analysis and surface hardness detection. The content of the analysis should include:
(1) Whether the material quality meets relevant standards and design requirements.
(2) Whether the basic structure and heat treatment quality of bearing parts meet relevant requirements.
(3) Whether there is decarburization layer, troostite and other surface processing deterioration layers in the surface structure.
(4) Measure the depth of the surface strengthening layer such as the carburized layer and the structure of each layer of the multi-layer metal, the shape and depth of the corrosion pit or crack, and determine the cause and nature of the crack based on the shape of the crack and the structural characteristics of both sides.
(5) Determine the degree of deformation, temperature rise, material type and process based on grain size, structural deformation, local phase transformation, recrystallization, phase aggregation, etc.
(6) Measure basic hardness, hardness uniformity and hardness changes in failure characteristic areas.
(7) Fracture observation and analysis. Qualitative analysis and measurement were performed to observe the fracture surface using scanning electron microscopy.
(8) Electron microscopes, probes and electron energy spectroscopy can measure the components of the fracture surface and discover the nature of the fracture surface and the cause of the fracture in the analysis of fatigue sources and crack sources.
The three steps of the general method of bearing failure analysis introduced above are a step-by-step and in-depth analysis process from the outside to the inside. The content included in each step should be selected based on the type and characteristics of the bearing failure and the specific circumstances, but the analysis steps are indispensable. over, throughout the entire analysis process, the analysis results should always be linked to the many factors that affect bearing failure and comprehensively considered.
Common failure modes and countermeasures of bearings
1. Peeling at the extreme position on one side of the channel. Peeling at the extreme position on one side of the channel is mainly manifested in severe spalling rings at the junction of the channel and the rib. The cause is that the bearing is not installed in place or there is a sudden axial overload during operation. The countermeasures to be taken are to ensure that the bearing is installed in place or to change the outer ring fit of the free side bearing to a clearance fit, so that the bearing can be compensated when the bearing is overloaded.
2. The channel peels off in a symmetrical position in the circumferential direction. The inner ring peels off in a symmetrical position around the circumference, while the outer ring peels off in a circumferentially symmetrical position (that is, the direction of the short axis of the ellipse). The main reason for this is that the shell hole is elliptical. Oversized or two-half split housing hole structure, which is particularly obvious in motorcycle camshaft bearings. When the bearing is pressed into the housing hole with a larger ellipse or the two halves of the separate housing are tightened, the outer ring of the bearing becomes elliptical, and the clearance in the short axis direction is significantly reduced or even negative. Under the action of load, the inner ring of the bearing will rotate and produce circumferential peeling marks, while the outer ring will only produce peeling marks at a symmetrical position in the short axis direction. This is the main reason for the early failure of the bearing. The inspection of the failed parts of the bearing shows that the outer diameter roundness of the bearing has changed from 0.8 μm controlled by the original process to 27 μm. This value is much larger than the radial clearance value. Therefore, it can be determined that the bearing is operating under severe deformation and negative clearance, and it is easy to cause abnormal and rapid wear and peeling on the working surface in the early stage. The countermeasures taken are to improve the processing accuracy of the housing hole or to avoid using the two-half separation structure of the housing hole as much as possible.
3. Inclined peeling of the raceway. An inclined peeling ring appears on the working surface of the bearing, indicating that the bearing is working in an inclined state. When the inclination angle reaches or exceeds a critical state, abnormal and rapid wear and peeling may occur early. The main reasons are poor installation, deflection of the shaft, low accuracy of the journal and housing hole, etc. Countermeasures are taken to ensure the quality of the bearing installation and improve the axial runout accuracy of the shaft shoulder and hole shoulder.
4. Ferrule breakage. Ferrule breakage failure is generally rare and is often caused by sudden overload. The causes are complex, such as bearing raw material defects (bubbles, shrinkage holes), forging defects (overburning), heat treatment defects (overheating), processing defects (local burns or surface microcracks), host defects (poor installation, poor lubrication, Instantaneous overload), etc. Once overloaded, impact load or severe vibration may cause the ferrule to break. Countermeasures are taken to avoid overload impact loads, select appropriate interference, improve installation accuracy, improve usage conditions and strengthen quality control in the bearing manufacturing process.
5. Cage fracture. Cage fracture is an sporadic abnormal failure mode. The main reasons are as follows:
a. Abnormal load on cage. If the installation is not in place, tilted, or the interference is too large, it will easily lead to a reduction in clearance, aggravated friction and heat generation, softening of the surface, and premature abnormal peeling. As the peeling expands, the peeling foreign matter will enter the cage pockets, causing the retention The operation of the cage is blocked and additional loads are generated, which aggravates the wear of the cage. Such worsening circulation may cause the cage to break.
b. Poor lubrication mainly means that the bearing is running in an oil-lean state, which is prone to adhesive wear, deteriorating the condition of the working surface, and the tears caused by adhesive wear can easily enter the cage, causing the cage to generate abnormal loads and possibly causing the cage to break.
c. The intrusion of foreign matter is a common mode of cage fracture failure. Due to the intrusion of foreign hard foreign matter, the wear of the cage is aggravated and abnormal additional loads are generated, which may also cause the cage to break.
d. Creep phenomenon is also one of the causes of cage fracture. The so-called creep phenomenon refers to the sliding phenomenon of ferrules. When the interference of the mating surface is insufficient, the load point moves in the peripheral direction due to sliding, causing the ferrule to deviate in the circumferential direction relative to the shaft or housing. Once creep occurs, the mating surface will wear significantly, and wear powder may enter the inside of the bearing, causing abnormal wear – raceway peeling – cage wear and additional load, which may even cause the cage to break.
e. Cage material defects (such as cracks, large foreign metal inclusions, shrinkage cavities, air bubbles) and riveting defects (missing nails, pad nails, gaps between the two cage halves, severe riveting damage), etc. may cause the cage to break. . The countermeasure is to strictly control the manufacturing process.
Conclusion
In summary, it can be seen from the common failure mechanisms and failure modes of bearings that although rolling bearings are precise and reliable structural foundations, improper use can also cause early failure. Generally speaking, if the bearings are used correctly, they can be used until their fatigue life. Early failure of bearings is mostly caused by factors such as the manufacturing accuracy of the host’s mating parts, installation quality, usage conditions, lubrication effect, intrusion of external foreign matter, thermal impact, and sudden failure of the host. Therefore, the correct and reasonable use of bearings is a systematic project. In the process of bearing structure design, manufacturing and installation, taking corresponding measures for the links that cause early failure can effectively improve the service life of the bearings and the main engine. This is the manufacturing The factory and the customer should bear joint responsibilities.