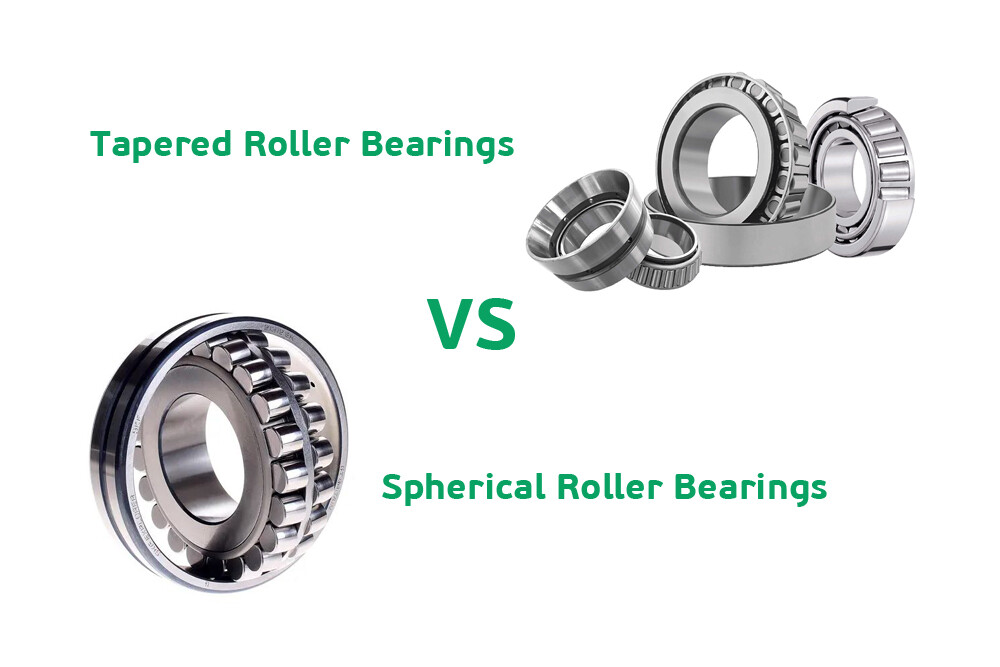
Bearing Manufacturer & Supplier
Specialize in ball bearings, roller bearings, thrust bearings, thin section bearings etc.
Tapered Roller Bearings or Spherical Roller Bearings?
A roller bearing is a rolling bearing that uses the rolling motion of rollers to support rotating parts. Roller bearings are an integral part of modern industrial machinery and play a pivotal role in a variety of applications. Roller bearings are favored for their low starting torque, high rotational accuracy and easy selection. The structure of roller bearings includes many types, such as tapered roller bearings, cylindrical roller bearings, spherical roller bearings and thrust roller bearings. They are able to withstand different types of radial and axial forces, and are designed with alignment performance in mind to adapt to complex installation conditions. This blog aims to clarify the differences between two key types of roller bearings: tapered bearings and spherical bearings. Help you understand the differences between them and provide constructive suggestions for making informed decisions in industrial applications.
Table of Contents
ToggleWhat are tapered roller bearings?
Tapered roller bearings have tapered rollers arranged between the inner and outer raceways. Tapered roller bearings are composed of inner rings, outer rings, rollers and cages. Corrected contact lines at the contact between rollers and raceways reduce stress concentrations. They converge at a common point on the bearing axis, ensuring optimal rolling conditions and effective distribution of load on the rollers. Tapered roller bearings are separate bearings. The inner and outer rings of the bearing have tapered raceways. This type of bearing is divided into different structural types such as single-row, double-row and four-row tapered roller bearings according to the number of rows of rollers installed. Single row tapered roller bearings can bear radial loads and axial loads in one direction. When the bearing is subjected to a radial load, an axial component force will be generated, so another bearing that can withstand the axial force in the opposite direction is needed to balance it.

On March 23, 1895, John Lincoln Scott, a farmer in Wilmot, Indiana, applied for a patent with the U.S. Patent Office for his invention of a roller bearing that could be mounted on “On the axles and hubs of trucks, four-wheelers, or other wheeled vehicles”.The bearing consists of two sets of cylindrical rollers, one set larger in diameter than the other, mounted on a flat surface machined on a tapered shaft winch. In 1898, Henry Timken patented a tapered roller bearing using tapered rollers. At the time, Timken was a St. Louis carriage manufacturer with three carriage spring patents. However, it was his patent for tapered roller bearings that made his company successful.
Advantages of tapered roller bearings
Large load-bearing capacity: Compared with other bearings, tapered roller bearings have a larger load-bearing capacity. This makes the bearing widely used in large mechanical equipment, such as wind power gearbox bearings.
High precision: Tapered roller bearings have high precision, and the inclination angles of the inner and outer rings can be set according to different use requirements, which is also one of the reasons for their popularity.
Automatic adjustment function: Due to the inclination angle of its inner and outer rings, tapered roller bearings can adapt to irregular movements in machinery and equipment, thereby reducing noise and losses caused by friction and vibration.

Handle axial and radial loads: Tapered roller bearings are good at handling axial (thrust) and radial loads, which is a unique feature brought about by their design. The arrangement of the tapered rollers allows them to effectively manage loads in multiple directions.
Good sealing: The internal design of the tapered roller bearing is very sealed, which can better protect the rollers and cages and reduce environmental pollution during use.
Long service life: Due to the advantages of tapered roller bearings such as large load-bearing capacity, high precision, automatic adjustment, and good sealing, they have a relatively long service life and high economic benefits.
Disadvantages of tapered roller bearings
Difficulty installation: Installing tapered roller bearings requires relatively high processing costs, especially in handling assembly. In many cases, professional knowledge and equipment are required, otherwise failures are easy to occur.
Higher cost: Because its manufacturing and processing require difficult technology and use materials, the cost of tapered roller bearings is relatively high.
Applications of tapered roller bearings
In many applications, tapered roller bearings are used in back-to-back pairs to support axial forces equally in either direction. Pairs of tapered roller bearings are used in automotive and wheel bearings where they must cope with both large vertical (radial) and horizontal (axial) forces. Tapered roller bearings are typically used in medium-speed, heavy-duty applications where durability is required. Common real-world applications include agricultural, construction, and mining equipment, motion robot combat, axle systems, gearboxes, engine motors and reducers, driveshafts, railway axleboxes, differentials, wind turbines, and . Tapered roller bearings are units composed of tapered raceways (inner and outer rings) and tapered rollers. This structure is suitable for combined loads, such as double-acting axial and radial loads. The bearing axis is where the projected lines of the raceway combine at a common location to improve rolling while reducing friction. The load capacity can be increased or decreased based on increasing or decreasing contact angle. The higher the angle, the greater the contact angle. They are often used in pairs to better handle radial loads and, in some heavy-duty applications, can be used in a combination of two or four rows in a single unit.

Application restrictions
Speed: Tapered roller bearings are not suitable for high speed applications due to their design.
Misalignment Sensitivity: They are sensitive to misalignment issues and require careful installation and maintenance.
Complexity of Installation and Removal: Due to their internal design, installation and removal of these bearings is complex than other types of bearings.
Tapered roller bearings play an important role in applications requiring high-precision heavy loads handling. However, understanding their applications is critical to ensuring they are used in appropriate applications, maximizing their efficiency and longevity.
What are spherical roller bearings?
Spherical roller bearings have double rows of rollers. The outer ring has a common spherical raceway, and the inner ring has two raceways that are inclined at an angle relative to the bearing axis. This ingenious structure makes it have self-aligning performance, so it is not easily affected by the angle of the shaft and the bearing housing or the shaft bending. It is suitable for occasions where installation errors or shaft deflection cause angle errors. When the shaft is bent due to force or the installation is not concentric, the bearing can still be used normally. The alignment performance varies with the bearing size series. The generally allowed alignment angle is 1 to 2.5 degrees, and it also has good impact resistance. In addition to radial loads, spherical roller bearings can also bear axial loads acting in both directions. There are two types of inner holes of spherical roller bearings: cylindrical and conical. The taper of the conical hole is 1:30 and 1:12. This kind of conical inner hole bearing is equipped with an adapter sleeve or a withdrawal sleeve. The tapered inner bore self-aligning ball bearing can be easily and quickly assembled on the shaft.

Advantages of spherical roller bearings
Self-aligning capability: An outstanding feature of spherical roller bearings is their self-aligning capability. This is due to the curvature of the outer ring raceway being aligned with the axis of rotation.
Misalignment tolerance: Spherical roller bearings can tolerate a certain degree of misalignment, compensating for errors in shaft deflection and alignment without affecting performance.
Large load-bearing capacity: Spherical roller bearings have a greater load-bearing capacity than other rolling bearings and can withstand higher loads and axial loads.
Long service life: The internal structure of spherical roller bearings is complex, but it can spread the load and reduce rolling friction, thereby extending the service life.
Strong adaptability: Spherical roller bearings can adapt to the rotation axis and installation errors, allowing them to adapt to different working environments and conditions.
Disadvantages of spherical roller bearings
High cost: The manufacturing of spherical roller bearings requires sophisticated process equipment and is costly, so careful consideration is needed in cost-sensitive applications.
Prone to axial load deflection: The axial load deflection of spherical roller bearings will cause early wear and failure of the bearings. Therefore, the installation and maintenance of the bearings need to be appropriately adjusted to avoid problems.
Not suitable for high-speed applications: When spherical roller ball bearings rotate at high speed, they will generate a lot of friction and heat, resulting in higher operating temperatures. This will not only affect the working efficiency of the machine, but also affect the life of the bearings. Therefore, when selecting spherical roller ball bearings, it is necessary to select appropriate specifications and models based on the actual working environment and load conditions to ensure the normal operation of the bearings.
Vibration and noise: The complexity of the spherical roller ball bearing structure determines that its noise and vibration will affect the normal operation of the machine and may also shorten the life of the bearing. In addition, vibration and noise may also have an impact on the operator of the machine, resulting in an unsafe or uncomfortable operating environment. In order to reduce the vibration and noise of spherical roller ball bearings, it is necessary to select high-quality bearings and perform reasonable adjustment and correction of the device.
Low energy efficiency: When rotating at high speed, spherical roller bearings need to consume a lot of energy to overcome friction. If the design and use of bearings are unreasonable, it will not only waste energy but also lead to low efficiency of the machine. Therefore, in order to improve the energy efficiency of spherical roller ball bearings, it is necessary to consider whether the bearing design and manufacturing process are reasonable, and take corresponding measures to improve the operating efficiency of the machine.
In summary, spherical roller bearings have unique advantages such as self-aligning and high load capacity, making them ideal for heavy-load and misalignment-prone applications. However, their restriction in speed, complexity, and size need to be considered to ensure they are selected for the appropriate use case.
Applications of spherical roller bearings
Mining equipment: They can withstand the extreme loads and impacts encountered by excavators, dump trucks and crushers.
Farm Machinery: Tractors, harvesters, and other heavy farm equipment rely on their durability and resistance to harsh environments.
Pulp Refiners: Their high load capacity and resistance to contamination are essential for efficient processing of fibrous materials.

Large industrial gearboxes: Their ability to handle combined radial and axial loads is critical to the power transmission of gearboxes in various industries.
Pulley systems: They adjust for misalignment in the belt drive, prevent wear and ensure efficient power transmission.
Tapered roller bearings vs spherical roller bearings
Understanding “Tapered Roller Bearings vs. Spherical Roller Bearings” is critical to selecting the correct bearing for a specific application. Here we compare these two types of roller bearings based on several key parameters.
Processing load
Tapered roller bearings: They are better at handling combined loads (radial and axial). The tapered design of the rollers effectively distributes load on the bearing, making it ideal for heavy-duty applications.
Spherical roller bearings: They are designed for high radial loads and moderate levels of axial loads.Their drum-shaped rollers make them suitable for applications where loading different directions.
Accuracy and alignment
Tapered Roller Bearings: This type of bearing is known for its accuracy and is suitable for applications that require high precision. However, they are sensitive to misalignment and require precise installation.
Spherical roller bearings: They offer self-aligning capabilities, making them forgiving in applications where shaft misalignment is possible. This feature reduces the risk of performance degradation due to alignment errors.
Application scope
Tapered roller bearings: suitable for automotive wheel bearings, transmissions and other applications where heavy combined loads are present.
Spherical roller bearings: Better suited for heavy machinery in mining and construction, wind turbines and applications where misalignment is likely to occur.
Maintenance requirements
Tapered roller bearings: require careful monitoring and precise alignment during installation and maintenance to ensure longevity and optimal performance.
Spherical roller bearings: While they can handle misalignment, regular maintenance is still critical to prevent premature wear caused by heavy loads and environmental factors.
Tapered roller bearings vs spherical roller bearings, which one?
Choosing the right bearing for any application depends on several key factors:
Key Factors to Consider | Tapered Roller Bearings | Spherical Roller Bearings |
Load Conditions | Ideal for high combined loads (radial and axial) in gearboxes, axles, etc. | Best suited for high radial loads with moderate axial loads in wind turbines, heavy machinery, etc. |
Cost and Maintenance | Lower initial cost but require precise mounting, increasing maintenance needs. | Higher initial cost but less maintenance-intensive due to their self-aligning features. |
Application Specifics | Consider environmental and space constraints for bearing size/design. | Consider bearing materials, sealing options, and consult manufacturers for specific load capacity, speed , and size. |
Additional | Consult bearing specialists for demanding applications and prioritize long-term reliability and safety over initial cost. | When unsure, prioritize higher load capacity and misalignment tolerance for critical applications. |
Misalignment | Highly sensitive to misalignment, even slight misalignment is prone to wear. | Accommodate some misalignment due to their design, forgiving in applications with potential shaft movement. |
Evaluate whether the applied load is radial, axial, or a combination of loads. For heavy combined loads, tapered roller bearings are ideal, while spherical roller bearings are suitable for high radial loads with axial load. In heavy industrial applications with high radial loads and misalignment, spherical roller bearings are often the best choice. For high-speed applications with high accuracy requirements and combined loads, tapered roller bearings are suitable.