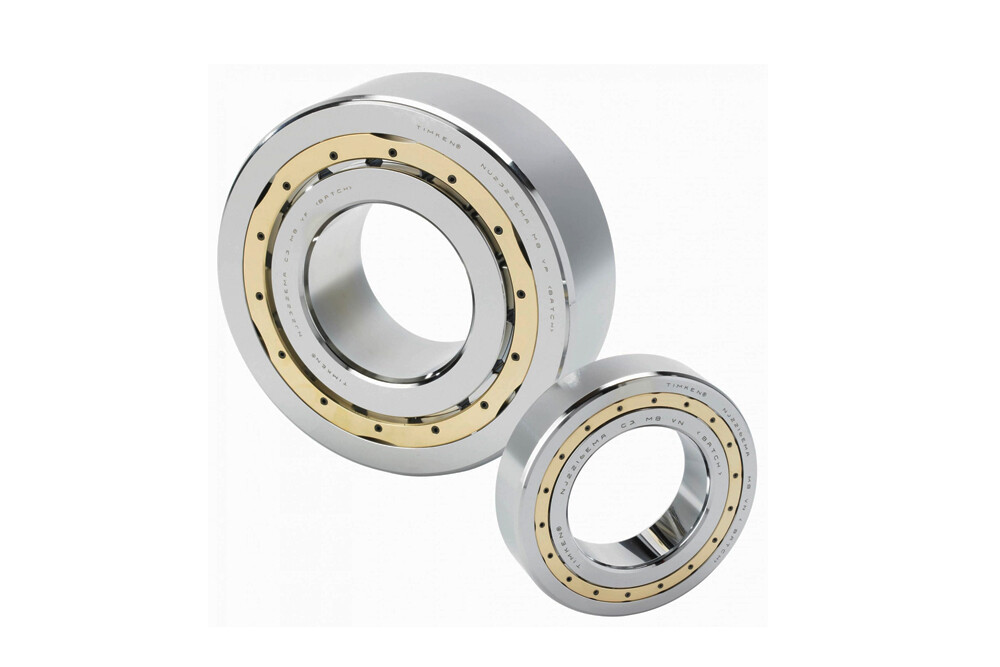
Bearing Manufacturer & Supplier
Specialize in ball bearings, roller bearings, thrust bearings, thin section bearings etc.
Guide to Selecting Cylindrical Roller Bearings
Cylindrical roller bearings are separate bearings that are very easy to install and disassemble. Cylindrical roller bearings allow the angular error (inclination) between the axis of the inner ring and the axis of the outer ring to be 2′ to 4′. Therefore, the machining accuracy of the shaft and bearing seat is relatively high, otherwise uneven loads or stress concentrations may easily occur at the raceway contact parts. However, the occurrence of stress concentration can be reduced by correcting the roller or raceway contact busbar. The cylindrical rollers are in line contact with the raceway and can withstand large radial loads. The friction between the rolling elements and the ring ribs is small, making it suitable for high-speed operation applications. There are thousands of variations of cylindrical roller bearings, and which model to choose depends on the specific application. Based on many years of manufacturing experience, Aubearing summarizes the guidelines for selecting cylindrical roller bearings.
Table of Contents
ToggleWhat are cylindrical roller bearings?
Cylindrical roller bearings consist of an inner ring, an outer ring, rollers and a cage, and use cylindrical rolling elements to replace the balls in ball bearings. The bearing rings and rollers carry the load, and the cage holds the rollers in place. Because cylindrical rollers are in linear contact with the raceway, they have a greater load capacity than ball bearings. Cylindrical roller bearings have high radial load capacity and moderate thrust load. Although rolling elements are cylindrical, they are not true cylinders. The rollers are crowned or have grooves on their ends, a geometry that reduces friction and allows for high-speed applications. Cylindrical roller bearings typically have an accuracy rating such as RBEC-5, which is the classification of the Roller Bearing Engineers Council (RBEC). RBEC grades describe the accuracy and tolerance ranges of different types of bearings. Generally, the higher the RBEC number, the tighter the bearing tolerances.

Cylindrical roller bearing materials
The inner and outer rings of most cylindrical roller bearings are made of chromium steel. Chromium steel 52100 has high and uniform hardness and wear resistance, as well as high elastic limit. The requirements for the uniformity of the chemical composition of bearing steel, the content and distribution of non-metallic inclusions, and the distribution of carbides are very strict. It is one of the most stringent steel types in all steel production. Generally, the cage of cylindrical roller bearings is made of steel or brass. However, you will also see molded polyamide cages, which make cylindrical roller bearings run smoother and quieter.

Types of cylindrical roller bearings
According to the number of rows of rollers, cylindrical roller bearings can be divided into single-row cylindrical roller bearings, double-row cylindrical roller bearings, full complement cylindrical roller bearings and four-row cylindrical roller bearings;
Single row cylindrical roller
Single row cylindrical rollers are popular release bearings and are easier to install and remove. However, they do not support heavy or excessive radial loads because they only bear axial loads in one direction and high rotational speeds. Single row cylindrical roller bearings can be divided into: NU type, NJ type, NUP type and N type design according to different rib structures;

N type – the outer ring has no ribs and the inner ring has no ribs, which allows the displacement of the shaft relative to the bearing seat in both axial directions.
NU type – double ribs on the outer ring and no ribs on the inner ring.
NJ type – double ribs on the outer ring and single rib on the inner ring. Therefore, these bearings are suitable for axial positioning of the shaft in one direction.
NF type – single rib on the outer ring and double ribs on the inner ring.
NUP type – double ribs on the outer ring, single rib on the inner ring and detachable flat ribs. These bearings can be used as positioning end bearings, providing axial positioning of the shaft in both directions.
NFP type – single rib on the outer ring and detachable flat ring, single rib on the inner ring.
Double row cylindrical roller bearings
Double row cylindrical roller bearings have compact structure, high load capacity and high rigidity. They can usually solve the problem of load capacity, spread the load to rollers, and can handle unstable loads or vibrations. They are especially suitable for machine tools. Spindle. In addition, a double-row bearing takes up less space in the bearing housing than placing two single-row bearings back to back and also optimizes load transfer between the two rows. Double row cylindrical roller bearings have two inner ring designs: cylindrical bore and tapered bore; according to their structure, there are two types: NNU type and NN type.

NN type bearings have no ribs on the outer ring, ribs on both sides of the inner ring and a middle rib in the middle. It allows axial displacement in two directions between the shaft and the bearing seat.The NNU type bearing has ribs on both sides of the outer ring and a middle rib in the middle, and the inner ring has no ribs. It allows axial displacement in two directions between the shaft and the bearing seat.
NNF type bearings consist of an outer ring with a middle rib and two inner rings with double ribs. The rollers are guided by the ribs of the inner ring, and the two inner rings are held together by a fastening ring. In addition to being able to withstand large radial loads and axial loads, this structure can also withstand overturning moments. Therefore, it is often used as a fixed-end bearing. NNF type bearings adopt contact seals on both sides. The bearing is filled with grease, and the operating temperature of the grease is -50°C to +110°C. However, due to the limitation of the sealing material, the operating temperature of the bearing is limited to -40°C to +80°C. Under good operating conditions, sealed NNF bearings do not require maintenance. If the bearing has been exposed to water vapor or polluted environment for a long time and is running at medium or high speed, it can be maintained through the lubricating oil groove and lubricating oil hole on the outer ring. Bearings are relubricated.
Four row cylindrical roller bearings
Four-row cylindrical roller bearings usually use surface-hardened carburized steel to improve wear resistance and impact load resistance. They can withstand greater radial loads and distribute the load to rollers. The cage of four-row cylindrical roller bearings usually uses machined brass cages or mild steel finger cages. However, larger size bearings use steel pin cages.

FC type bearings are composed of two outer rings and an inner ring. Each outer ring has ribs on both sides and a middle rib in the middle. The inner ring has no ribs.
FCD type bearings are actually composed of two NN type bearings.
FC type and FCD type bearings can allow axial displacement in two directions between the shaft and the bearing seat. Therefore, this type of structure is suitable for free end bearings.
Full complement cylindrical roller bearings are divided into two types: NCF type and NJG type, single row full complement cylindrical roller bearings, and double row full complement cylindrical roller bearings such as NNC type, NNCF type, NNCL type, and NNF type.
Why Selecting Cylindrical Roller Bearings?
From the simplest household appliances to the most complex industrial equipment, load capacity is critical for safe, reliable moving parts. Like ball bearings, the purpose of roller bearings is to minimize friction while carrying load, but instead of point contact, roller bearings have line contact. This gives them greater shock resistance and capacity. For cylindrical roller bearings, the external load is distributed on the cylindrical rollers with greater load-bearing capacity, which helps to extend the service life of the machinery.
1. High load-bearing capacity: Cylindrical roller bearings adopt a roller structure and can withstand high radial and axial loads, and are suitable for high-load rotating bodies.
2. Lower friction coefficient: Because the rolling contact area of cylindrical roller bearings is large and the friction coefficient is low, it has good lubrication performance and low friction resistance, which can effectively reduce mechanical energy consumption and wear.
3. High rotation accuracy: Cylindrical roller bearings adopt precise processing technology and have high rotation accuracy, which can ensure the stability and accuracy of mechanical equipment.
4. Better durability: Cylindrical roller bearings use high-quality materials and advanced heat treatment technology, which have good durability and long service life.
5. Better adaptability: Cylindrical roller bearings can choose different designs, materials and sizes according to different application requirements, and have strong adaptability and flexibility.
6. Lower maintenance costs: Cylindrical roller bearings have low maintenance costs and only require regular lubrication and inspection to ensure their normal operation.
Cylindrical roller bearing selection criteria
There are several criteria to consider when selecting a cylindrical roller bearing. For example, size, operating speed and load specifications, unique installation features, and material selection must be considered.
Size
Bore size and outside diameter (OD) are the most important factors to consider when selecting a cylindrical roller bearing, as this determines whether the bearing will fit in place. There are industry standards for bore diameters in metric cylindrical roller bearings. For bore sizes 04 and above, multiply the bore size by 5 to determine the bore diameter in millimeters (mm). It is worth noting that when manufacturers indicate the outer diameter, they include the bearing seat (if any) but not the flange.
Specification
Selecting the correct bearing requires consideration of support for axial loads in one direction (single row) or both directions (double row) and load parameters, which include:
Rated speed
Static axial or thrust load
Static radial load
Dynamic axial or thrust loads
dynamic radial load
unique features
Static axial load and static radial load are respectively the maximum axial load and radial load that the bearing can bear in the delicate state. Dynamic axial load and dynamic radial load are respectively the amount of load the inner ring is rated to withstand at 1 million revolutions. Cylindrical roller bearing clearance and lubrication options vary by manufacturer.
Certain applications require thoroughly hardened, high-carbon bearing-quality steel that is durable than typical alloy or mild steel bearings. Additionally, material processing can add carbon and alloys to mild steel. The process produces a fatigue-resistant shell and a rigid, forgeable core that improves bending fatigue to withstand heavy impact loads.
Application
Cylindrical roller bearings have greater radial load capacity, the ability to adapt to faster speeds, and other advantages, making them an ideal solution for a variety of industries, including: large and medium-sized electric motors, rolling stock, machine tool spindles, internal combustion engines, generators, gas Turbines, reduction gearboxes, rolling mills, vibrating screens and lifting and transportation machinery, etc.
Conclusion
At Aubearing, we understand that choosing the right roller bearing is crucial to ensuring optimal performance of your machinery. Aubearing’s experienced and knowledgeable team is ready to help you determine the best roller bearing for your specific application, ensuring reliability and longevity. Our commitment to customer satisfaction goes beyond providing quality products to include personalized guidance, technical expertise, and dedication to meeting your unique needs.