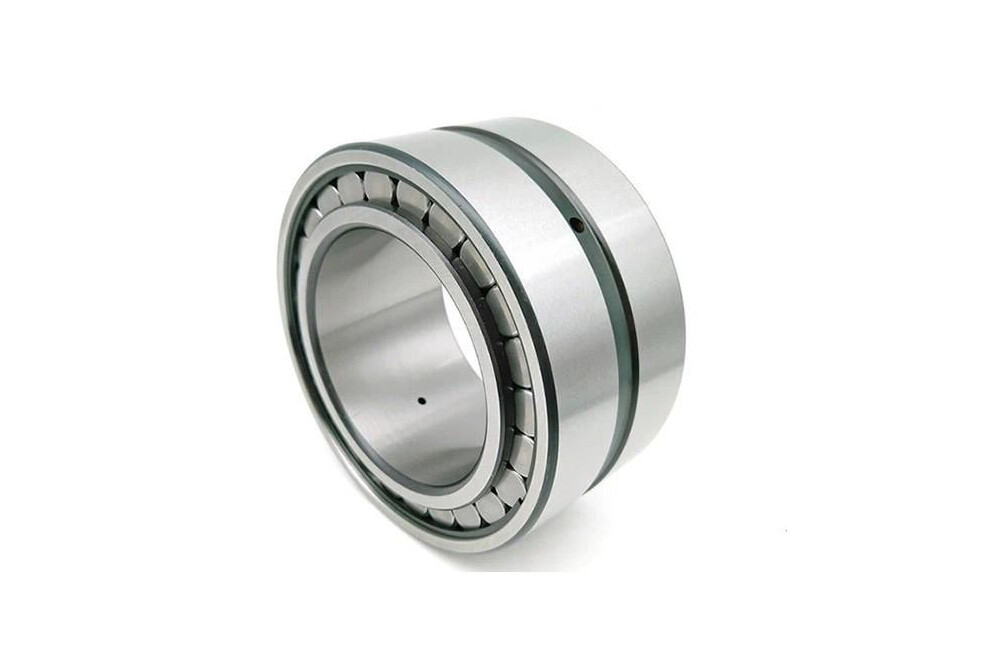
Bearing Manufacturer & Supplier
Specialize in ball bearings, roller bearings, thrust bearings, thin section bearings etc.
Guide to Full Complement Cylindrical Roller Bearings
As the bearing market continues to develop in recent years, full complement cylindrical roller bearings, as one of the important types, also have broad application prospects. With the continuous growth of the world economy and the upgrading of the manufacturing industry, the demand for full complement cylindrical roller bearings will also continue to increase. At the same time, with the application and promotion of new technologies such as intelligent manufacturing and green manufacturing, full complement cylindrical roller bearings will also face new development opportunities and challenges. This guide aims to introduce the types, materials, applications, installation and other information of full complement cylindrical roller bearings, and provide constructive suggestions for you to fully understand it.
Table of Contents
ToggleWhat are full complement cylindrical roller bearings?
Full complement cylindrical roller bearings are a further improved version of cylindrical roller bearings that contain as many rollers as possible, but these rollers are not equipped with cages like other row versions with multiple rollers. The bearing is assembled from a solid outer ring, inner ring and rolling element set. Since the design does not accommodate a cage, the bearing can accommodate a maximum number of rolling elements. Full complement cylindrical roller bearings are designed to carry heavy loads. Under the same width, compared with traditional bearings with cages, full complement cylindrical roller bearings have extremely high load-bearing capacity and small radial cross-section, which can save space, but the rotation speed is relatively low. Under continuous operation, full complement cylindrical roller bearings must bear a small load, that is, C/P<25. Otherwise, wear will be aggravated due to insufficient lubrication and high-speed operation. All multi-row cylindrical roller bearings have a lubrication groove and lubrication hole on the outer ring.

At the same time, since this type of bearing does not have cage guidance and roller isolation measures, relative slip will occur between the rollers. Therefore, compared with ordinary cylindrical roller bearings, its rotation speed is lower and the noise is larger. Each of these rollers needs to have a slight lateral curvature at the end. These profiled ends reduce damaging edge stresses that can occur between raceways and rolling elements. These cylindrical roller bearings are also radial roller bearings. Its main features are:
Able to withstand particularly high radial loads
The bearing surface has high rigidity
Compact and space-saving design easy to install
Full complement cylindrical roller bearing structure
Full complement cylindrical roller bearings have many structural changes due to different uses and adaptability to working environments, but the basic structure consists of three parts: inner ring, outer ring, and rolling elements (rollers). Another special type of full complement bearing without outer ring has one less outer ring than the normal structure, and considering the convenience of transportation and installation, the outer ring is usually replaced by a plastic shell. After it is officially installed on the machine, the shell can be discarded.
(1) Inner ring: Usually fixed on the journal, the inner ring rotates with the shaft. The outer surface of the inner ring has some grooves for roller rolling, called inner grooves or inner raceways.
(2) Outer ring: It is usually fixed on the bearing seat or casing of the machine to support the rolling elements. There are also grooves on the inner surface of the outer ring for rolling steel balls or rollers, called inner grooves or inner raceways.
(3) Rolling elements: Each set of bearings is equipped with one or several sets of rolling elements, which are installed between the inner ring and the outer ring to transmit rolling force. Rolling elements are load-bearing components, and their shape, size and number determine the high-speed running performance of the bearing’s load-bearing capacity.
Different series of full complement bearings also have other matching options. For example, dust cover, sealing ring, stop washer, etc. For example, SL04502PP is a full complement cylindrical roller bearing with a circlip groove seal ring.
Materials for full complement cylindrical roller bearings
The choice of materials used in the manufacture of cylindrical roller bearings depends on their ability to withstand physical stresses, environmental conditions and the specific requirements of their intended use. They are usually made of chromium-manganese high carbon steel (resistant to pitting corrosion). Commonly used materials are GCr15 bearing steel, GCr15SiMn bearing steel, GCr6 bearing steel, GCr9 bearing steel, stainless steel, etc. The hardness after quenching is between 61HRC-65HRC.
GCr15 bearing steel
GCr15 bearing steel is a high-carbon chromium bearing steel with low alloy content, good performance and the most widely used. After quenching and tempering, the hardness is high and uniform, the wear resistance is good, and the contact fatigue performance is high. The steel has moderate cold working plasticity, average cutting properties, poor welding properties, high sensitivity to white spot formation and temper brittleness. GCr15 bearing steel, containing c0.95-1.05, Mn0.25-0.45, Si0.15-0.35.GCr15 bearing steel performed well overall. The cutting performance after spheroidizing annealing is good. After quenching and tempering, the hardness is high and uniform, and the wear resistance and contact fatigue strength are high. Good heat treatability, contains fewer alloying elements, and is relatively cheap.
GCr15SiMn bearing steel
GCr15SiMn has higher wear resistance and hardenability than GCr15, moderate cold working plastic deformation, poor weldability, is sensitive to white spot formation, and has temper brittleness during heat treatment. Used to manufacture sealing washers with wall thickness > 12mm and outer diameter ≥ 250mm; steel balls with a diameter of 50.8-203.2 and rollers with a diameter > 22mm; in addition, it can also be used as other mechanical parts requiring high hardness and wear resistance , such as rollers, spiral gauges, etc.
GCr15SiMn is a high-carbon, high-chromium bearing steel with higher wear resistance and hardenability than GCr15 steel. The critical quenching diameter in oil is 90~110mm (volume fraction is 50% martensite). After the oil is quenched at 840°C, tempered at 350°C, and then lightly quenched, the surface hardness is as high as 1096HV, and the depth of the hardened layer can reach 1mm. In view of the insufficient heat treatment process of the forming roll, pre-cooling at the thin edge to generate perovskite or sorbite allows for non-martensitic phase transformation, which can enhance toughness, reduce stress, and then quench the entire body. Ice treatment can improve the dimensional stability of the bearing, or stabilize the retained austenite and obtain high dimensional stability and high toughness through martensitic gradient quenching.
Stainless steel
For applications requiring corrosion resistance, such as in the food processing or chemical industry, stainless steel cylindrical roller bearings are preferred. Stainless steel has good corrosion resistance while maintaining high strength and wear resistance. Has good wear resistance and is suitable for high speed applications.
Some cylindrical roller bearings include seals or guards to prevent contaminants from entering and maintain lubrication:
Rubber seals: Typically made of nitrile rubber or silicone rubber, they are chosen for their elasticity, wear resistance, and compatibility with a variety of lubricants.
Metal Shields: Typically made of stamped steel, these shields create a physical barrier against contaminants.
Full complement cylindrical roller bearings can be divided into single row and double row according to the number of rows of rolling elements. The two most famous brands in the world are SKF and INA. At present, the quality of full complement cylindrical roller bearings made in China is comparable to these two brands, and the price is only one-tenth or even lower than them, and they are becoming and popular.
Single row full complement cylindrical roller bearings are designed to carry extremely high axial and radial loads and are designed with a maximum number of rollers and no cage. Full complement cylindrical roller bearings generally run at lower speeds than bearings with cages. Typical series of single row full complement cylindrical roller bearings manufactured by Aubearing: NCF and NJG. They are manufactured with normal radial internal clearance (CN), but are also available with C2, C3, C4 and C5 radial clearances.
Double row full complement cylindrical roller bearings
Double row full complement cylindrical roller bearings have solid inner and outer rings and correctly guided rolling elements between ribs. Due to their cageless design, they can carry rollers, resulting in higher load ratings. The most typical series of double row full complement cylindrical roller bearings: NNC, NNCL, NNF, NNCF.
Full complement cylindrical roller bearings are used in many industries, such as lathes, CNC machining centers, milling machines, boring machines and other mechanical equipment. These bearings can withstand extremely high loads and maintain excellent performance at low to medium speeds. In addition, depending on the design and structure, full complement cylindrical roller bearings also have different applications. For example, unsealed single-row and double-row bearings are mainly used in gearbox mechanisms, while sealed double-row bearings are suitable for lifting mechanisms. Here are some common industry applications:
1. Mechanical engineering: Full complement cylindrical roller bearings are widely used in industrial machinery, construction machinery, metallurgical machinery, etc. For example, used in cranes, machine tools, conveyor belts and other equipment.
2. Railway industry: Full complement cylindrical roller bearings play an important role in key parts such as wheel sets, axle boxes and body joints of railway vehicles. They can withstand high loads and strong impacts, ensuring the safety and smooth operation of trains.
3. Electric power industry: Full complement cylindrical roller bearings are widely used in the electric power industry. For example, they are used in bearing boxes of power plants, hydroelectric generator sets, wind turbines and other equipment.
4. Oil and natural gas industry: Full complement cylindrical roller bearings are widely used in oil and natural gas extraction equipment such as oil well drilling rigs, oil transfer pumps, and centrifuges. They can withstand high temperatures, high pressures and harsh working environments.
5. Chemical industry: Full complement cylindrical roller bearings are also commonly used in chemical equipment, such as centrifuges, mixers, compressors and other equipment. They maintain good performance under chemical corrosion and high-speed operating conditions.
6. Food and beverage industry: Full complement cylindrical roller bearings are widely used in food and beverage processing equipment, including use in mixers, conveyor belts, grinders and other equipment. These bearings usually need to meet hygiene standards and be corrosion-resistant and easy to clean.
7. Textile industry: Full complement cylindrical roller bearings are often used in spindles, rollers and other parts of textile equipment. They can withstand high-speed rotation and frequent undulating loads, ensuring the smooth operation of textile machinery.
8. Agricultural machinery: Full complement cylindrical roller bearings are also widely used in agricultural machinery, such as tractors, harvesters, sprinkler irrigation equipment, etc. They are able to withstand heavy loads and vibrations in agricultural operations, ensuring the reliability and durability of machinery.
In addition, full complement cylindrical roller bearings are also used in many fields such as mining, shipbuilding industry, and metallurgical industry. Their high load-bearing capacity and performance advantages make them an important component of many critical equipment and mechanical systems.