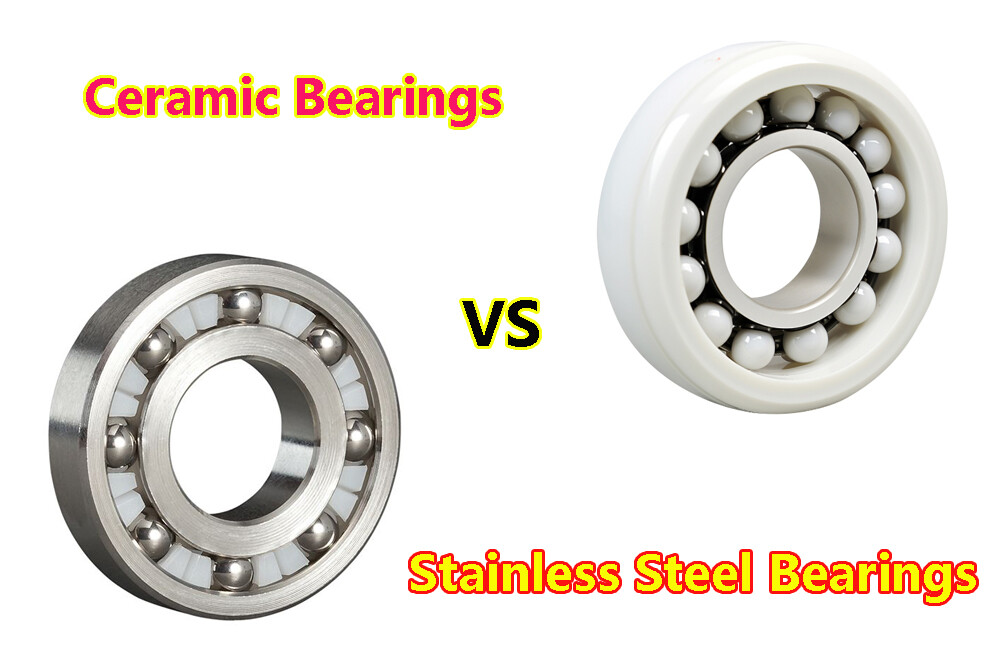
Bearing Manufacturer & Supplier
Specialize in ball bearings, roller bearings, thrust bearings, thin section bearings etc.
Ceramic Bearings VS Stainless Steel Bearings, Which One?
Bearings are important components in many machines and equipment, used to reduce friction at contact surfaces, support loads, smooth motion and extend the life of moving parts. Bearings are divided into many types, including sliding bearings, linear bearings, roller bearings, ball bearings, etc. You can also classify them based on the two main types of raw materials used to make bearings: ceramic bearings vs stainless steel bearings. Ceramic ball bearings and steel ball bearings are very similar in design. The contact points, internal and external dimensions, and thickness of stainless steel ball bearings and ceramic ball bearings are the same. The only obvious difference in design is the ball’s material – ceramic or stainless steel. The most significant differences between these two types are their performance and longevity. In this blog, we will delve into the differences between ceramic bearings vs stainless steel bearings and the pros and cons of each. I hope you can have a better understanding of the characteristics of these two types of bearings.
Table of Contents
ToggleWhat are ceramic bearings?
Ceramics can be used in the manufacture of bearings due to their various properties, especially resistance to corrosion and high temperatures. Ceramics are inert and non-conductive, while stainless steel is reactive and conductive, which makes ceramics resistant to corrosive materials such as seawater and many chemicals, including acids and alkalis. Because ceramic bearings do not corrode, they require less maintenance than stainless steel bearings and can be used in highly harsh environments. Not surprisingly, these corrosion-resistant properties make ceramic bearings useful in many industries, from food and chemical production to marine and underwater applications. The first ceramic bearings were designed in the United States as early as the 1960s and 1970s. Today, ceramic bearings are used in industrial fields such as aerospace, medical, and automotive, as well as in high-value everyday applications such as air conditioners, skateboards, and bicycles. Especially today, new developments in electric vehicles mean that ceramic bearings are becoming and popular. Depending on the materials used, ceramic bearings can be divided into full ceramic bearings and hybrid ceramic bearings.
Full ceramic bearings
Fully ceramic bearings have ceramic rings and balls and a synthetic cage made of PEEK or PTFE or no cage at all. They are highly resistant to acids and alkalis, making them suitable for use in very corrosive environments. Silicon nitride (Si3N4) bearings can be heated to 800 degrees Celsius without a cage. Combining these qualities with their lightweight nature, they weigh only 45% of stainless steel bearings, making them an incredible alternative to traditional stainless steel bearings. Full ceramic bearings are also non-magnetic, meaning they can be used in medical equipment such as MRI scanners, or any application where strong magnetic fields are present. However, the harder ceramic bearings also mean they are brittle, so they do not withstand shock loads well.

– Zirconia is the most commonly used ceramic bearing material. It has excellent electromagnetic resistance, wear resistance, corrosion resistance, lubricity and maintenance-free properties.
– The cage is usually polytetrafluoroethylene (PTFE) or polyetheretherketone (PEEK).

Part Number | Seal Type | Bore Dia | Outer Dia | Width | Ring Material | Dynamic Radial Load | Static Radial Load | Max Speed (X1000 rpm) |
CE6215ZRPP | Sealed | 75 mm | 130 mm | 25 mm | Zirconia | 20220 N | 14490 N | 2.24 |
CE6216ZR | Open | 80 mm | 140 mm | 26 mm | Zirconia | 21810 N | 15900 N | 3.15 |
CE6216ZRPP | Sealed | 80 mm | 140 mm | 26 mm | Zirconia | 21810 N | 15900 N | 2.1 |
CE6217ZR | Open | 85 mm | 150 mm | 28 mm | Zirconia | 25200 N | 18570 N | 3.01 |
CE6217ZRPP | Sealed | 85 mm | 150 mm | 28 mm | Zirconia | 25200 N | 18570 N | 1.96 |
CE6218ZR | Open | 90 mm | 160 mm | 30 mm | Zirconia | 28830 N | 21450 N | 2.8 |
CE6218ZRPP | Sealed | 90 mm | 160 mm | 30 mm | Zirconia | 28830 N | 21450 N | 1.82 |
CE6219ZR | Open | 95 mm | 170 mm | 32 mm | Zirconia | 32700 N | 24570 N | 2.66 |
CE6219ZRPP | Sealed | 95 mm | 170 mm | 32 mm | Zirconia | 32700 N | 24570 N | 1.82 |
CE62200ZRPP | Sealed | 10 mm | 30 mm | 14 mm | Zirconia | 1800 N | 720 N | 20.3 |
CE62201ZRPP | Sealed | 12 mm | 32 mm | 14 mm | Zirconia | 2070 N | 930 N | 18.2 |
CE62202ZRPP | Sealed | 15 mm | 35 mm | 14 mm | Zirconia | 2340 N | 1140 N | 15.4 |
CE62203ZRPP | Sealed | 17 mm | 40 mm | 16 mm | Zirconia | 2880 N | 1440 N | 14 |
CE62204ZRPP | Sealed | 20 mm | 47 mm | 18 mm | Zirconia | 3810 N | 1980 N | 12.6 |
CE62205ZRPP | Sealed | 25 mm | 52 mm | 18 mm | Zirconia | 4200 N | 2340 N | 10.5 |
CE62206ZRPP | Sealed | 30 mm | 62 mm | 20 mm | Zirconia | 5850 N | 3360 N | 9.1 |
CE62207ZRPP | Sealed | 35 mm | 72 mm | 23 mm | Zirconia | 7650 N | 4590 N | 8.4 |
CE62208ZRPP | Sealed | 40 mm | 80 mm | 23 mm | Zirconia | 9210 N | 5700 N | 7 |
CE62209ZRPP | Sealed | 45 mm | 85 mm | 23 mm | Zirconia | 9960 N | 6480 N | 6.44 |
CE6220ZR | Open | 100 mm | 180 mm | 34 mm | Zirconia | 36600 N | 27930 N | 2.52 |
CE6220ZRPP | Sealed | 100 mm | 180 mm | 34 mm | Zirconia | 36600 N | 27930 N | 1.68 |
CE62210ZRPP | Sealed | 50 mm | 90 mm | 23 mm | Zirconia | 10530 N | 6960 N | 5.95 |
CE62211ZRPP | Sealed | 55 mm | 100 mm | 25 mm | Zirconia | 13080 N | 8700 N | 5.46 |
CE62212ZRPP | Sealed | 60 mm | 110 mm | 28 mm | Zirconia | 15810 N | 10800 N | 5.25 |
CE62213ZRPP | Sealed | 65 mm | 120 mm | 31 mm | Zirconia | 16770 N | 12150 N | 5.04 |
CE62214ZRPP | Sealed | 70 mm | 125 mm | 31 mm | Zirconia | 18150 N | 13650 N | 4.69 |
CE6221ZR | Open | 105 mm | 190 mm | 36 mm | Zirconia | 39900 N | 31500 N | 2.45 |
CE6221ZRPP | Sealed | 105 mm | 190 mm | 36 mm | Zirconia | 39900 N | 31500 N | 1.54 |
CE6222ZR | Open | 110 mm | 200 mm | 38 mm | Zirconia | 45300 N | 35400 N | 3.01 |
CE6222ZRPP | Sealed | 110 mm | 200 mm | 38 mm | Zirconia | 45300 N | 35400 N | 1.4 |
CE6224ZR | Open | 120 mm | 215 mm | 40 mm | Zirconia | 43800 N | 35400 N | 2.8 |
CE6224ZRPP | Sealed | 120 mm | 215 mm | 40 mm | Zirconia | 43800 N | 35400 N | 1.33 |
CE6226ZR | Open | 130 mm | 230 mm | 40 mm | Zirconia | 46800 N | 39600 N | 2.52 |
CE6226ZRPP | Sealed | 130 mm | 230 mm | 40 mm | Zirconia | 46800 N | 39600 N | 1.26 |
CE6228ZR | Open | 140 mm | 250 mm | 42 mm | Zirconia | 49500 N | 45000 N | 2.38 |
CE62300ZRPP | Sealed | 10 mm | 35 mm | 17 mm | Zirconia | 2430 N | 1020 N | 18.2 |
CE62301ZRPP | Sealed | 12 mm | 37 mm | 17 mm | Zirconia | 2940 N | 1260 N | 16.1 |
CE62302ZRPP | Sealed | 15 mm | 42 mm | 17 mm | Zirconia | 3420 N | 1620 N | 13.3 |
CE62303ZRPP | Sealed | 17 mm | 47 mm | 19 mm | Zirconia | 4050 N | 1980 N | 12.6 |
CE62304ZRPP | Sealed | 20 mm | 52 mm | 21 mm | Zirconia | 4770 N | 2340 N | 11.9 |
CE62305ZRPP | Sealed | 25 mm | 62 mm | 24 mm | Zirconia | 6750 N | 3480 N | 9.8 |
CE62306ZRPP | Sealed | 30 mm | 72 mm | 27 mm | Zirconia | 8430 N | 4800 N | 9.1 |
CE62307ZRPP | Sealed | 35 mm | 80 mm | 31 mm | Zirconia | 9960 N | 5700 N | 8.4 |
CE62308ZRPP | Sealed | 40 mm | 90 mm | 33 mm | Zirconia | 12300 N | 7200 N | 7.7 |
CE62309ZRPP | Sealed | 45 mm | 100 mm | 36 mm | Zirconia | 15810 N | 9450 N | 6.79 |
CE6230ZR | Open | 150 mm | 270 mm | 45 mm | Zirconia | 52200 N | 49800 N | 2.24 |
CE62310ZRPP | Sealed | 50 mm | 110 mm | 40 mm | Zirconia | 18540 N | 11400 N | 6.44 |
CE62311ZRPP | Sealed | 55 mm | 120 mm | 43 mm | Zirconia | 21450 N | 13500 N | 6.02 |
CE62312ZRPP | Sealed | 60 mm | 130 mm | 46 mm | Zirconia | 24540 N | 15570 N | 5.67 |
CE6232ZR | Open | 160 mm | 290 mm | 48 mm | Zirconia | 55800 N | 55800 N | 2.1 |
CE6234ZR | Open | 170 mm | 310 mm | 52 mm | Zirconia | 63600 N | 67200 N | 1.96 |
CE6236 MZR | Open | 180 mm | 320 mm | 52 mm | Zirconia | 68700 N | 72000 N | 2.66 |
CE6238ZR | Open | 190 mm | 340 mm | 55 mm | Zirconia | 76500 N | 84000 N | 1.68 |
CE623ZR | Open | 3 mm | 10 mm | 4 mm | Zirconia | 161 N | 52 N | 35 |
CE623ZRPP | Sealed | 3 mm | 10 mm | 4 mm | Zirconia | 161 N | 52 N | 35 |
CE6240 MZR | Open | 200 mm | 360 mm | 58 mm | Zirconia | 81000 N | 93000 N | 2.24 |
CE6244 MZR | Open | 220 mm | 400 mm | 65 mm | Zirconia | 88800 N | 109500 N | 2.1 |
CE6248 MZR | Open | 240 mm | 440 mm | 72 mm | Zirconia | 107400 N | 139500 N | 1.82 |
CE624ZR | Open | 4 mm | 13 mm | 5 mm | Zirconia | 332 N | 117 N | 28 |
CE624ZRPP | Sealed | 4 mm | 13 mm | 5 mm | Zirconia | 332 N | 117 N | 28 |
CE6252 MZR | Open | 260 mm | 480 mm | 80 mm | Zirconia | 117000 N | 159000 N | 1.68 |
CE6256 MZR | Open | 280 mm | 500 mm | 80 mm | Zirconia | 126900 N | 180000 N | 1.54 |
CE625ZR | Open | 5 mm | 16 mm | 5 mm | Zirconia | 441 N | 162 N | 25.2 |
CE625ZRPP | Sealed | 5 mm | 16 mm | 5 mm | Zirconia | 441 N | 162 N | 25.2 |
CE6260 MZR | Open | 300 mm | 540 mm | 85 mm | Zirconia | 138600 N | 201000 N | 1.4 |
CE626ZR | Open | 6 mm | 19 mm | 6 mm | Zirconia | 596 N | 215 N | 22.4 |
CE626ZRPP | Sealed | 6 mm | 19 mm | 6 mm | Zirconia | 596 N | 215 N | 22.4 |
CE627ZR | Open | 7 mm | 22 mm | 7 mm | Zirconia | 838 N | 331 N | 21 |
CE627ZRPP | Sealed | 7 mm | 22 mm | 7 mm | Zirconia | 838 N | 331 N | 21 |
CE628ZR | Open | 8 mm | 24 mm | 8 mm | Zirconia | 850 N | 341 N | 19.6 |
CE628ZRPP | Sealed | 8 mm | 24 mm | 8 mm | Zirconia | 850 N | 341 N | 19.6 |
CE629ZR | Open | 9 mm | 26 mm | 8 mm | Zirconia | 1164 N | 476 N | 19.6 |
CE629ZRPP | Sealed | 9 mm | 26 mm | 8 mm | Zirconia | 1164 N | 476 N | 19.6 |
CE63000ZRPP | Sealed | 10 mm | 26 mm | 12 mm | Zirconia | 1380 N | 600 N | 23.1 |
CE63001ZRPP | Sealed | 12 mm | 28 mm | 12 mm | Zirconia | 1530 N | 720 N | 20.3 |
CE63002ZRPP | Sealed | 15 mm | 32 mm | 13 mm | Zirconia | 1680 N | 840 N | 17.5 |
CE63003ZRPP | Sealed | 17 mm | 35 mm | 14 mm | Zirconia | 1800 N | 990 N | 16.1 |
CE63004ZRPP | Sealed | 20 mm | 42 mm | 16 mm | Zirconia | 2820 N | 1500 N | 14 |
CE63005ZRPP | Sealed | 25 mm | 47 mm | 16 mm | Zirconia | 3030 N | 1740 N | 11.9 |
CE63006ZRPP | Sealed | 30 mm | 55 mm | 19 mm | Zirconia | 3960 N | 2490 N | 10.5 |
CE63007ZRPP | Sealed | 35 mm | 62 mm | 20 mm | Zirconia | 4800 N | 3090 N | 9.8 |
CE63008ZRPP | Sealed | 40 mm | 68 mm | 21 mm | Zirconia | 5040 N | 3480 N | 8.4 |
CE6300ZR | Open | 10 mm | 35 mm | 11 mm | Zirconia | 2430 N | 1035 N | 15.4 |
CE6300ZRPP | Sealed | 10 mm | 35 mm | 11 mm | Zirconia | 2430 N | 1035 N | 15.4 |
CE6301ZR | Open | 12 mm | 37 mm | 12 mm | Zirconia | 2910 N | 1260 N | 14 |
CE6301ZRPP | Sealed | 12 mm | 37 mm | 12 mm | Zirconia | 2910 N | 1260 N | 14 |
CE6302ZR | Open | 15 mm | 42 mm | 13 mm | Zirconia | 3420 N | 1635 N | 11.9 |
CE6302ZRPP | Sealed | 15 mm | 42 mm | 13 mm | Zirconia | 3420 N | 1635 N | 11.9 |
CE6303ZR | Open | 17 mm | 47 mm | 14 mm | Zirconia | 4080 N | 1995 N | 10.5 |
CE6303ZRPP | Sealed | 17 mm | 47 mm | 14 mm | Zirconia | 4080 N | 1995 N | 10.5 |
CE6304ZR | Open | 20 mm | 52 mm | 15 mm | Zirconia | 4770 N | 2355 N | 9.8 |
CE6304ZRPP | Sealed | 20 mm | 52 mm | 15 mm | Zirconia | 4770 N | 2355 N | 9.8 |
CE6305ZR | Open | 25 mm | 62 mm | 17 mm | Zirconia | 6180 N | 3390 N | 7.7 |
CE6305ZRPP | Sealed | 25 mm | 62 mm | 17 mm | Zirconia | 6180 N | 3390 N | 7.7 |
CE6306ZR | Open | 30 mm | 72 mm | 19 mm | Zirconia | 8010 N | 4500 N | 6.72 |
CE6306ZRPP | Sealed | 30 mm | 72 mm | 19 mm | Zirconia | 8010 N | 4500 N | 6.72 |
CE6307ZR | Open | 35 mm | 80 mm | 21 mm | Zirconia | 10020 N | 5790 N | 5.95 |
CE6307ZRPP | Sealed | 35 mm | 80 mm | 21 mm | Zirconia | 10020 N | 5790 N | 5.95 |
CE6308ZR | Open | 40 mm | 90 mm | 23 mm | Zirconia | 12210 N | 7200 N | 5.25 |
CE6308ZRPP | Sealed | 40 mm | 90 mm | 23 mm | Zirconia | 12210 N | 7200 N | 5.25 |
– Compared with ZrO2, Si3N4 ceramic bearings can withstand higher loads and are suitable for use in high temperature environments. In addition, the rotation speed of silicon nitride bearings is also very high.
– Cage is usually PTFE or PEEK.

Part Number | Seal Type | Bore Dia | Outer Dia | Width | Ring Material | Cage Material | Dynamic Radial Load | Static Radial Load | Maximum Temperature |
63800 | Open | 10 mm | 19 mm | 7 mm | Silicon Nitride | PEEK | 430 N | 210 N | 800 C (1472F) |
63800 2rs | Sealed | 10 mm | 19 mm | 7 mm | Silicon Nitride | PEEK | 430 N | 210 N | 800 C (1472F) |
63801 | Open | 12 mm | 21 mm | 7 mm | Silicon Nitride | PEEK | 480 N | 260 N | 800 C (1472F) |
63801 2rs | Sealed | 12 mm | 21 mm | 7 mm | Silicon Nitride | PEEK | 480 N | 260 N | 800 C (1472F) |
63802 | Open | 15 mm | 24 mm | 7 mm | Silicon Nitride | PEEK | 518 N | 315 N | 800 C (1472F) |
63802 2rs | Sealed | 15 mm | 24 mm | 7 mm | Silicon Nitride | PEEK | 518 N | 315 N | 800 C (1472F) |
63803 | Open | 17 mm | 26 mm | 7 mm | Silicon Nitride | PEEK | 558 N | 365 N | 800 C (1472F) |
63803 2rs | Sealed | 17 mm | 26 mm | 7 mm | Silicon Nitride | PEEK | 558 N | 365 N | 800 C (1472F) |
63804 | Open | 20 mm | 32 mm | 10 mm | Silicon Nitride | PEEK | 1005 N | 615 N | 800 C (1472F) |
63804 2rs | Sealed | 20 mm | 32 mm | 10 mm | Silicon Nitride | PEEK | 1005 N | 615 N | 800 C (1472F) |
63805 | Open | 25 mm | 37 mm | 10 mm | Silicon Nitride | PEEK | 1075 N | 735 N | 800 C (1472F) |
63805 2rs | Sealed | 25 mm | 37 mm | 10 mm | Silicon Nitride | PEEK | 1075 N | 735 N | 800 C (1472F) |
63806 | Open | 30 mm | 42 mm | 10 mm | Silicon Nitride | PEEK | 1134 N | 850 N | 800 C (1472F) |
63806 2rs | Sealed | 30 mm | 42 mm | 10 mm | Silicon Nitride | PEEK | 1134 N | 850 N | 800 C (1472F) |
6700 | Open | 10 mm | 15 mm | 3 mm | Silicon Nitride | PEEK | 214 N | 109 N | 800 C (1472F) |
6700 2rs | Sealed | 10 mm | 15 mm | 4 mm | Silicon Nitride | PEEK | 214 N | 109 N | 800 C (1472F) |
6701 | Open | 12 mm | 18 mm | 4 mm | Silicon Nitride | PEEK | 232 N | 133 N | 800 C (1472F) |
6701 2rs | Sealed | 12 mm | 18 mm | 4 mm | Silicon Nitride | PEEK | 232 N | 133 N | 800 C (1472F) |
6702 | Open | 15 mm | 21 mm | 4 mm | Silicon Nitride | PEEK | 234 N | 145 N | 800 C (1472F) |
6702 2rs | Sealed | 15 mm | 21 mm | 4 mm | Silicon Nitride | PEEK | 234 N | 145 N | 800 C (1472F) |
6703 | Open | 17 mm | 23 mm | 4 mm | Silicon Nitride | PEEK | 250 N | 164 N | 800 C (1472F) |
6703 2rs | Sealed | 17 mm | 23 mm | 4 mm | Silicon Nitride | PEEK | 250 N | 164 N | 800 C (1472F) |
6704 | Open | 20 mm | 27 mm | 4 mm | Silicon Nitride | PEEK | 252 N | 180 N | 800 C (1472F) |
6704 2rs | Sealed | 20 mm | 27 mm | 4 mm | Silicon Nitride | PEEK | 252 N | 180 N | 800 C (1472F) |
6705 | Open | 25 mm | 32 mm | 4 mm | Silicon Nitride | PEEK | 275 N | 210 N | 800 C (1472F) |
6705 2rs | Sealed | 25 mm | 32 mm | 4 mm | Silicon Nitride | PEEK | 275 N | 210 N | 800 C (1472F) |
6706 | Open | 30 mm | 37 mm | 4 mm | Silicon Nitride | PEEK | 285 N | 237 N | 800 C (1472F) |
6706 2rs | Sealed | 30 mm | 37 mm | 4 mm | Silicon Nitride | PEEK | 285 N | 237 N | 800 C (1472F) |
6707 | Open | 35 mm | 44 mm | 5 mm | Silicon Nitride | PEEK | 465 N | 408 N | 800 C (1472F) |
6707 2rs | Sealed | 35 mm | 44 mm | 5 mm | Silicon Nitride | PEEK | 465 N | 408 N | 800 C (1472F) |
6708 | Open | 40 mm | 50 mm | 6 mm | Silicon Nitride | PEEK | 628 N | 558 N | 800 C (1472F) |
6708 2rs | Sealed | 40 mm | 50 mm | 6 mm | Silicon Nitride | PEEK | 628 N | 558 N | 800 C (1472F) |
6709 | Open | 45 mm | 55 mm | 6 mm | Silicon Nitride | PEEK | 642 N | 600 N | 800 C (1472F) |
6709 2rs | Sealed | 45 mm | 55 mm | 6 mm | Silicon Nitride | PEEK | 642 N | 600 N | 800 C (1472F) |
6710 | Open | 50 mm | 62 mm | 6 mm | Silicon Nitride | PEEK | 668 N | 662 N | 800 C (1472F) |
6710 2rs | Sealed | 50 mm | 62 mm | 6 mm | Silicon Nitride | PEEK | 668 N | 662 N | 800 C (1472F) |
6800 | Open | 10 mm | 19 mm | 5 mm | Silicon Nitride | PEEK | 430 N | 210 N | 800 C (1472F) |
6800 2rs | Sealed | 10 mm | 19 mm | 5 mm | Silicon Nitride | PEEK | 430 N | 210 N | 800 C (1472F) |
6801 | Open | 12 mm | 21 mm | 5 mm | Silicon Nitride | PEEK | 480 N | 260 N | 800 C (1472F) |
6801 2rs | Sealed | 12 mm | 21 mm | 5 mm | Silicon Nitride | PEEK | 480 N | 260 N | 800 C (1472F) |
6802 | Open | 15 mm | 24 mm | 5 mm | Silicon Nitride | PEEK | 518 N | 315 N | 800 C (1472F) |
6802 2rs | Sealed | 15 mm | 24 mm | 5 mm | Silicon Nitride | PEEK | 518 N | 315 N | 800 C (1472F) |
6803 | Open | 17 mm | 26 mm | 5 mm | Silicon Nitride | PEEK | 558 N | 365 N | 800 C (1472F) |
6803 2rs | Sealed | 17 mm | 26 mm | 5 mm | Silicon Nitride | PEEK | 558 N | 365 N | 800 C (1472F) |
6804 | Open | 20 mm | 32 mm | 7 mm | Silicon Nitride | PEEK | 1005 N | 615 N | 800 C (1472F) |
6804 2rs | Sealed | 20 mm | 32 mm | 7 mm | Silicon Nitride | PEEK | 1005 N | 615 N | 800 C (1472F) |
6805 | Open | 25 mm | 37 mm | 7 mm | Silicon Nitride | PEEK | 1075 N | 735 N | 800 C (1472F) |
6805 2rs | Sealed | 25 mm | 37 mm | 7 mm | Silicon Nitride | PEEK | 1075 N | 735 N | 800 C (1472F) |
6806 | Open | 30 mm | 42 mm | 7 mm | Silicon Nitride | PEEK | 1112 N | 860 N | 800 C (1472F) |
6806 2rs | Sealed | 30 mm | 42 mm | 7 mm | Silicon Nitride | PEEK | 1112 N | 860 N | 800 C (1472F) |
6807 | Open | 35 mm | 47 mm | 7 mm | Silicon Nitride | PEEK | 1185 N | 955 N | 800 C (1472F) |
6807 2rs | Sealed | 35 mm | 47 mm | 7 mm | Silicon Nitride | PEEK | 1185 N | 955 N | 800 C (1472F) |
6808 | Open | 40 mm | 52 mm | 7 mm | Silicon Nitride | PEEK | 1232 N | 1045 N | 800 C (1472F) |
6808 2rs | Sealed | 40 mm | 52 mm | 7 mm | Silicon Nitride | PEEK | 1232 N | 1045 N | 800 C (1472F) |
6809 | Open | 45 mm | 58 mm | 7 mm | Silicon Nitride | PEEK | 1552 N | 1345 N | 800 C (1472F) |
6809 2rs | Sealed | 45 mm | 58 mm | 7 mm | Silicon Nitride | PEEK | 1552 N | 1345 N | 800 C (1472F) |
6810 | Open | 50 mm | 65 mm | 7 mm | Silicon Nitride | PEEK | 1542 N | 1440 N | 800 C (1472F) |
6810 2rs | Sealed | 50 mm | 65 mm | 7 mm | Silicon Nitride | PEEK | 1542 N | 1440 N | 800 C (1472F) |
6811 | Open | 55 mm | 72 mm | 9 mm | Silicon Nitride | PEEK | 2200 N | 2020 N | 800 C (1472F) |
6811 2rs | Sealed | 55 mm | 72 mm | 9 mm | Silicon Nitride | PEEK | 2200 N | 2020 N | 800 C (1472F) |
6812 | Open | 60 mm | 78 mm | 10 mm | Silicon Nitride | PEEK | 2875 N | 2650 N | 800 C (1472F) |
6812 2rs | Sealed | 60 mm | 78 mm | 10 mm | Silicon Nitride | PEEK | 2875 N | 2650 N | 800 C (1472F) |
6813 | Open | 65 mm | 85 mm | 10 mm | Silicon Nitride | PEEK | 2975 N | 2875 N | 800 C (1472F) |
6813 2rs | Sealed | 65 mm | 85 mm | 10 mm | Silicon Nitride | PEEK | 2975 N | 2875 N | 800 C (1472F) |
6814 | Open | 70 mm | 90 mm | 10 mm | Silicon Nitride | PEEK | 2900 N | 2950 N | 800 C (1472F) |
6814 2rs | Sealed | 70 mm | 90 mm | 10 mm | Silicon Nitride | PEEK | 2900 N | 2950 N | 800 C (1472F) |
6815 | Open | 75 mm | 95 mm | 10 mm | Silicon Nitride | PEEK | 3075 N | 3200 N | 800 C (1472F) |
6815 2rs | Sealed | 75 mm | 95 mm | 10 mm | Silicon Nitride | PEEK | 3075 N | 3200 N | 800 C (1472F) |
6816 | Open | 80 mm | 100 mm | 10 mm | Silicon Nitride | PEEK | 3150 N | 3325 N | 800 C (1472F) |
6816 2rs | Sealed | 80 mm | 100 mm | 10 mm | Silicon Nitride | PEEK | 3150 N | 3325 N | 800 C (1472F) |
6817 | Open | 85 mm | 110 mm | 13 mm | Silicon Nitride | PEEK | 4675 N | 4750 N | 800 C (1472F) |
6817 2rs | Sealed | 85 mm | 110 mm | 13 mm | Silicon Nitride | PEEK | 4675 N | 4750 N | 800 C (1472F) |
6818 | Open | 90 mm | 115 mm | 13 mm | Silicon Nitride | PEEK | 4575 N | 4875 N | 800 C (1472F) |
6818 2rs | Sealed | 90 mm | 115 mm | 13 mm | Silicon Nitride | PEEK | 4575 N | 4875 N | 800 C (1472F) |
6819 | Open | 95 mm | 120 mm | 13 mm | Silicon Nitride | PEEK | 4700 N | 5075 N | 800 C (1472F) |
6819 2rs | Sealed | 95 mm | 120 mm | 13 mm | Silicon Nitride | PEEK | 4700 N | 5075 N | 800 C (1472F) |
6900 | Open | 10 mm | 22 mm | 6 mm | Silicon Nitride | PEEK | 675 N | 318 N | 800 C (1472F) |
6900 2rs | Sealed | 10 mm | 22 mm | 6 mm | Silicon Nitride | PEEK | 675 N | 318 N | 800 C (1472F) |
6901 | Open | 12 mm | 24 mm | 6 mm | Silicon Nitride | PEEK | 722 N | 365 N | 800 C (1472F) |
6901 2rs | Sealed | 12 mm | 24 mm | 6 mm | Silicon Nitride | PEEK | 722 N | 365 N | 800 C (1472F) |
6902 | Open | 15 mm | 28 mm | 7 mm | Silicon Nitride | PEEK | 1082 N | 562 N | 800 C (1472F) |
6902 2rs | Sealed | 15 mm | 28 mm | 7 mm | Silicon Nitride | PEEK | 1082 N | 562 N | 800 C (1472F) |
6903 | Open | 17 mm | 30 mm | 7 mm | Silicon Nitride | PEEK | 1148 N | 640 N | 800 C (1472F) |
6903 2rs | Sealed | 17 mm | 30 mm | 7 mm | Silicon Nitride | PEEK | 1148 N | 640 N | 800 C (1472F) |
6904 | Open | 20 mm | 37 mm | 9 mm | Silicon Nitride | PEEK | 1595 N | 920 N | 800 C (1472F) |
6904 2rs | Sealed | 20 mm | 37 mm | 9 mm | Silicon Nitride | PEEK | 1595 N | 920 N | 800 C (1472F) |
6905 | Open | 25 mm | 42 mm | 9 mm | Silicon Nitride | PEEK | 1752 N | 1138 N | 800 C (1472F) |
6905 2rs | Sealed | 25 mm | 42 mm | 9 mm | Silicon Nitride | PEEK | 1752 N | 1138 N | 800 C (1472F) |
6906 | Open | 30 mm | 47 mm | 9 mm | Silicon Nitride | PEEK | 1810 N | 1252 N | 800 C (1472F) |
6906 2rs | Sealed | 30 mm | 47 mm | 9 mm | Silicon Nitride | PEEK | 1810 N | 1252 N | 800 C (1472F) |
6907 | Open | 35 mm | 55 mm | 10 mm | Silicon Nitride | PEEK | 2725 N | 1938 N | 800 C (1472F) |
6907 2rs | Sealed | 35 mm | 55 mm | 10 mm | Silicon Nitride | PEEK | 2725 N | 1938 N | 800 C (1472F) |
6908 | Open | 40 mm | 62 mm | 12 mm | Silicon Nitride | PEEK | 3425 N | 2480 N | 800 C (1472F) |
6908 2rs | Sealed | 40 mm | 62 mm | 12 mm | Silicon Nitride | PEEK | 3425 N | 2480 N | 800 C (1472F) |
6909 | Open | 45 mm | 68 mm | 12 mm | Silicon Nitride | PEEK | 3525 N | 2725 N | 800 C (1472F) |
6909 2rs | Sealed | 45 mm | 68 mm | 12 mm | Silicon Nitride | PEEK | 3525 N | 2725 N | 800 C (1472F) |
6910 | Open | 50 mm | 72 mm | 12 mm | Silicon Nitride | PEEK | 3625 N | 2925 N | 800 C (1472F) |
6910 2rs | Sealed | 50 mm | 72 mm | 12 mm | Silicon Nitride | PEEK | 3625 N | 2925 N | 800 C (1472F) |
6911 | Open | 55 mm | 80 mm | 13 mm | Silicon Nitride | PEEK | 4150 N | 3525 N | 800 C (1472F) |
6911 2rs | Sealed | 55 mm | 80 mm | 13 mm | Silicon Nitride | PEEK | 4150 N | 3525 N | 800 C (1472F) |
Full ball ceramic bearing
– no cage, so that ceramic balls can be added to the ball bearing to increase the radial load.
– Lower performance in high speed applications and therefore should not be used in applications requiring axial loads.

Ceramic cage full of ceramic bearings
– Ceramic cages and ceramic bearings have the characteristics of good wear resistance, corrosion resistance, high strength, lubrication-free, and maintenance-free. Works well in corrosive, low temperature or high vacuum areas.
– Cage is usually ZrO2
Hybrid ceramic bearings
When most people think of ceramic bearings, they are usually referring to hybrid ceramic bearings. Hybrid bearings are somewhere between fully ceramic and stainless steel bearings. Although they use ceramic balls, these bearings are paired with stainless steel inner and outer rings. Higher speeds can be achieved using this combination than all-ceramic options because the brittle metal rings are less prone to sudden catastrophic failure at high speeds or under load.
Although the design differences are nearly identical, the requirements for hybrid bearings are significantly different from fully ceramic bearings. For example, full ceramic bearings may not require lubrication, while hybrid bearings do. However, although ceramic balls will still wear steel rings, hybrid bearings can cope with edge lubrication better than steel bearings due to the balls’ low coefficient of friction and light weight.

Lubrication may not be required when using hybrid bearings at very low speeds. However, since these bearings are typically selected for higher speed applications than all-ceramic bearings, proper lubrication is recommended. Precision hybrid bearings with high-speed cages can withstand very high speeds and are therefore used in areas such as machine tool spindles. Corrosion resistance can also be affected when hybrid bearings are chosen instead of fully ceramic bearings. While ceramic balls are highly resistant to corrosion, due to the use of metal rings, even if they are stainless steel, the overall level of corrosion resistance is reduced. The decision to choose ceramic or hybrid bearings depends on cost, application and the severity of the environment in which the bearing will be used.
Stainless steel bearing is a bearing made of stainless steel material. Since stainless steel has good wear resistance, corrosion resistance and other characteristics, stainless steel bearings have the characteristics of long service life, low friction coefficient and high operating accuracy. Stainless steel bearings are generally made of 304 or 316 stainless steel. The difference between the two is that 316 stainless steel contains 2% to 3% molybdenum, and its corrosion resistance is better than that of 304 stainless steel. In addition, stainless steel bearings can also use some special stainless steel materials, such as SUS440C, SUS630, etc.

SUS420 stainless steel bearings.
420 stainless steel is a martensitic stainless steel with certain wear resistance and corrosion resistance and high hardness. Suitable for various bearings, precision machinery, electrical appliances, equipment, instruments, transportation vehicles, household appliances, etc. It is mainly used in environments resistant to atmospheric, water vapor, water and oxidizing acid corrosion, and is widely used in the bearing field.
The carbon content of martensitic stainless steel is higher than that of cr13 steel, so its strength and hardness are higher than cr13. Other properties are similar to cr13, but its weldability is poor, corrosion resistance and toughness are strong, and the rotation speed in micro bearings and bearings is higher, so SUS440 stainless steel bearings are widely used.
SUS630 stainless steel bearings.
630 stainless steel is a martensitic precipitation hardening stainless steel. 630 stainless steel has good attenuation properties and is highly resistant to corrosion fatigue and water droplets. Its corrosion resistance is equivalent to 304 stainless steel and its hardness is better than 304 stainless steel. It is suitable for the food industry. , offshore platforms, paper industry, medical equipment, washing equipment, environmentally friendly cleaning machinery, chemical machinery, etc., are widely used in fields with high pollution prevention requirements.
304 austenitic stainless steel has good corrosion resistance, heat resistance, low temperature strength and mechanical properties. It has good hot processing properties such as stamping and bending, and cannot be hardened by heat treatment. Non-magnetic 304 (processed weakly magnetic) stainless steel has good heat resistance and is widely used in the production of corrosion-resistant and formable equipment and parts. Currently, 304 stainless steel bearings are widely used in food processing machinery, chemical machinery, ship equipment, Medical equipment, washing equipment, environmentally friendly cleaning machinery and other fields.
316 austenitic stainless steel has plasticity, toughness, cold deformation, good welding process performance, and good glossy appearance of cold-rolled products. Due to the addition of Mo (2-3%), its pitting corrosion resistance is particularly excellent.
Ceramic Bearings vs Stainless Steel Bearings: Key Differences
Both stainless steel bearings and full ceramic bearings are corrosion-resistant, but ceramic bearings are corrosion-resistant. They can both handle higher temperatures than chromium steel, but ceramic bearings also win. Stainless steel bearings win due to load and speed ratings.
440 stainless steel bearings have moderate corrosion resistance but are resistant to many stronger chemicals and salt water. 316 stainless steel has higher chemical resistance and can be used offshore. Ceramics have superior corrosion resistance to many chemicals, including concentrated acids and bases, and can be permanently immersed in seawater without corroding. Ceramic bearings have the highest temperature ratings. Silicon nitride can withstand 800°C. Next is 316 stainless steel at 500°C, zirconia at 400°C, and finally 440 stainless steel at 300°C. For cryogenic use, 316 stainless steel wins at -250°C, followed by silicon nitride (-210°C), zirconium oxide (-190°C), and then 440 stainless steel (-70°C).
In terms of load and speed ratings, 440 stainless steel bearings are the clear winner. Fully ceramic zirconia bearings can support approximately 90% of the load and 20% of the speed of a 440 stainless steel bearing. Next the silicon nitride bearing has 75% load/25% speed. The obvious loser here is the much softer 316 stainless steel bearing with 15% load and about 6% speed.
Friction:
Since ceramic balls have no pores, they are rounder, lighter, harder and smoother than steel balls. This reduces friction and energy loss, allowing your equipment to run efficiently (and for longer) with ceramic ball bearings. Because ceramic ball bearings are relatively smooth, they require less lubrication than steel bearings.
Corrosion:
Even if well lubricated, steel balls will corrode over time, while ceramic balls will not corrode. In fact, even ceramic hybrid ball bearings may last up to ten times longer than steel bearings when it comes to corrosion.
Heavy load:
Ceramic balls are much less elastic than steel balls, which is something to keep in mind when considering upgrading your ceramic bearings. Ceramic balls are likely to cause damage (indentation) to bearing raceways if heavy loads are encountered. Over time, dents in the raceway will grow larger and eventually lead to failure.
Electrically insulating and non-magnetic
Ceramic bearings are non-magnetic and non-conductive, so they are often preferred in applications where conductivity is a concern, for example if you have an electric motor, traction motors and other electric motors controlled by a variable frequency drive, the current can cause serious damage to the normal bearings damage. Electrically insulating ceramic balls protect the steel ring from arc penetration. Additionally, fully ceramic bearings are non-magnetic. Therefore, they are often used in medical devices. However, stainless steel bearings are fully conductive and occasionally weakly magnetic.
Accuracy:
In terms of accuracy, the ABEC rating is high enough that the difference between ceramic and steel bearings is minimal. The only difference is that ceramic bearings do not thermally expand as much as steel bearings and therefore do not generate as much heat at high speeds or have as much measurable thermal growth.
Cost:
This is usually the biggest difference between ceramic bearings and steel bearings. Ceramic bearings are on average at least 50% expensive than stainless steel bearings. Therefore, stainless steel bearings are cost-effective than ceramic bearings.
Service life
The density of ceramic balls is lower than that of steel balls, but their hardness is much higher than that of steel balls. They are very wear-resistant: small particles that enter the bearing are simply crushed. They have very low rolling resistance, ensuring that very little heat is released. When it comes to the specific service life, it needs to be based on the use environment of the bearing. If you blurt it out, ceramic bearings generally have a longer service life than stainless steel bearings.
Advantages of hybrid ceramic bearings
Hybrid ceramic bearings perform very well when bearings need to operate under extreme conditions for a limited period of time. Due to the low adhesion between silicon nitride and steel, no micro-welding (sticking) occurs and the resistance to smears is very high, further eliminating the possibility of catastrophic failure.
High power output
When used in electric drives and industrial machine tools, hybrid ceramic bearings provide low friction and high-speed operation. Since the weight of silicon nitride is only 40% of the steel ball, the centrifugal force is lower. Reducing friction and lowering temperature rise can increase operating speed. Additionally, hybrid balls are lighter in weight, allowing for rapid acceleration and deceleration. Because hybrid ceramic bearings have about 30% less thermal expansion than steel, ceramic bearings are less sensitive to thermal differences between races. Ceramic balls also transfer less heat. All this means that cold ceramic bearings have less initial preload. This preload is not significantly affected by temperature increases.
Longer life
Hybrid ceramic bearings generally last longer than other bearing types. One reason is that, unlike all-steel bearings, ceramic balls have natural insulating properties that prevent arcing, which can cause a washboard or groove pattern on the raceway. This damage can produce excessive noise and premature lubrication aging. Hybrid bearings also allow for a wider range of speeds, allowing operators to meet the needs of specific jobs. Because ceramic bearings are less prone to static vibration (a common cause of false Brinell markings), there is much less risk of spalling and premature failure. Ceramic bearings can experience spalling and spalling, but hybrid ceramics generally have a much longer fatigue life than steel.
Environmental friendly
Because hybrid bearings perform well in lifetime lubricated applications and generally do not require oil lubrication, the chance of oil leakage into the environment is eliminated. Low-friction operation also requires less energy consumption. Due to their lubricity (the friction coefficient of hybrid bearings is approximately 20% that of comparable steel balls), hybrid bearings generate less vibration than all-steel bearings, thus reducing noise levels during operation. These advantages are an advantage when used in compressors, mixers, pumps and flow meters.
Low life cycle costs
Compared with all-steel bearings, hybrid bearings have longer service life, lower operating and maintenance costs, higher production quality, simpler operation and installation, and therefore lower life cycle costs. This is especially true when used with electric motors, stepper motors, encoders and pumps.
lubricating
Grease and oil are common lubricants for hybrid bearings, but ceramic bearings are less sensitive to fluctuations in lubrication conditions. For example, compared to steel bearings, ceramic balls can run at 20% higher speeds under the same lubrication conditions. Grease is the recommended lubricant for most ceramic bearing applications, except for applications running at high speeds. Grease is preferred because it remains on the bearings easily than oil and provides better protection against moisture and dirt. The most commonly used grease for ceramic bearings is mineral oil-based lithium grease, which is suitable for precision bearings. For high speed, high temperature and extended service life applications, synthetic lubricants are preferred. Regardless of the type of grease used, the amount of grease should not exceed 30% of the free space in the bearing. In high-speed applications, this amount should be less than 30%.

Ceramic bearings VS stainless steel bearings, which one?
When evaluating the performance of ceramic and stainless steel bearings, several key factors are of utmost importance, each affecting the functionality of these components:
Friction and Wear:
Ceramic bearings stand out for their low coefficient of friction. This reduced friction essentially reduces wear and extends the life of the bearing. These features not only increase efficiency but also reduce heat generation, especially for high-speed applications.
Heat resistance and thermal performance:
While ceramic bearings are praised for their heat resistance, steel bearings have commendable thermal properties. Steel bearings can dissipate heat effectively, but they may not handle extreme temperatures as adeptly as ceramic bearings.
Carrying capacity:
Steel bearings generally exhibit excellent load-carrying capabilities, especially under heavy-load operation. However, ceramic bearings, while sometimes exhibiting lower load capabilities, can maintain their structural integrity under extreme and variable conditions.
Operating efficiency, speed and vibration:
There are many factors that influence these parameters. Ceramic bearings have less friction, typically perform well at high speeds, and exhibit lower vibrations due to their smooth surface. Stainless steel bearings, while efficient, may not match ceramics in ultra-high-speed settings, but are versatile and reliable in a wide range of applications.
Anti-rust performance:
Even with regular lubrication, steel ball bearings can rust. Ceramic bearings, on the other hand, are completely corrosion-resistant. Therefore, they minimize the possibility of motor downtime and bearing failure. Ceramic hybrid ball bearings are designed to withstand extreme conditions without cracking or chipping.
Minimize friction:
High-grade ceramic balls are generally smoother, rounder, and lighter than steel balls. Motors equipped with ceramic ball bearings can run efficiently as it combines to reduce friction by up to 40%. This way, the machine can also run faster because the light weight of the bearings reduces the load on other related components. In addition, the superior smoothness of ceramic ball surfaces means they require less lubrication than steel bearings.
Current resistance:
Bearings used in electric motors controlled by variable frequency drives tend to have better current resistance. Compared to steel bearings, motors equipped with ceramic bearings can prevent arcing and other conditions.
Long life:
Based on service life, ceramic ball bearings may last ten times longer than steel bearings in the same motor. Compared with steel bearings, ceramic balls are less prone to expansion and vibration. Additionally, the smoother surface of ceramic bearings prevents raceway damage that can occur in steel bearings.
Cost:
Stainless steel bearings are not as expensive as ceramic bearings, but when you consider the superior service of the latter, it becomes a better choice. The higher cost of ceramic bearings can be forgiven due to their durable properties.
When is it worthwhile to invest in ceramic bearings?
High-value applications, such as laboratory equipment, have exact requirements that need to be met every time the application is used. Using the wrong components in such equipment can contaminate the research conditions or cause the study to stop altogether. This is the same as in medical equipment, where the contamination-free and non-magnetic properties of ceramic bearings are critical.
Take magnetic resonance imaging (MRI), an imaging technology primarily associated with hospital MRI scanners. The technology uses strong magnetic fields to generate two- or three-dimensional images of any living object. Standard steel bearings cannot be used in these scanners due to their magnetic properties, so ceramic bearings are the best choice for these high-value applications.
Likewise, as integrated circuit manufacturers strive to make their chips faster, smaller, and cheaper, semiconductor manufacturing equipment companies have become reliant on advanced ceramic components to achieve the required performance. Bearings made from silicon nitride instead of standard aluminum oxide (aluminum oxide) provide electrical insulation and good corrosion resistance. Silicon nitride has a similar resistivity and dielectric constant to aluminum oxide, but due to its microstructure, the material is much stronger. Fully ceramic bearings can accommodate the many challenging conditions present in the semiconductor production stage; from furnace temperatures approaching 1400 °C to the air quality of clean rooms 1. Suddenly, the added cost is clearly justified.
Zirconia or silicon nitride?
If fully ceramic bearings are right for you, which bearing material should you choose given that they can withstand the harshest environments? The two most common types are zirconium oxide (ZrO2) and silicon nitride (Si3N4), both of which have their own advantages and disadvantages.
While ceramic materials are harder than steel, they are also brittle, which means ceramic bearings have lower load and speed ratings. While zirconia has high fracture toughness and can withstand minor impact loads, silicon nitride is brittle and therefore should not withstand impact loads. Silicon nitride is corrosion resistant than zirconia and has a wider temperature range, although it is significantly expensive. Like silicon nitride, zirconia is not affected by water and most chemicals, but it should not be regularly exposed to steam as it will degrade over time.
Silicon nitride is a very hard but also very light material. It has excellent resistance to water, salt water and a wide range of acids and alkalis. It also has a very wide temperature range and is suitable for use in high vacuum applications. The extremely high hardness of silicon nitride also means greater brittleness, so impact or impact loading should be minimized to avoid the risk of cracking. Silicon nitride has been used as a primary material in a variety of aerospace applications. It’s worth noting that NASA’s space shuttles were originally built using steel bearings in the turbine pumps, which was not a good combination when the space shuttle, and especially its engines, experienced tremendous loads and temperatures.
Ceramic bearings made of ZrO (zirconia) are a tough ceramic material with expansion properties very similar to steel, although they are 30% lighter. This is an advantage when considering the fit of the shaft and housing in high temperature applications, as bearing expansion may mean the shaft no longer fits. ZrO2 bearings have higher strength and resistance to fracture at room temperature. They are also extremely waterproof, which means they are often used in marine applications, particularly where equipment is completely submerged, or where traditional steel bearings cannot cope with the load or speed.
Weighing whether a Si3N4 or a ZrO2 bearing is the right choice is a complex decision, but generally speaking, ZrO2 bearings are used in applications due to their extremely high corrosion resistance and tougher properties.
Conclusion
In summary, both ceramic bearings and steel bearings have their own advantages and disadvantages, and the choice between the two depends on the specific application requirements. Ceramic bearings offer excellent speed, low electrical conductivity, corrosion resistance and high temperature resistance. Stainless steel bearings, on the other hand, are generally cheaper, easier to source, have higher load capacities, and are easier to maintain. By considering specific application requirements, one can make an informed decision based on the respective advantages and disadvantages of ceramic and stainless steel bearings. Aubearing, China’s leading bearing manufacturer, provides high-quality ceramic bearings and stainless steel bearings. If you are interested, please send us an inquiry.